The Importance of Ovality in Centerless Grinding Insights from Industry Leaders
Centerless grinding is a critical manufacturing process used to achieve precise cylindrical parts with tight tolerances. In various industries, particularly in automotive, aerospace, and medical applications, the quality of the parts produced relies heavily on the grinding process's accuracy. Among the many factors that influence the outcomes of centerless grinding, ovality is an essential parameter that manufacturers must monitor closely to ensure product quality.
Understanding Ovality in Centerless Grinding
Ovality refers to the deviation of a cylindrical part from a perfect circle. In the context of centerless grinding, ovality occurs when the grinding process produces parts that are not uniformly round. This can arise from several factors, including improper setup of the grinder, inconsistent material removal rates, or variations in the workpiece's hardness. The presence of ovality not only jeopardizes the functional performance of a part but can also lead to increased wear of components and machinery over time.
Manufacturers need to understand that ovality can significantly affect a part's performance. For example, in rotating machinery, such as shafts, high ovality can cause imbalances that lead to vibration, noise, and accelerated wear of bearings. In hydraulic components, it can lead to leakage and reduced efficiency. Consequently, maintaining tight control over ovality during the grinding process is crucial.
Technology and Techniques to Minimize Ovality
Leading centerless grinding companies have developed various technologies and techniques aimed at minimizing ovality
. Advances in machine design, control systems, and grinding wheels have contributed significantly to improving roundness in ground parts.1. Machine Design Modern centerless grinders are equipped with sophisticated features that enhance stability and accuracy. For instance, some machines utilize rigid frameworks and advanced linear bearings to reduce vibration and maintain precise alignment throughout the grinding process. Additionally, the introduction of CNC (Computer Numerical Control) technology allows for more precise adjustments and real-time monitoring of the grinding parameters.
ovality in centerless grinder companies
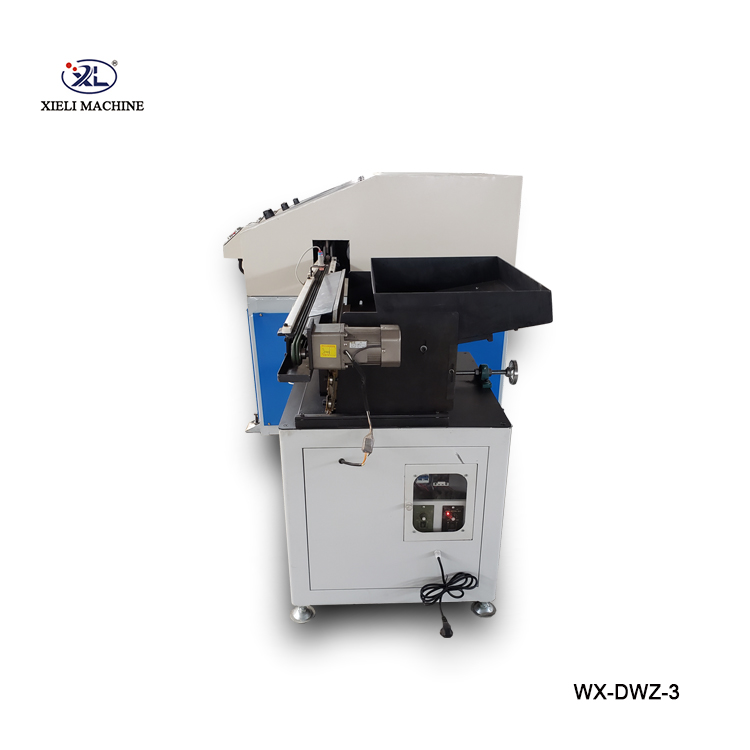
2. Grinding Wheel Selection The choice of grinding wheel plays a significant role in achieving minimal ovality. Precise selection of wheel composition, grit size, and hardness can help optimize material removal rates while maintaining the integrity of the workpiece. Manufacturers may even tailor grinding wheels based on the specific characteristics of the material being machined to ensure uniformity.
3. Process Parameters Establishing optimal grinding parameters, such as feed rate, infeed, and coolant application, is vital in controlling ovality. Advanced data analytics and process simulations further enable grinding companies to fine-tune these parameters based on the specific requirements of their production runs.
4. Quality Control Measures The incorporation of in-process measurement systems allows operators to assess ovality in real-time. Non-contact measurement technologies, such as laser measurement systems, can provide immediate feedback during production, allowing adjustments to be made proactively, thus preventing the production of out-of-spec parts.
Industry Experiences and Best Practices
Many prominent centerless grinding companies have shared their experiences and best practices regarding the management of ovality. For instance, some have implemented comprehensive training programs for operators, emphasizing the importance of machine setup and monitoring. By fostering a culture of quality and emphasizing the role each team member plays in reducing ovality, these companies have seen significant improvements in overall product quality.
Additionally, collaboration with material suppliers has also proven beneficial. By understanding the material properties and their influences on grinding performance, manufacturers can better anticipate and mitigate factors contributing to ovality.
Conclusion
In conclusion, ovality is a critical concern in the field of centerless grinding, impacting the quality and performance of machined parts across various industries. As technology continues to advance, manufacturers are better equipped to tackle the challenges posed by ovality. By focusing on machine design, grinding wheel selection, process parameters, and stringent quality control measures, companies can minimize the occurrence of ovality and enhance the reliability of their products. As the demand for precision components grows, so too will the emphasis on achieving perfect roundness through effective centerless grinding practices.