High-Quality Customized CNC Centerless Grinders
In the realm of modern manufacturing, precision and efficiency are paramount. One of the key players in achieving these goals is the Centerless Grinder, a specialized machine designed to grind cylindrical parts without the need for a fixed center point. With advancements in technology, the integration of Computer Numerical Control (CNC) has revolutionized traditional grinding methods, leading to the development of high-quality customized CNC centerless grinders that cater to specific industrial needs.
The Importance of Precision Grinding
The primary function of centerless grinding is to achieve high precision in the manufacturing of various components, including shafts, pins, and bushings. Unlike traditional methods, centerless grinding allows for continuous operation, which leads to improved productivity. The absence of a central axis enables the grinder to accommodate multiple workpieces simultaneously, making it an efficient choice for mass production.
Customization and Its Benefits
The demand for customization in industries like automotive, aerospace, and medical manufacturing has led to the creation of tailored CNC centerless grinders. These machines can be configured to meet the unique specifications of different applications, allowing manufacturers to optimize their production processes. Customization can include adjustments to grinding wheel size, spindle speeds, and loading methods, ensuring that the equipment meets the precise requirements of various materials and dimensions.
1. Enhanced Performance Customized centerless grinders are designed with specific tasks in mind, ensuring that they deliver peak performance. This tailored approach minimizes material wastage and reduces machining time, thus maximizing efficiency.
2. Adaptability Industries often require quick changes in production runs. Customized CNC centerless grinders can be easily reconfigured to accommodate different workpieces, providing manufacturers with the flexibility needed to meet changing market demands.
high quality customized cnc centerless grinder
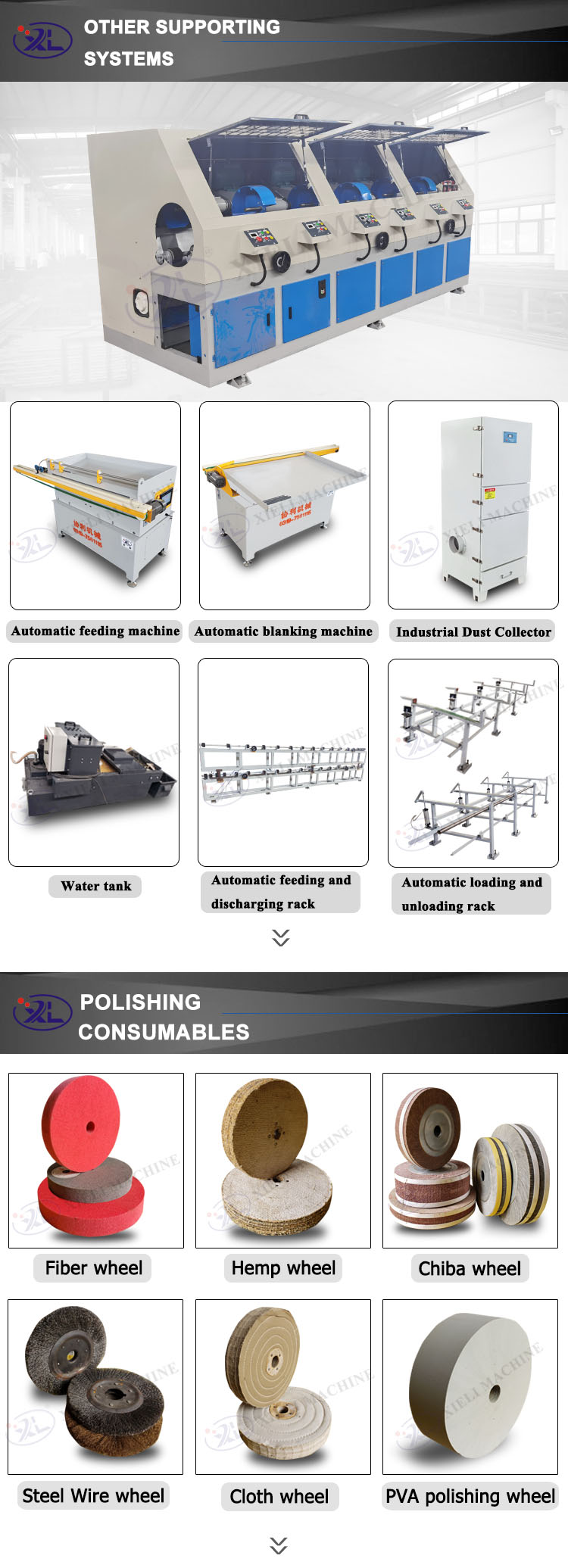
3. Consistent Quality When a grinder is customized for specific applications, it can consistently produce parts that meet stringent quality standards. This is particularly important in sectors where precision is critical, such as medical devices and automotive components.
The Role of Technology
The integration of advanced technology in CNC centerless grinders has further enhanced their capabilities. Features such as automated loading and unloading systems, real-time monitoring, and advanced software for process control facilitate superior manufacturing processes. These technological advancements enable the execution of complex operations with minimal human intervention, resulting in improved accuracy and reduced cycle times.
For instance, the use of sensors for in-process measurement helps to maintain tight tolerances and ensures that any deviations are promptly corrected. This not only enhances the quality of the finished product but also contributes to lower production costs.
Conclusion
The rise of high-quality customized CNC centerless grinders is a testament to the evolving landscape of manufacturing technology. By offering enhanced performance, adaptability, and consistent product quality, these machines play a vital role in elevating production capabilities across various industries. As manufacturers continue to seek innovative solutions to stay competitive in a global market, the importance of customized CNC centerless grinders will only grow.
In summary, the future of precision grinding lies in the ability to customize equipment to meet the specific demands of diverse applications. Embracing these customized CNC centerless grinders can lead to significant improvements in productivity, efficiency, and product quality, ultimately bolstering a manufacturer's success in an increasingly dynamic industry.