The Rise of Tube Internal Polishing Machine Factories A New Era of Precision and Quality
In the ever-evolving landscape of manufacturing, the demand for high-quality products persists, pushing industries to seek innovative solutions. Within this context, tube internal polishing machines have emerged as indispensable tools for various sectors, including aerospace, automotive, and medical equipment manufacturing. These machines ensure that tubes not only meet stringent aesthetic requirements but also uphold rigorous standards of functionality and performance. As a result, tube internal polishing machine factories have gained prominence, paving the way for enhanced production capabilities and improved product quality.
Understanding Tube Internal Polishing Machines
Tube internal polishing machines are specialized systems designed to enhance the inner surface of tubes through various polishing processes. The goal is to eliminate surface imperfections, improve finish quality, and achieve desired dimensional tolerances. These machines can operate using different methods, including mechanical polishing, chemical polishing, and abrasive polishing. Each technique is tailored to meet the specific materials and industry requirements, offering flexibility and precision.
The significance of these machines cannot be overstated. In industries like aerospace, for example, even a minute imperfection in a tube can lead to catastrophic failures. Consequently, manufacturers rely on advanced polishing machines to ensure the highest standard of quality in their products.
The Manufacturing Process
The establishment of a factory dedicated to producing tube internal polishing machines involves several critical stages, from design and prototyping to manufacturing and quality assurance
. The initial phase focuses on research and development, where engineers work to design machines that incorporate the latest technology and meet industry standards.Once prototypes are developed, rigorous testing occurs to ensure that the machines perform consistently under various conditions. After final adjustments, the mass production phase begins, where robotic automation and advanced manufacturing techniques are often employed. This enhances efficiency and allows for higher output without compromising quality.
Quality control is paramount in the manufacturing process. As machines are produced, factories implement strict inspection protocols to ensure that every unit meets the specified standards. Any deviations from quality criteria are addressed immediately, ensuring that only top-tier machines reach the market.
tube internal polishing machine factory
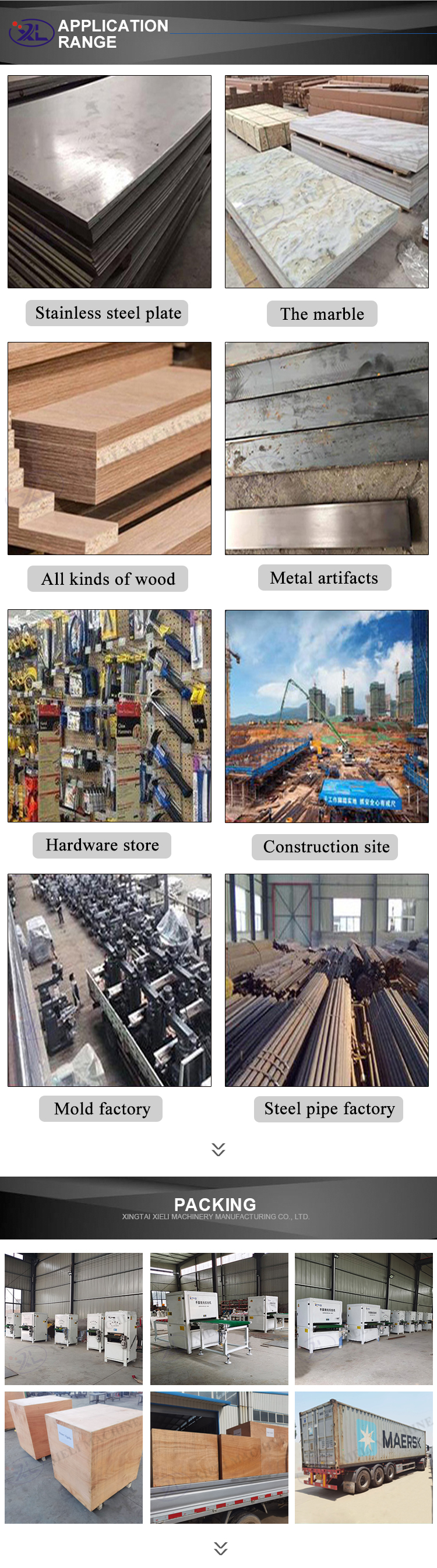
Innovations and Advancements
The factory landscape for tube internal polishing machines has not remained stagnant. Continuous advancements in technology, such as computer numerical control (CNC) systems and robotics, have revolutionized the production and efficiency of these machines. CNC technology allows for precise control over polishing processes, resulting in uniform finishes and reduced processing times.
Moreover, the integration of artificial intelligence and machine learning can enhance the operational capabilities of polishing machines. By collecting data throughout the polishing process, manufacturers can analyze performance metrics, predict maintenance needs, and optimize production schedules, all leading to greater efficiency and lower operational costs.
The Global Market and Future Prospects
The global market for tube internal polishing machines is expanding, driven by growth in industries such as energy, construction, and biotechnology. As regulations around safety and standards become more stringent, the demand for precision-engineered components will only increase, further bolstering the need for specialized polishing machines.
For factories producing these machines, the future looks promising. By investing in research and development and embracing new technologies, manufacturers can stay ahead of the curve, addressing market demands and fostering innovation. Collaborations between manufacturers, researchers, and industry stakeholders will also play a key role in shaping the future of tube internal polishing technology.
Conclusion
In conclusion, tube internal polishing machine factories are crucial players in the manufacturing sector, facilitating the production of high-quality tubular components across multiple industries. As technology progresses and market demands evolve, these factories will continue to innovate, ensuring that they meet the rigorous standards of tomorrow. The journey toward perfection in manufacturing is ongoing, and tube internal polishing machines are at the forefront of this quest for quality and precision.