Custom Pipe and Tube Polishing Machine Enhancing Surface Finish and Quality
In the world of manufacturing, the importance of surface finish cannot be overstated. Pipes and tubes are integral components in various industries, including automotive, aerospace, medical, and construction. A custom pipe and tube polishing machine plays a critical role in ensuring that these essential components meet stringent quality standards. This article explores the significance of polishing machines, their features, and the advantages of customization.
The Importance of Polishing
Polishing is an essential step in the fabrication process, particularly for metal pipes and tubes. The primary goal is to enhance the surface finish, which not only improves aesthetics but also increases the durability and performance of the products. A well-polished surface reduces the risk of corrosion, promotes better fluid flow in pipes, and ensures that components are free from surface irregularities that could lead to premature failure.
Moreover, in industries such as food processing and pharmaceuticals, polished surfaces are imperative for maintaining hygiene and preventing contamination. Any roughness on the surface can harbor bacteria, making it vital to have a smooth finish. Therefore, investing in a reliable polishing machine is a necessity for manufacturers aiming for high-quality output.
Features of Custom Pipe and Tube Polishing Machines
Custom pipe and tube polishing machines are designed to address the specific needs of different manufacturers and industries. These machines can vary greatly in size, capability, and technology. Some key features include
2. Multi-Head Configurations Many customized machines come with multiple polishing heads, which can simultaneously work on several components in different orientations. This feature significantly increases productivity and efficiency.
3. Versatile Abrasive Materials Custom polishing machines can utilize various abrasive materials, from traditional bonded abrasives to advanced non-woven materials. This versatility allows for tailored polishing that meets the specific requirements of each job.
custom pipe and tube polishing machine
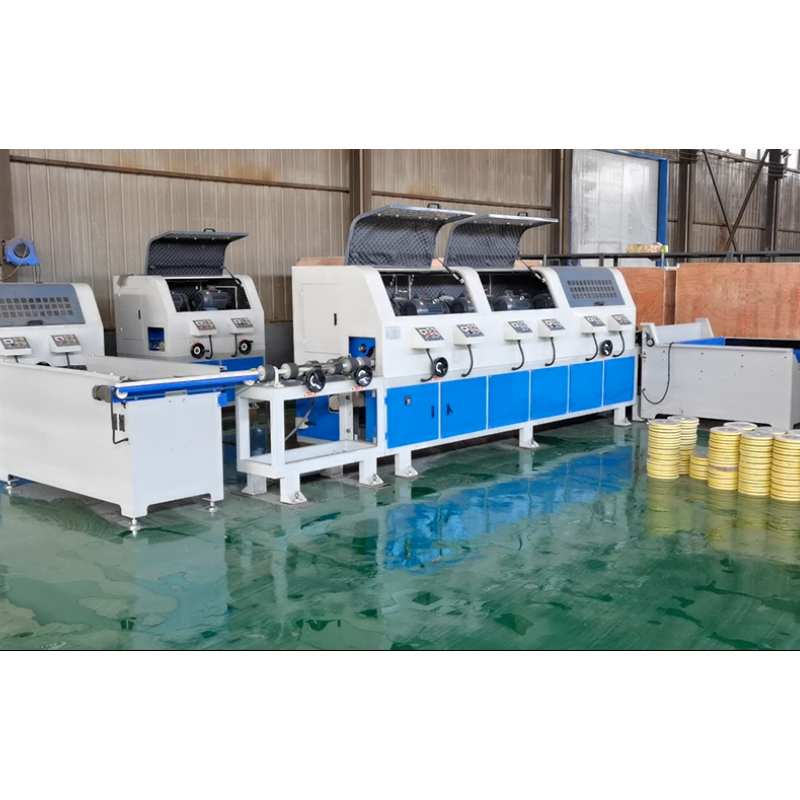
4. Robust Automation The integration of automation and robotics in modern polishing machines enhances precision and repeatability. Custom solutions can incorporate advanced control systems that monitor and adjust the polishing process in real-time.
5. User-Friendly Interfaces Many machines are designed with user-friendly controls, enabling operators to easily set parameters, monitor progress, and make adjustments as needed.
Advantages of Customization
The ability to customize polishing machines offers several advantages for manufacturers
1. Increased Efficiency Custom machines are designed to fit seamlessly into existing production lines, resulting in minimized downtime and enhanced productivity.
2. Tailored Solutions Every manufacturer has unique processes and requirements. Customized machines are built to meet these specific needs, ensuring optimal performance and output quality.
3. Cost-Effectiveness Although the initial investment might be higher, the long-term benefits of efficiency, reduced waste, and enhanced quality often lead to cost savings over time.
4. Improved Quality Control Custom polishing machines can incorporate features that ensure consistent quality, reducing the likelihood of defects and enhancing overall product reliability.
Conclusion
Custom pipe and tube polishing machines are indispensable in modern manufacturing. They not only enhance the surface finish of critical components but also contribute significantly to maintaining quality standards across a variety of industries. By investing in customized solutions, manufacturers can enjoy increased efficiency, tailored functionalities, and improved overall performance, ultimately leading to better products and greater customer satisfaction.