The Evolution of Small Centerless Grinding Machines
In the realm of precision machining, small centerless grinding machines have emerged as pivotal tools for a variety of industries, including automotive, aerospace, and medical device manufacturing. These machines excel at producing cylindrical components with tight tolerances and superior surface finishes. As automation and precision manufacturing continue to evolve, the demand for compact, efficient grinding solutions has significantly increased.
Centerless grinding is a process that utilizes two wheels a grinding wheel and a regulating wheel, which enables the workpiece to be ground on its outer surface without requiring any fixturing. This unique design allows for continuous grinding, where multiple parts can be fed through the machine in succession. The small centerless grinding machine is designed to accommodate shorter workpieces and tighter production spaces, making it an ideal choice for small-scale production runs and intricate applications.
One of the key benefits of small centerless grinding machines is their ability to achieve high levels of precision and consistency. With advancements in technology, these machines are now equipped with sophisticated CNC (Computer Numerical Control) systems that allow for programmable settings and repeatable processes. This capability dramatically reduces setup times and enhances productivity, ensuring that manufacturers can meet the increasing demands of their clients without compromising quality.
small centerless grinding machine quotes
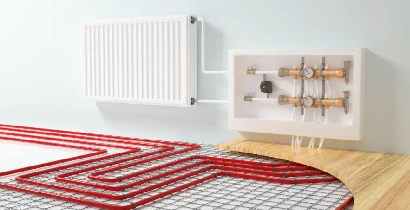
Moreover, the compact size of small centerless grinding machines makes them an attractive option for facilities with limited floor space. Manufacturers can integrate multiple grinding stations within a small footprint, optimizing their production lines and maximizing efficiency. This flexibility is essential for businesses looking to adapt to changing market conditions and customer requirements.
Another significant advantage of modern small centerless grinding machines is their energy efficiency. Many new models are designed with energy-saving features and lower operational costs. Manufacturers are increasingly focused on minimizing their environmental impact, and investing in these machines can contribute to sustainability efforts within the industry.
Furthermore, the evolution of small centerless grinding technology has introduced innovations such as improved cooling and filtration systems. These advancements help prolong the lifespan of consumables, reduce waste, and maintain the integrity of the grinding process. By ensuring that the workpieces are cooled effectively, manufacturers can avoid thermal distortions that might lead to dimensional inaccuracies, thus preserving the high-quality standards expected in precision machining.
In conclusion, small centerless grinding machines represent a significant advancement in the field of manufacturing. Their compact design, precision capabilities, and adaptability to various production environments make them an indispensable tool for many industries. As technology continues to advance, these machines will undoubtedly evolve further, incorporating more sophisticated features that will enhance their efficiency and performance. For manufacturers seeking to maintain a competitive edge, investing in small centerless grinding machines is a strategic move that promises long-term benefits and improved production outcomes.