The Evolution and Importance of OEM Flat Polishing Machines
In contemporary manufacturing, the quest for precision and efficiency has driven the development of advanced machinery tailored to meet the specific demands of various industries. Among these innovations, the OEM flat polishing machine has emerged as a critical tool, particularly in sectors that require high-tolerance surfaces and smooth finishes. This article explores the evolution of OEM flat polishing machines, their functionalities, and their importance in different industrial applications.
Understanding OEM Flat Polishing Machines
OEM, or Original Equipment Manufacturer, implies that the manufacturer produces equipment that can be rebranded and sold by another company. In the context of flat polishing machines, these are specialized devices designed for polishing flat surfaces of materials such as metal, glass, ceramics, and composites. Typically, these machines are indispensable in sectors like automotive, aerospace, electronics, and manufacturing, where surface finish and precision are paramount.
Flat polishing machines work by utilizing various polishing techniques, which can include mechanical polishing, chemical polishing, or a combination of both. They are equipped with abrasives and often feature adjustable settings that allow operators to control the speed, pressure, and duration of the polishing process. This flexibility ensures that the machines can cater to a wide range of materials and specifications, making them versatile assets in any workshop.
The Evolution of Polishing Technology
The journey of flat polishing machines began with rudimentary tools operated manually. These early devices laid the groundwork for more sophisticated machinery. However, as industries rapidly advanced, the limitations of manual polishing became evident—primarily concerning efficiency, uniformity, and the ability to meet stringent quality standards.
With the advent of automation and computer-controlled technologies, the design and performance of flat polishing machines were transformed. Today’s equipment often incorporates advanced features such as CNC (Computer Numerical Control) systems, which enable precise control over the polishing process and optimize the path taken by the polishing tool. This not only enhances the quality of the finish but also significantly reduces the time required for processing, allowing manufacturers to keep pace with increasing production demands.
Importance in Various Industries
oem flat polishing machine
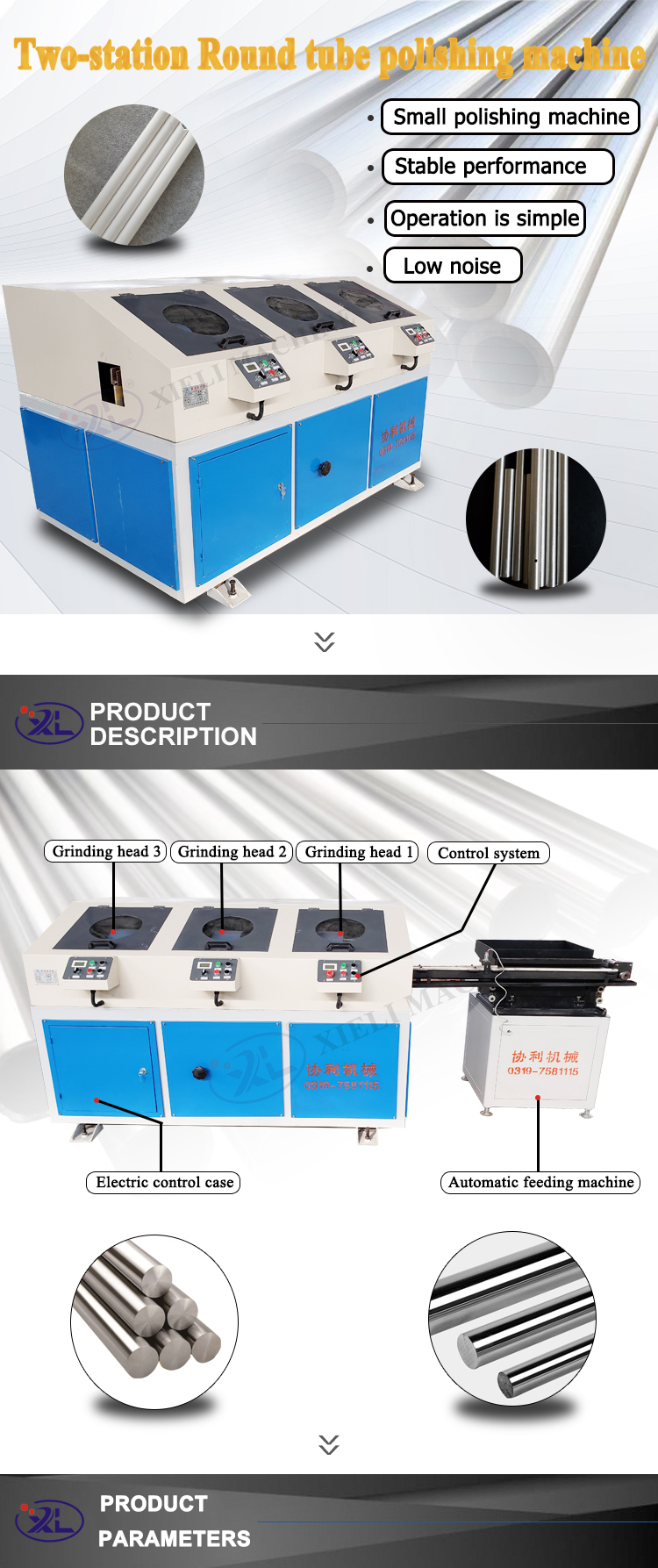
The significance of OEM flat polishing machines can be observed across different sectors. In the aerospace industry, for example, components such as turbine blades require impeccable surface finishes to improve aerodynamics and reduce wear. Flat polishing machines provide the necessary precision to achieve these requirements, helping to enhance the performance and lifespan of crucial aircraft components.
Similarly, in the electronics sector, the demand for flat polished surfaces is growing, particularly for circuit boards and components that require excellent thermal and electrical conductivity. Any imperfections on these surfaces can lead to performance issues. Therefore, the reliability of OEM flat polishing machines in meeting these stringent specifications is critical for maintaining the integrity of electronic devices.
The automotive industry also heavily relies on flat polishing machines. When preparing surfaces for painting or coating, achieving a smooth finish is essential to ensure adhesion and visual appeal. Polished surfaces contribute significantly to the aesthetics of vehicles, adding to their market value.
Future Trends in Flat Polishing Technology
As industries evolve, so too do the requirements placed on machinery. The future of OEM flat polishing machines will likely involve greater integration of smart technologies, such as IoT (Internet of Things) capabilities. This would allow for real-time monitoring and predictive maintenance, increasing efficiency and reducing downtime.
Moreover, advancements in materials science might lead to the development of more durable and efficient abrasives, further enhancing the polishing process. The incorporation of artificial intelligence could also play a role in optimizing polishing parameters, adapting processes dynamically based on real-time feedback.
Conclusion
OEM flat polishing machines represent a vital component in the machinery landscape of modern manufacturing. Their evolution reflects broader technological advancements and the increasing demand for quality and precision across diverse sectors. As these machines continue to adapt to the needs of the industry, their role will undoubtedly become even more integral, ensuring that manufacturers can deliver high-quality products that meet the expectations of consumers worldwide.