Centerless surface grinders have become essential in various industries, offering precision, efficiency, and remarkable consistency for high-volume production. However, understanding the price list of these advanced machines can be challenging due to several influencing factors. This comprehensive guide will offer insights into the cost structure of centerless surface grinders, including key variables that impact pricing, to help businesses make informed purchasing decisions.
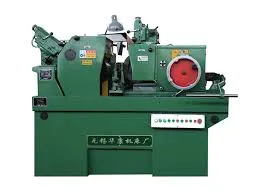
The price of a centerless surface grinder is determined by its technical specifications and features. High-end machines, equipped with automated controls and advanced technology, often come with premium pricing. These models are ideal for operations requiring precision engineering and high throughput. For instance, grinders with CNC controls enhance accuracy and reduce manual intervention, leading to a higher initial investment but potentially lower operational costs over time.
The type of material being processed also plays a significant role in price determination. Grinders designed to handle tough or specialized materials, such as hard metals or composite substances, typically require robust construction and additional features, which can drive up the cost. Additionally, the grinder's wheel diameter and width are critical specifications, as larger wheels often correlate with higher prices due to increased material costs and manufacturing complexities.
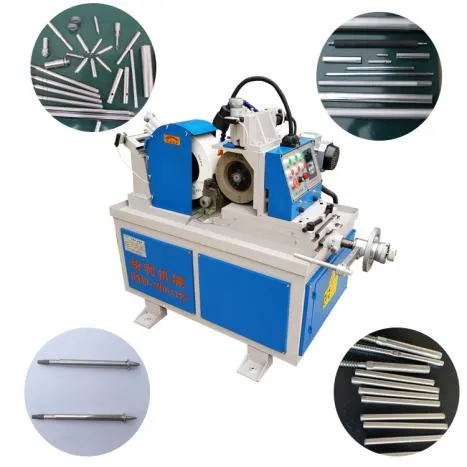
Brand reputation is another crucial factor. Established brands with a track record of reliability and innovative technology often command higher prices. These companies offer comprehensive customer support, warranties, and service packages that enhance the machine's overall value. On the other hand, newer or lesser-known brands may offer competitive pricing but require cautious evaluation regarding quality and after-sales support.
centerless surface grinder pricelist
Customization options significantly impact the pricing of centerless surface grinders. Manufacturers often offer tailor-made solutions to meet specific operational needs, from bespoke configurations to unique tooling systems. While these options provide operational flexibility, they can substantially increase the price compared to standard models.
Geographic location and market demand also influence pricing. In regions with high demand and limited supply, prices may surge. Conversely, areas with competitive markets might offer more favorable pricing due to competition among suppliers.
To ensure a sound investment, businesses are encouraged to evaluate their production needs and budget constraints comprehensively. It is advisable to conduct a cost-benefit analysis, considering factors such as expected throughput increases, labor cost savings, and product quality improvements associated with more advanced grinders. Engaging with industry experts, seeking peer recommendations, and evaluating supplier credibility and post-sales support can further enhance purchasing decisions.
Ultimately, while the initial cost of a centerless surface grinder is a significant consideration, the total cost of ownership, including maintenance, operation, and potential production benefits, should be carefully weighed. By thoroughly understanding these factors, businesses can select a grinder that aligns with their operational objectives and offers the best return on investment.
For More Details Pls Contact Us
Fiberglass Reinforced Plastic (FRP), also known as fiber-reinforced plastic, is a composite material widely used across various industries.