High-Quality Pipe Inside Polishing Machine Revolutionizing Pipe Finishing Processes
In the world of manufacturing and metalworking, the finishing process of pipes is crucial for ensuring optimal performance and aesthetic appeal. A high-quality pipe inside polishing machine plays a significant role in achieving these objectives. These machines are designed to enhance the inner surface of metal pipes, improving their quality and functionality while ensuring they meet stringent industry standards. This article explores the features, benefits, and advancements associated with high-quality pipe inside polishing machines.
Understanding the Purpose of Pipe Polishing
The primary purpose of polishing the inside of pipes is to achieve a smooth surface finish, thereby reducing the likelihood of corrosion and enhancing fluid flow efficiency. Rough or uneven surfaces can lead to increased turbulence, which can negatively impact processes such as fluid transport, heat exchange, and overall system efficiency. Polishing also contributes to aesthetics, especially in visible installations, where the appearance of piping can influence the overall design of a facility.
Features of High-Quality Pipe Inside Polishing Machines
Modern pipe polishing machines come equipped with a range of advanced features that enhance their efficiency and effectiveness. One of the most significant advancements is the incorporation of computer numerical control (CNC) technology. CNC machines allow for precise control over the polishing process, ensuring uniformity across different pipe sections and reducing human error. This precision is particularly important in industries such as aerospace, automotive, and pharmaceuticals, where strict tolerances are a requirement.
Additionally, high-quality polishing machines often feature adjustable settings that cater to various pipe materials and sizes. Whether dealing with stainless steel, carbon steel, or specialized alloys, these machines can be calibrated to provide optimal polishing results. The ability to handle different diameters and wall thicknesses makes these machines versatile and suitable for a wide range of applications.
Benefits of Using Pipe Inside Polishing Machines
high quality pipe inside polishing machine
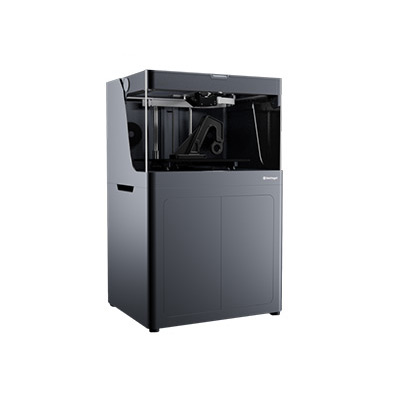
Investing in a high-quality pipe inside polishing machine brings numerous benefits to manufacturers. Firstly, improved productivity is a significant advantage. Automated polishing processes reduce the time and labor needed to achieve desired surface finishes, allowing companies to increase their production rates. This efficiency can lead to substantial cost savings and a faster return on investment.
Secondly, the enhancement of pipe quality cannot be overstated. The smooth internal surfaces achieved through polishing reduce friction and prevent the buildup of deposits, leading to improved flow characteristics. This factor is particularly crucial in industries where the movement of fluids is essential, such as oil and gas, chemical processing, and food and beverage.
Furthermore, polished pipes have a longer service life, as the reduction in surface roughness decreases the likelihood of corrosion. This longevity translates to lower maintenance costs and reduced downtime, allowing businesses to operate more effectively.
Technological Innovations in Pipe Polishing
Technological innovations continue to shape the capabilities of pipe inside polishing machines. Recent advancements include the integration of robotic systems and automation, allowing for increased consistency and repeatability in the polishing process. These machines can be programmed to perform complex polishing paths and adapt to various pipe geometries, further enhancing productivity.
Moreover, the development of eco-friendly polishing solutions and advanced abrasives is leading to more sustainable practices in pipe finishing. These innovations not only improve performance but also reduce environmental impact, aligning with the increasing focus on sustainability in manufacturing.
Conclusion
In conclusion, high-quality pipe inside polishing machines are essential tools in the metalworking industry, transforming the way pipes are finished and enhancing overall product quality. With advancements in technology, these machines now offer unparalleled precision, efficiency, and versatility, catering to a wide range of applications. By investing in such sophisticated equipment, manufacturers can improve their operational excellence, ensure compliance with industry standards, and deliver superior products to their customers. As the industry continues to evolve, the importance of efficient and effective pipe polishing processes will only grow, solidifying the role of these machines as invaluable assets in modern manufacturing.