The Importance of Coolant Systems in Custom Centerless Grinders
In the world of precision manufacturing, centerless grinding plays a crucial role in shaping and finishing delicate components. Custom centerless grinders are designed to handle specific tasks unique to particular industries and applications. A key aspect of maintaining the high efficiency and longevity of these machines is the use of effective coolant systems. Coolants not only contribute to the grinding process but significantly influence the quality of the finished product, machine performance, and operational safety.
Understanding Centerless Grinding
Before delving into the coolant systems, it is essential to understand the basic operation of a centerless grinder. Unlike conventional grinding machines where the workpiece is held between two centers, centerless grinding employs a simpler method. The workpiece is situated on a support blade, while the grinding wheel and regulating wheel rotate around it. This unique setup allows for the continuous processing of cylindrical parts without the need for manual tightening or repositioning.
The Role of Coolant in Centerless Grinding
During the grinding process, significant amounts of heat are generated due to friction between the grinding wheel and the workpiece. Without proper cooling, excessive heat can lead to several detrimental issues, including
1. Thermal Distortion High temperatures can cause the workpiece to expand, leading to dimensional inaccuracies. Precise specifications are critical in many manufacturing sectors, making thermal stability essential.
2. Wheel Wear Heat can degrade the grinding wheel’s material, diminishing its cutting efficiency and leading to premature wear. Effective cooling helps to extend the life of both the wheel and the machine.
3. Workpiece Integrity Excessive grinding heat can alter the material properties of the workpiece, reducing its strength and potential lifespan. Proper coolant application preserves the integrity of the components being machined.
4. Surface Finish Quality Adequate cooling helps in achieving a finer surface finish by preventing burn marks and discoloration on the machined part. A high-quality finish is often a requirement in industries like automotive and aerospace.
Types of Coolants
In custom centerless grinding, the choice of coolant can significantly affect the grinding performance
. Several types of coolants are commonly usedcustom centerless grinder coolant
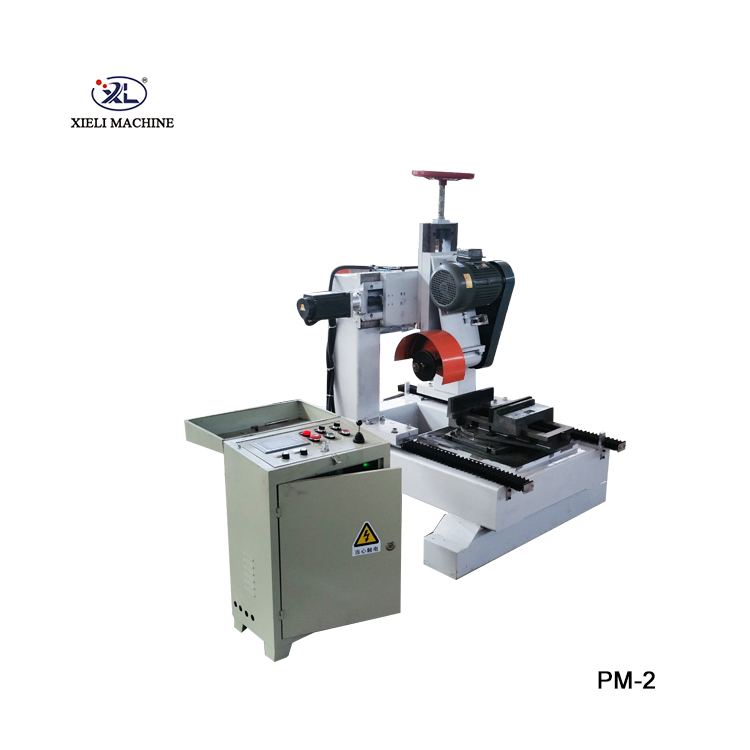
1. Water-Soluble Fluids These are popular due to their easier application and cooling properties. They disperse heat quickly and provide sufficient lubrication for the grinding process.
2. Oil-Based Fluids Although more viscous, oil-based coolants offer excellent lubrication but may not dissipate heat as efficiently as water-soluble options.
3. Synthetic Coolants A newer category, synthetic coolants combine properties of both water-soluble and oil-based fluids. They often have superior cooling characteristics and help maintain cleanliness in the machine.
Implementing an Effective Coolant System
To ensure the optimal performance of coolant systems in custom centerless grinders, manufacturers should consider the following
1. Regular Maintenance The coolant system must be regularly checked for cleanliness and effectiveness. Contaminated coolant can lead to bacterial growth and poor grinding performance.
2. Optimal Flow Rate Managing the flow rate of coolant to the grinding area is crucial. Too much coolant can lead to swirl and disrupt the grinding process, while too little can cause overheating.
3. Filtration Systems Installing appropriate filtration can prevent the recirculation of debris back into the coolant, which can contaminate both the workpiece and grinding wheel.
4. Temperature Control Monitoring coolant temperature via cooling systems ensures that the fluid remains within a functional range, thus preserving its effectiveness.
Conclusion
Incorporating an efficient coolant system into custom centerless grinding operations is not simply a matter of convenience but a necessity for ensuring precision, performance, and safety. By understanding the importance of coolant and selecting the right type for specific applications, manufacturers can optimize their grinding processes, enhance the longevity of their equipment, and guarantee high-quality outputs that meet stringent industry standards. Whether it's through careful selection of coolants, regular maintenance, or strategic implementation, the benefits of good coolant management cannot be overstated in the precision manufacturing landscape.