The Importance of 340-20% Centerless Grinder Service
In the intricate world of manufacturing and machining, precision is paramount. Among the various tools that contribute to achieving such precision, the centerless grinder stands out as an essential equipment piece. This article will delve into the significance of maintaining and servicing the 340-20% centerless grinder, focusing on the benefits of regular maintenance, common issues, and best practices for servicing.
Understanding the Centerless Grinder
A centerless grinder is a type of grinding machine that allows the workpiece to be fed through the grinding wheels without needing a centering device. This method enables high-volume production of cylindrical parts, making it a preferred choice for manufacturers dealing with components that require tight tolerances and consistent quality. The 340-20% model represents a specific type of centerless grinder known for its efficiency and precision in grinding operations.
The Need for Regular Service
Like any other piece of machinery, the 340-20% centerless grinder requires regular service to ensure optimal performance. Over time, wear and tear can impact the grinding wheels, bearings, and drive systems, leading to decreased efficiency and potential operational hazards. By conducting routine maintenance, manufacturers can identify potential problems before they escalate, ensuring that the machine runs smoothly and maintains the high quality of output.
Common Issues Faced
Several common issues can arise with centerless grinders, including
1. Grinding Wheel Wear The grinding wheel is one of the most critical components of a centerless grinder. Over time, the wheel can become worn out or damaged, leading to poor grinding performance and compromised part quality. Regular monitoring and timely replacement of grinding wheels are essential.
2. Misalignment The precision of a centerless grinder heavily relies on the alignment of its components. Misalignment can lead to inconsistency in the parts being produced. Routine checks and adjustments can help in maintaining proper alignment.
3. Hydraulic System Problems Centerless grinders often use hydraulic systems to control the movement of the workpiece and grinding wheels. Any leaks or failures in the hydraulic system can lead to significant downtime and the need for costly repairs.
340-20 centerless grinder service
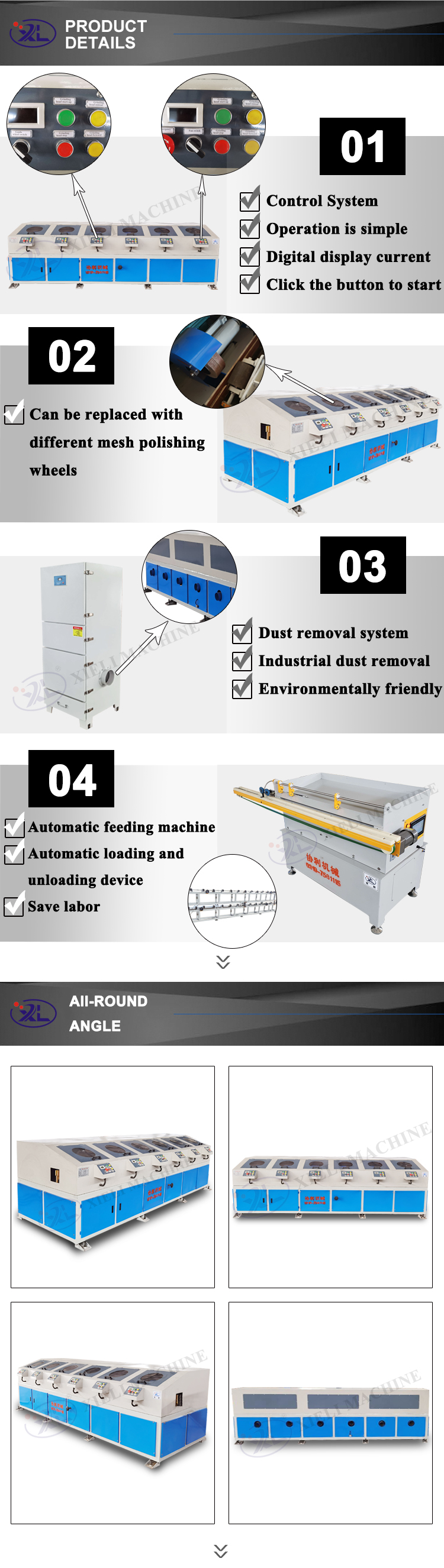
4. Vibration Issues Excessive vibration can affect the grinding process, leading to surface imperfections on the machined parts. Regular servicing can help identify and rectify any issues contributing to vibrations.
Best Practices for Service
To keep the 340-20% centerless grinder in optimal condition, here are some best practices
1. Regular Inspections Schedule routine inspections to check for wear and tear on critical components, assess alignment, and ensure that all hydraulic systems are functioning correctly.
2. Replace Worn Parts Promptly Address any signs of wear and replace grinding wheels, belts, and other consumables before they lead to operational failures.
3. Lubrication Proper lubrication of moving parts is crucial for ensuring smooth operation and prolonging the lifespan of the machine. Follow the manufacturer’s recommendations for lubrication intervals and types of lubricants.
4. Calibration Regularly calibrate the machine to ensure that it maintains the desired tolerances for precision grinding. This process is essential for producing parts that meet stringent quality standards.
5. Training and SOPs Ensure that staff operating the grinder are well-trained and familiar with standard operating procedures (SOPs). Proper training can prevent accidents and improper usage that can lead to machine damage.
Conclusion
In conclusion, the 340-20% centerless grinder is an invaluable tool in the manufacturing process, but like all machinery, it requires diligent care and maintenance. By understanding the importance of regular servicing, recognizing common issues, and following best practices, manufacturers can enhance the reliability and efficiency of their grinding operations. Regular service not only extends the life of the machine but also ensures the consistent production of high-quality components, ultimately contributing to the success of the manufacturing process as a whole. Investing in the maintenance of centerless grinders is, therefore, an investment in the overall quality and efficiency of production.