The Importance of High-Quality Coolant in Centerless Grinding
Centerless grinding is a precision process that plays a pivotal role in various manufacturing industries, from automotive to aerospace. This technique involves the grinding of cylindrical parts without the need for a fixture to hold the workpiece, allowing for high-volume production and reduced operational costs. However, to ensure optimal performance and longevity of machinery, the use of high-quality coolant in the centerless grinding process is essential.
Coolant serves multiple critical functions in centerless grinding. Primarily, it acts as a lubricant, reducing friction between the grinding wheel and the workpiece. This lubrication minimizes wear and tear on both the grinder and the material being processed, thus extending the equipment's lifespan and enhancing the quality of the finished product. A suitable coolant helps maintain a consistent and even grinding surface, which is vital for achieving tight tolerances that many industries require.
The Importance of High-Quality Coolant in Centerless Grinding
Moreover, coolant aids in chip removal during the grinding process. Efficient chip evacuation is crucial for maintaining productivity and preventing the accumulation of debris that can adversely affect the grinding operation. High-quality coolants are designed to enhance chip flow, preventing clogging and ensuring a clean workspace, which ultimately leads to improved grinding efficiency.
high quality centerless grinder coolant
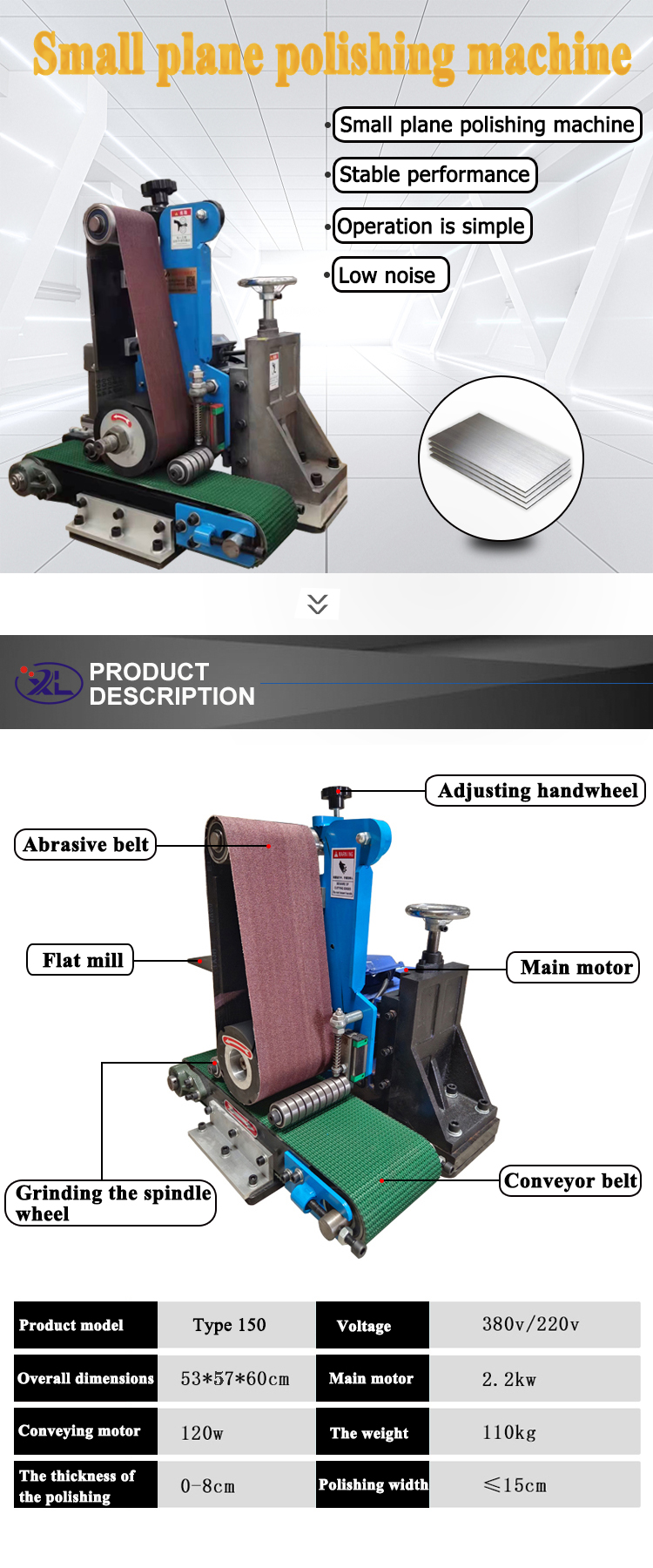
Choosing the right coolant for centerless grinding is not just about functionality but also about compatibility with the materials being processed. Some coolants are formulated with specific additives designed to work effectively with certain metals or composites. Manufacturers must select a coolant that aligns with their machining materials to maximize performance and minimize potential adverse reactions that could degrade the quality of both the coolant and the workpiece.
In addition to performance characteristics, the safety and environmental impact of grinding coolants cannot be overlooked. Many traditional coolants may contain harmful substances, posing risks to operators and the environment. Consequently, industries are increasingly turning to biodegradable and non-toxic coolants that provide the same level of performance without the associated health and environmental hazards. These eco-friendly options not only adhere to regulations but also promote a safer workspace, a crucial consideration in modern manufacturing.
Furthermore, the maintenance of coolant systems is integral to their effectiveness. Regular monitoring of coolant concentration, pH level, and contamination is essential to ensure that the coolant performs at its best. Operators must implement good housekeeping practices and utilize filtration systems to maintain cleanliness and effectiveness. A proactive approach to coolant maintenance can prevent costly downtime and ensure consistent production quality.
In conclusion, the role of high-quality coolant in centerless grinding is fundamental to enhancing machining efficiency and product quality. It provides lubrication, regulates temperature, aids in chip removal, and ensures compatibility with various materials. With an increasing focus on health, safety, and environmental considerations, manufacturers are encouraged to invest in advanced coolant solutions that not only meet operational requirements but also contribute to a sustainable production environment. Ultimately, the success of centerless grinding operations heavily relies on the selection and maintenance of the right coolant, underscoring its significance in modern manufacturing processes.