The Importance of Centerless Tube Polishing Machines in Modern Manufacturing
In the realm of metal processing and fabrication, the efficiency and quality of surface finishing play crucial roles in determining the overall product performance. One of the key players in this field is the odm centerless tube polishing machine. This advanced equipment has revolutionized the way manufacturers approach tube polishing, delivering exceptional results for a variety of industries, including automotive, aerospace, and medical.
Understanding Centerless Polishing
Centerless polishing is a unique process that differs from traditional polishing methods. It involves the use of a machine that allows for the continuous polishing of tubes without the need for fixtures or supports. This method is particularly beneficial for long and slender tubes, enabling a smooth and uniform finish along the entire length of the material. The centerless tube polishing machine achieves this by positioning the tube between two wheels a driving wheel and a regulating wheel. This setup ensures that the tube is held securely in place while being polished, resulting in consistent and high-quality finishes.
Key Features of ODM Centerless Tube Polishing Machines
The odm centerless tube polishing machine is designed with several key features that enhance its performance and usability
1. Versatility These machines can handle a wide range of tube diameters and materials, making them suitable for various applications. Whether dealing with stainless steel, aluminum, or other metals, the centerless system adapts to different tube specifications.
2. Automated Processes Many modern centerless polishing machines come equipped with automation features, which reduce the need for manual intervention and increase productivity. Automation not only speeds up the polishing process but also minimizes human errors, leading to a higher level of precision.
3. Consistent Surface Quality The design of centerless polishing machines ensures that every tube receives the same level of treatment throughout the entire polishing cycle. This consistency is crucial for industries where precision is non-negotiable, such as in the production of medical devices or aerospace components.
odm centerless tube polishing machine
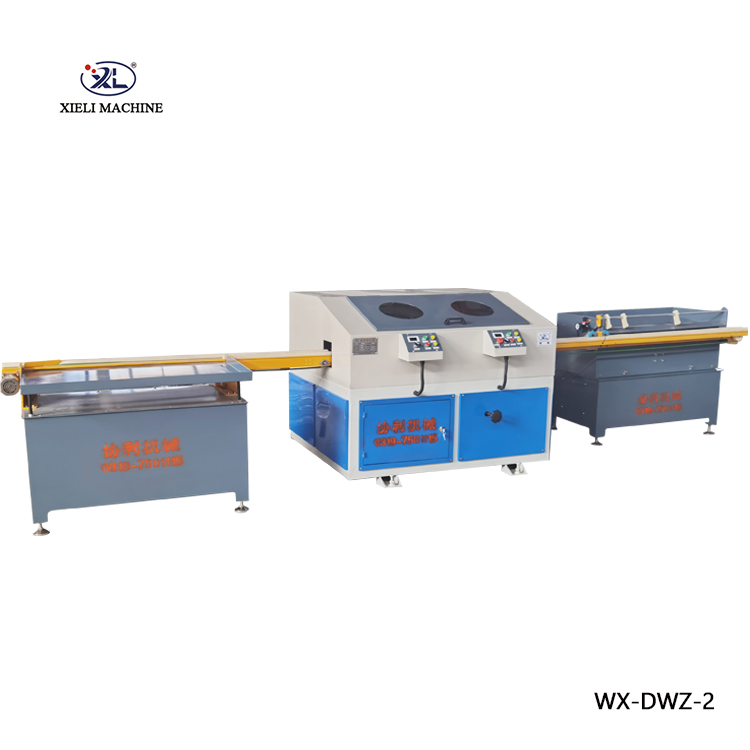
4. Efficiency Centerless polishing machines are known for their efficiency. They can polish multiple tubes simultaneously or handle long batches without interruption. This capability significantly reduces lead times in production, allowing companies to respond quickly to market demands.
5. Ergonomics and Safety Modern machines are designed with the operator's safety and comfort in mind. Features such as adjustable work heights, safety enclosures, and noise reduction systems help create a safer and more pleasant working environment.
Applications in Various Industries
The application of ODM centerless tube polishing machines is vast. In the automotive industry, these machines are employed to polish exhaust systems, fuel lines, and various other components that require high-quality surface finishes. The polished surfaces improve not only aesthetic appeal but also resistance to corrosion and wear.
In the aerospace sector, where materials must meet stringent regulations, centerless tube polishing machines ensure that components are free of defects that could compromise safety. The smooth finishes reduce drag in fluid systems, optimizing performance and efficiency.
The medical industry also benefits greatly from these polishing machines, particularly in the manufacturing of surgical instruments and medical tubes. A precise finish is essential to meet hygiene standards and ensure the safety of patients.
Conclusion
In conclusion, the ODM centerless tube polishing machine stands as a testament to modern manufacturing technology's advancement. Its unique approach to polishing, combined with automation and efficiency, places it at the forefront of surface finishing solutions. As industries continue to demand higher standards of quality and performance, the role of centerless tube polishing machines will undoubtedly become even more pivotal. Investing in such equipment not only enhances production capabilities but also helps manufacturers maintain a competitive edge in a rapidly evolving market.