The Evolution and Importance of Custom Centerless Grinders
In the world of manufacturing and precision engineering, centerless grinders play a crucial role in producing high-quality cylindrical components. Among various types of grinding machines, the custom centerless grinder stands out for its adaptability and efficiency. In this article, we will explore the significance, workings, and advancements of custom centerless grinders, which cater to the unique needs of different industries.
Understanding Centerless Grinding
At its core, centerless grinding is a technique that allows for the efficient processing of cylindrical parts without the need for a conventional center to hold the workpiece in place. This method employs two wheels the grinding wheel, which shapes the material, and the regulating wheel, which controls the rotation and feed rate of the workpiece. The workpiece is fed into the grinding area and is supported by a blade on one side, allowing for continuous operation and high throughput.
This adaptability makes centerless grinding ideal for producing components with strict tolerances and surface finish requirements, essential in industries like automotive, aerospace, and medical manufacturing.
The Need for Customization
As industries evolve and technology advances, the demand for customization in manufacturing processes has surged. Companies today require specific grinding solutions to meet unique challenges in their production lines. This is where custom centerless grinders come into play.
Custom centerless grinders are tailored to meet the precise specifications of the workpieces they are designed to process. They can be equipped with specialized features that accommodate varying part sizes, shapes, and materials. For example, an automotive manufacturer might need a grinding machine capable of processing both small and large parts efficiently, while a medical device manufacturer might require stringent cleanliness standards in their processes.
The Design and Engineering Process
Designing a custom centerless grinder involves a thorough understanding of the customer's requirements and the intricate details of the grinding process
. The engineering team typically collaborates closely with clients to identify the necessary features and capabilities, including1. Size and Configuration Custom grinders can be designed to fit specific floor plans and operational needs. This may include modifications to the length and width of the machine or alterations to the wheel setup.
custom 3 centerless grinder
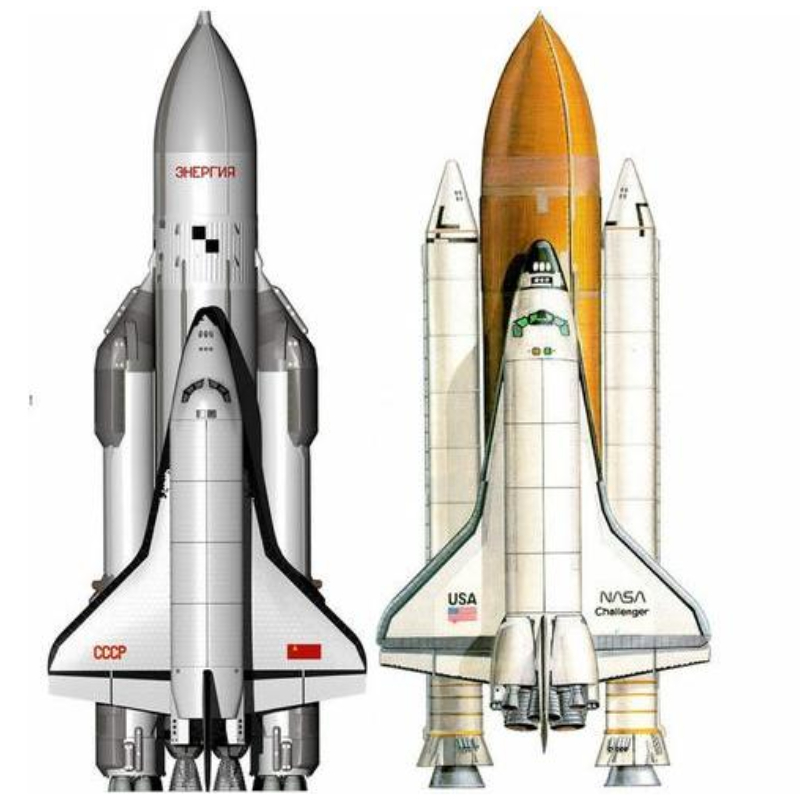
2. Material Handling Automated loading and unloading systems can be integrated to streamline production and reduce manual intervention. This is crucial for high-volume operations where consistency and efficiency are key.
3. Control Systems Modern centerless grinders incorporate advanced control systems that allow for precise adjustments in speed, feed rate, and pressure. These controls ensure optimal performance and maintain high levels of accuracy and repeatability.
4. Cooling and Lubrication To prevent overheating and maintain quality, custom grinders can include specialized cooling and lubrication systems. This is particularly important when grinding hard materials that generate significant heat during processing.
5. Safety Features Enhancing operator safety is paramount in any industrial setting. Custom grinders often incorporate safety features such as emergency stops, protective enclosures, and advanced monitoring systems to minimize risks associated with grinding operations.
Advancements in Technology
The machining world is witnessing remarkable advancements in technology, and centerless grinding is no exception. The integration of robotics, AI, and IoT (Internet of Things) into custom centerless grinders has opened new avenues for enhancing productivity and quality. For instance
- Automated Inspection Many custom grinders now feature in-process measurement systems that provide real-time feedback, allowing for immediate adjustments to maintain specifications. - Data Analytics Collecting data during the grinding process helps manufacturers analyze performance and implement predictive maintenance, reducing downtime and improving overall efficiency.
- Energy Efficiency Modern custom centerless grinders are designed with energy efficiency in mind, utilizing components and systems that minimize energy consumption while maximizing output.
Conclusion
In conclusion, custom centerless grinders represent a vital aspect of modern manufacturing, meeting the diverse and evolving needs of various industries. By providing tailored solutions that enhance precision, efficiency, and safety, these grinding machines contribute significantly to the production of high-quality parts essential for today’s advanced applications. As technology continues to progress, we can expect further innovations in custom centerless grinding, ultimately shaping the future of manufacturing processes worldwide.