The Advantages of OEM CNC Centerless Grinding Machines
In the modern manufacturing landscape, precision and efficiency are paramount. One of the most effective methods for achieving precise dimensions and finishes on round workpieces is through centerless grinding. The advent of OEM (Original Equipment Manufacturer) CNC (Computer Numerical Control) centerless grinding machines has revolutionized this process, offering improved reliability, accuracy, and efficiency.
Understanding Centerless Grinding
Centerless grinding is a technique used for shaping the outer surface of an object. Unlike traditional grinding, this method does not require the workpiece to be clamped in place. Instead, the workpiece is supported by two wheels – the grinding wheel and the regulating wheel – allowing for continuous operation. This unique setup provides significant advantages in terms of processing speed and efficiency, making it an ideal choice for high-volume production settings.
The Role of CNC Technology
The integration of CNC technology into centerless grinding machines enhances their capabilities. CNC systems automate the grinding process, allowing for programmable specifications and adjustments. This not only increases the precision of the grinding operation but also reduces the potential for human error. Operators can set parameters for multiple processes, managing various aspects of grinding, including feed rate, speed, and duration, with minimal hands-on intervention.
Advantages of OEM Machines
Opting for OEM CNC centerless grinding machines brings several benefits to manufacturers
1. Quality Assurance OEM machines are designed and built by trusted manufacturers who prioritize quality and performance. This ensures that the machines meet high standards and are reliable in their operation, thereby maintaining production quality.
oem cnc centerless grinding machine
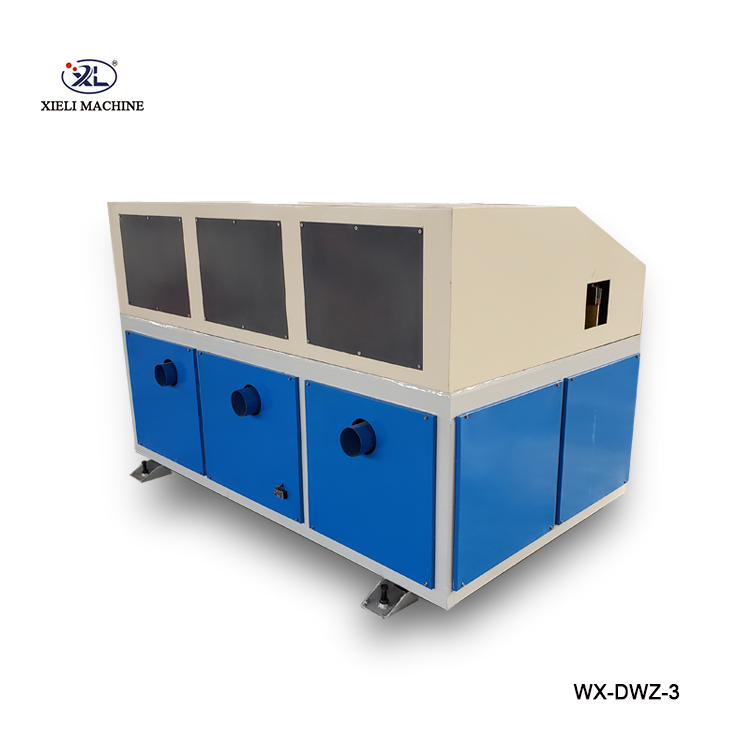
2. Customization OEM manufacturers often offer customization options, allowing businesses to tailor machines to their specific needs. This adaptability is crucial in industries that require distinct specifications, such as aerospace and automotive.
3. Advanced Technology OEM providers typically incorporate the latest technology in their machines. This includes advanced sensors, state-of-the-art software, and enhanced grinding capabilities, resulting in improved precision and reduced cycle times.
4. Service and Support Purchasing from an OEM means that customers receive comprehensive support and service. OEM manufacturers usually provide training, maintenance, and parts supply, ensuring that machines remain operational and efficient over time.
5. Cost-effectiveness While initial costs may be higher for OEM machines, the long-term savings associated with their reliability, efficiency, and reduced downtime often offset the initial investment. This results in overall improved profitability for manufacturing operations.
Application in Various Industries
OEM CNC centerless grinding machines find applications across different sectors, including metalworking, manufacturing of automotive components, medical device fabrication, and more. Their ability to produce consistent, high-quality parts makes them invaluable in maintaining the stringent tolerances required in these industries.
Conclusion
As manufacturers seek to enhance their production processes, the role of OEM CNC centerless grinding machines cannot be overstated. With their precision, reliability, and ability to accommodate custom requirements, these machines not only contribute to improved efficiency but also bolster product quality. Investing in such technology is essential for businesses looking to stay competitive in today’s fast-paced manufacturing environment. Embracing the advancements in CNC centerless grinding will undoubtedly lead to greater operational success and superior output.