Custom Filmatic Solutions for Centerless Grinder Machines
In the world of manufacturing, precision and efficiency are paramount. Among the various machinery that plays a critical role in achieving these standards, centerless grinders stand out for their ability to perform high-precision grinding on a wide range of materials. As industries continue to evolve, the demand for tailored solutions becomes increasingly evident. This is where custom filmatic solutions for centerless grinder machines come into play.
Understanding Centerless Grinding
Centerless grinding is a process that enables the grinding of workpieces without the need for a fixture, which is often considered a significant advantage over traditional grinding methods. The process relies on two wheels – the grinding wheel and a regulating wheel – which work together to hold the workpiece in place while it is ground to the desired specification. This technique is favored for high-volume production due to its speed, efficiency, and ability to produce parts with tight tolerances.
The Role of Filmatic Solutions
Filmatic solutions provide an innovative approach to enhance the functionality and performance of centerless grinder machines. These solutions involve the use of tailored films or coatings applied to various components of the grinder. The primary goal of these films is to reduce friction, increase durability, and improve the overall efficiency of the grinding process.
Custom filmatic solutions can be designed to suit specific operational environments and material types, which can significantly improve the wear resistance of vital components, thus extending the machine's lifespan
. Moreover, these films can also optimize the grinding efficiency by ensuring that the materials are processed smoothly and consistently.Benefits of Customization
custom filmatic for centerless grinder machine
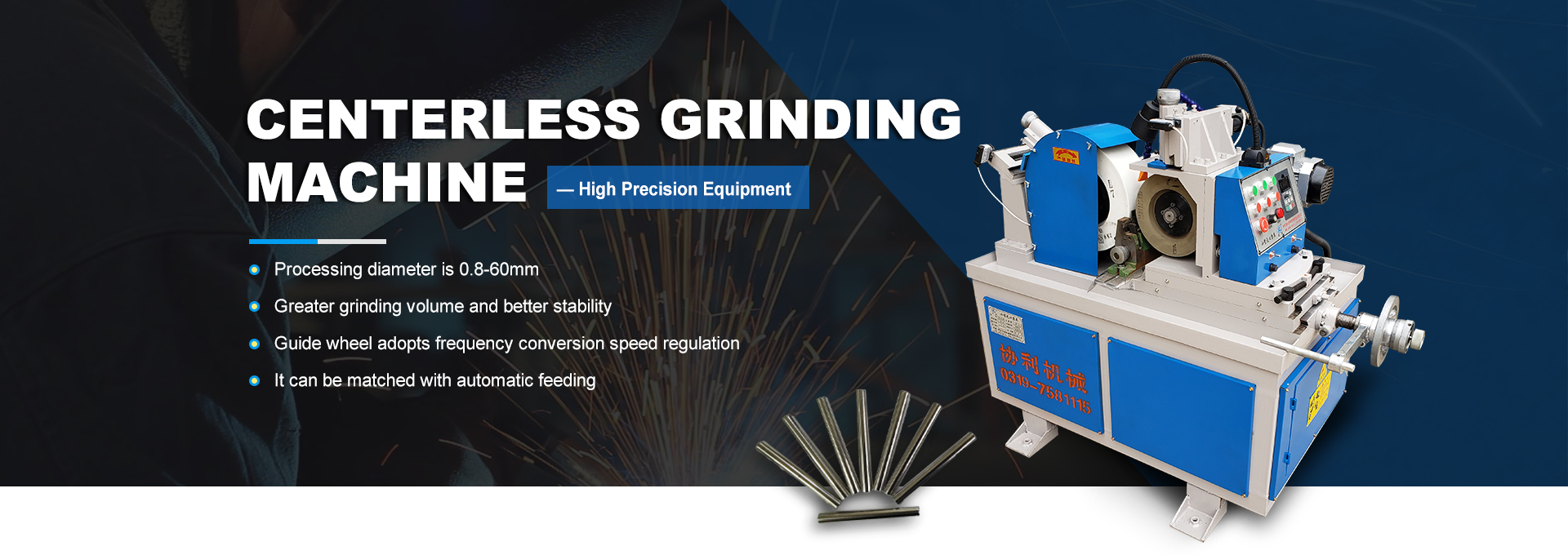
One of the main advantages of custom filmatic applications is that they can be engineered to meet the exact specifications and requirements of a particular machining operation. This level of customization allows manufacturers to address specific challenges they may face during the grinding process. For example, different materials may require different types of films depending on their hardness, abrasive properties, and the intended finish.
By working closely with manufacturers to design bespoke filmatic solutions, suppliers can help to reduce downtime, improve productivity, and increase overall efficiency. Custom coatings can also minimize the buildup of heat during grinding, thus reducing the likelihood of thermal damage to both the grinder and the workpiece being processed.
Environmental Considerations
In today’s manufacturing landscape, sustainability is a key focus. Custom filmatic solutions can also contribute to a greener production process. Many modern films are designed to be environmentally friendly, using less harmful materials and reducing waste. By implementing these solutions, manufacturers can improve their operational efficiency while also adhering to environmental regulations and corporate social responsibility initiatives.
Conclusion
The intersection of technology and customization in the machine tool sector heralds a new era of precision manufacturing. Custom filmatic solutions for centerless grinder machines exemplify this trend, offering tailored enhancements that not only boost performance but also ensure longevity. As companies continue to strive for operational excellence, integrating advanced filmatic technologies will be pivotal in maintaining competitiveness in the ever-evolving manufacturing landscape.
In an age where every detail counts, embracing custom solutions can lead to significant improvements in productivity, quality, and sustainability. As the industry charts its course into the future, those who invest in technological advancements and customizations will likely emerge as leaders in the manufacturing realm.