Understanding Infeed Centerless Grinders
Infeed centerless grinders are pivotal in the manufacturing realm, particularly for producing precise and consistent cylindrical parts. Unlike traditional grinding methods, centerless grinding offers unique advantages that enhance efficiency and accuracy in the machining process. This article delves into the mechanisms, benefits, and applications of infeed centerless grinders, providing insight into their essential role in modern manufacturing.
At its core, an infeed centerless grinder utilizes two rotating wheels—a grinding wheel and a regulating wheel. The grinding wheel, which is larger, is responsible for removing material from the workpiece, while the smaller regulating wheel controls the speed and position of the part during the grinding process. The workpiece is positioned between these two wheels and is fed in a lateral manner, allowing for a quick and efficient grinding operation without the need for a conventional chuck or fixture.
One of the most significant advantages of infeed centerless grinding is its ability to handle complex geometries and irregularly shaped parts. By adjusting the angles and pressures applied by the wheels, operators can produce pieces with tight tolerances and sophisticated shapes that may be challenging to achieve through traditional grinding methods. This flexibility makes infeed centerless grinders particularly valuable for industries that require high precision, such as aerospace, automotive, and medical device manufacturing.
infeed centerless grinder
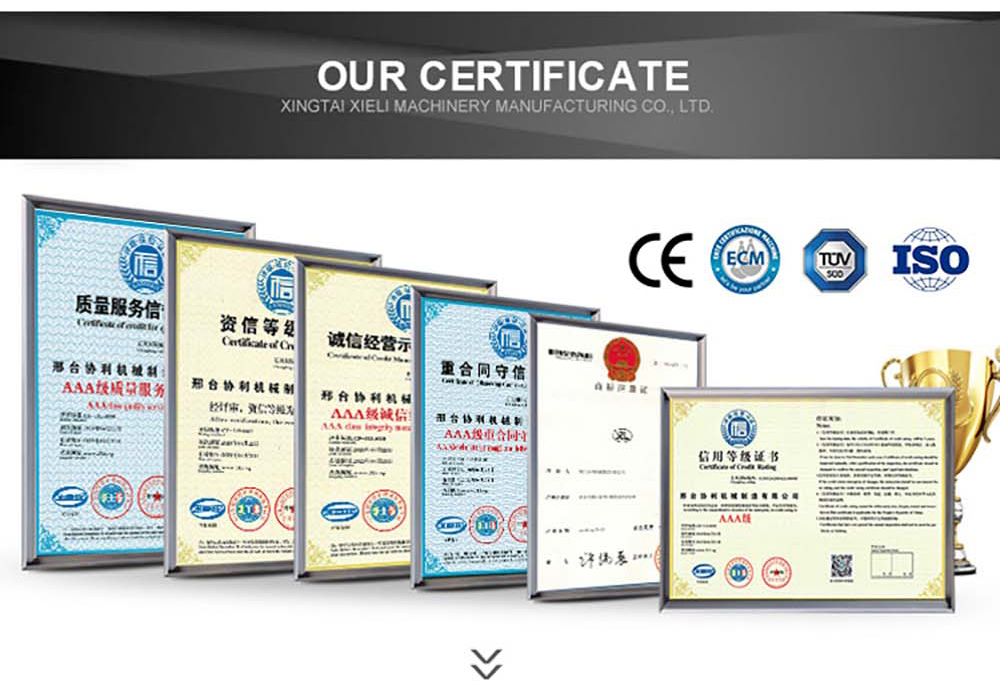
Another critical benefit of infeed centerless grinders is their operational efficiency. The design allows for continuous loading of workpieces, thereby minimizing downtime between grinding sessions. Unlike other grinding techniques that may require frequent adjustments and pauses, centerless grinders can operate at higher speeds and with greater throughput, leading to reduced production times and increased output.
Moreover, the uniformity achieved through centerless grinding enhances the overall quality of the final product. The process generates minimal waste and produces less heat, which reduces the risk of warping or damaging sensitive materials. Additionally, the consistency in dimensions and surface finishes contributes significantly to lower reject rates and improved cost-effectiveness in long-term production schedules.
In practical applications, infeed centerless grinders are used to manufacture essential components such as shafts, pins, and bushings. These components are utilized in various end products, from engines to hydraulic systems. Manufacturers choose centerless grinding for its ability to deliver precision and reliability, ensuring that the parts not only meet but often exceed industry standards.
In conclusion, infeed centerless grinders are an indispensable tool in the machining industry. They provide a powerful solution for producing high-quality, precise parts with minimal waste and maximum efficiency. As industries continue to evolve and demand higher standards of precision, the importance of technologies like centerless grinding will only increase, underscoring its relevance in the future of manufacturing. Whether for large-scale production or specialized components, infeed centerless grinders remain at the forefront of innovation and efficiency in machining technology.