The Importance of Centerless Valve Grinders in Precision Engineering
In the world of precision engineering, the significance of high-quality machinery cannot be overstated. Among the array of tools available, centerless valve grinders stand out as essential equipment for maintaining and enhancing the performance of valve components in various industries, from automotive to aerospace. These machines provide exceptional accuracy and efficiency, addressing the specific needs of valve processing with remarkable precision.
Understanding Centerless Grinding
Centerless grinding is a machining process that uses abrasive cutting to remove material from a workpiece. Unlike traditional grinding, where the workpiece is mounted between two centers, centerless grinding holds the workpiece in place through the use of a grinding wheel and a regulating wheel. This process allows for the continuous feed of parts, resulting in consistent results and high productivity.
In the case of valve grinding, centerless grinding machines are engineered to provide superior finishing on valve stems, ensuring they meet the stringent tolerances required for optimal performance. The ability to grind an array of shapes and sizes makes centerless valve grinders a versatile tool for manufacturers.
Applications of Centerless Valve Grinders
Centerless valve grinders are used across various applications, reflecting the versatility and importance of these machines in modern industry.
1. Automotive Industry Valves are integral components in automotive engines, controlling the flow of gases and ensuring efficiency. Centerless grinding helps achieve precise dimensions on valve stems and bodies, resulting in better functionality and engine performance.
2. Aerospace Engineering Aerospace components require meticulous attention to detail due to high safety standards. Centerless valve grinders play a crucial role in producing ultra-precise valve components that can withstand the extreme conditions faced during flight.
3. Manufacturing From heavy machinery to medical devices, valves are ubiquitous in manufacturing processes. The efficiency of centerless grinding allows for mass production of quality parts, reducing costs while maintaining high standards.
4. Marine Engineering In marine applications, valves must be durable and resistant to corrosion. Centerless valve grinders can produce parts that meet the rigorous requirements of marine environments, including saline conditions.
Key Features of Centerless Valve Grinders
Centerless valve grinders come equipped with several features that enhance their functionality
centerless valve grinder products
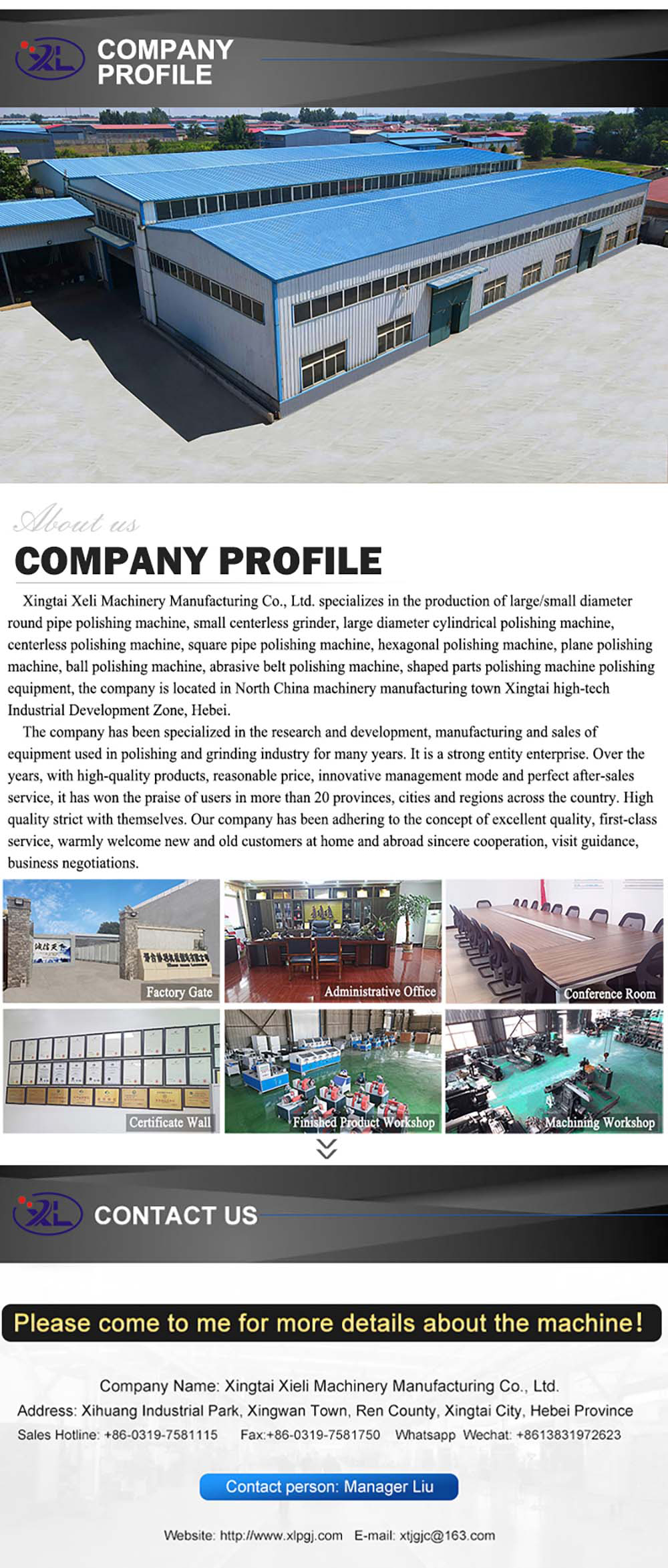
- Automatic Feeding Systems These systems allow operators to set up production runs without constant supervision, maximizing productivity.
- Precision Grinding Wheels Centerless valve grinders use specially designed grinding wheels that ensure an even material removal rate, resulting in a smooth finish.
- Adjustable Settings Operating parameters such as speed, feed rate, and pressure can be adjusted depending on the specific requirements of the workpiece, showcasing the machine's versatility.
- Automation Integration Many modern centerless grinders are equipped with robotics and automation systems to streamline the grinding process, improving efficiency and reducing labor costs.
Benefits of Using Centerless Valve Grinders
The use of centerless valve grinders translates to numerous benefits that appeal to manufacturers seeking quality and efficiency in their production processes.
- Enhanced Precision By eliminating part rotation during grinding, the process achieves exceptional accuracy and consistency.
- Reduced Cycle Times Centerless grinding allows for continuous operation, reducing the time required per part and increasing overall throughput.
- Lower Cost of Ownership While the initial investment in centerless grinding technology may be higher, the cost savings realized through increased efficiency, reduced scrap rates, and minimal downtime are significant.
- Quality Assurance The repeatability achieved with centerless grinding ensures that each valve produced meets the established specifications, reducing the need for secondary processing.
Conclusion
In conclusion, centerless valve grinders are indispensable in the landscape of precision engineering. Their ability to deliver high precision, efficiency, and versatility makes them a preferred choice for manufacturers across multiple sectors. As industries evolve and demands for smaller, lighter, and more efficient components increase, the relevance of centerless valve grinders will only grow, solidifying their place as fundamental tools in the production of high-quality valve components. Investing in advanced grinding technology is not just a choice but a necessity for manufacturers aiming to stay competitive and meet the rigorous demands of the modern market.