Custom Automatic Pipe Polishing Machines Revolutionizing Metal Finishing
In the industrial manufacturing landscape, the demand for precision and efficiency has never been higher. As various industries rely heavily on high-quality metal components, the process of pipe polishing has emerged as a crucial step in ensuring product durability and aesthetic appeal. Enter the custom automatic pipe polishing machine – a technological marvel poised to transform the metal finishing sector.
The Need for Pipe Polishing
Metal pipes are widely used across different applications, including construction, automotive, plumbing, and manufacturing. However, the raw finish of these pipes is often rough and unattractive, leading to potential issues such as corrosion, tarnishing, and improper fitting. Pipe polishing serves to remove surface imperfections, provide a smooth finish, and enhance corrosion resistance, thereby contributing to an extended lifespan.
The Evolution of Polishing Technology
Traditional pipe polishing methods were labor-intensive and often inconsistent in quality. Manual polishing required significant human input and was prone to variability due to the skill level of the technicians. This inconsistency could lead to high levels of scrap material and additional costs. With the introduction of automation, the industry has experienced a paradigm shift. Automated polishing machines can operate continuously, providing uniform results while minimizing human error.
Custom Solutions for Diverse Needs
A key advantage of modern pipe polishing machines is their customization. Manufacturers understand that different applications require different polishing standards, and off-the-shelf solutions may not fit every requirement. Custom automatic pipe polishing machines can be tailored to accommodate varying pipe sizes, shapes, and materials. Whether dealing with stainless steel, aluminum, or other alloys, a custom solution ensures that the specific polishing needs are met with precision.
Features of Custom Automatic Pipe Polishing Machines
1. Automation Advanced control systems allow for the automation of the entire polishing process, reducing labor costs and increasing efficiency.
custom automatic pipe polishing machine
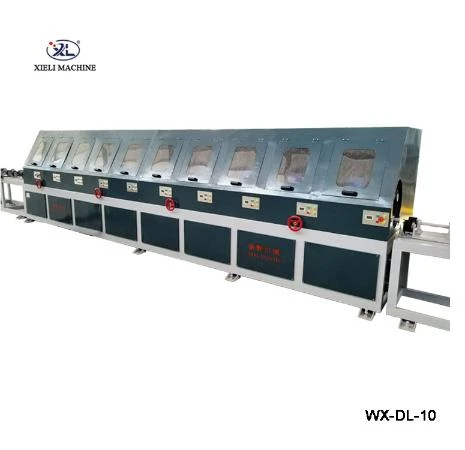
3. Adaptable Processing Speeds Users can adjust the speed of the polishing cycle based on the material and desired finish, ensuring optimal results without damaging the pipe.
4. Integration with Other Processes Custom machines can often be integrated with other manufacturing processes, such as cutting or bending, providing a seamless workflow that increases productivity.
5. User-friendly Interfaces Modern machines come equipped with intuitive controls and monitoring systems, allowing operators to easily adjust settings and track the polishing process in real-time.
Economic Benefits
Investing in custom automatic pipe polishing machines can yield significant economic benefits. By reducing labor costs and increasing processing speed, manufacturers can improve their bottom line. The consistent quality of polished pipes also leads to lower rejection rates and reduced material waste, enhancing overall profitability.
Meeting Industry Standards
With growing environmental and safety regulations, companies are compelled to adopt practices that meet stringent standards. Custom automatic polishing systems can be designed to minimize waste and emissions, aligning with eco-friendly goals while maintaining compliance with industry regulations.
Conclusion
As industries continue to evolve, the need for high-quality metal finishing becomes increasingly critical. Custom automatic pipe polishing machines present a compelling solution to meet these demands, offering the benefits of efficiency, customization, and quality. By investing in these advanced technologies, manufacturers can enhance their operational capabilities, reduce costs, and remain competitive in a global market.
Embracing this transformative technology is not merely an option but a necessary step towards achieving excellence in metal finishing, thus paving the way for a more efficient and sustainable future in manufacturing.