Understanding Centerless Grinders The 3% Advantage
In the realm of precision machining, centerless grinders hold a crucial position in enhancing productivity and ensuring accuracy in the manufacturing process. These sophisticated machines are designed to grind the outer diameter of cylindrical parts without the need for a central support, offering unique benefits that set them apart from conventional grinding equipment. Among the various types of centerless grinders available, the ones that adhere to the 3% efficiency improvement standard have attracted significant attention due to their ability to enhance operational effectiveness while maintaining high levels of precision.
What is a Centerless Grinder?
A centerless grinder operates on the principle of supporting the workpiece between two wheels, a grinding wheel and a regulating wheel, which work together to achieve the desired shape and finish. The workpiece rotates as it is fed through the machine, guided by the regulating wheel while being ground by the grinding wheel. The lack of a central support allows for continuous operation, making centerless grinding an ideal choice for high-volume production of cylindrical components.
The 3% Efficiency Improvement
When we talk about the 3% centerless grinder products, we refer to machines that have been engineered to enhance their efficiency by at least 3% compared to their predecessors. This improvement can be attributed to several key factors
1. Optimized Design Modern centerless grinders are designed with advanced engineering principles that maximize stability and minimize vibrations. This results in a smoother operation and greater consistency in the grind, leading to better surface finishes and dimensional accuracy.
2. Enhanced Materials Technological advancements in material science have allowed manufacturers to produce grinding wheels and components that are more durable and efficient. These materials can withstand higher loads and temperatures, resulting in less wear and tear and reduced downtime for maintenance.
3 centerless grinder products
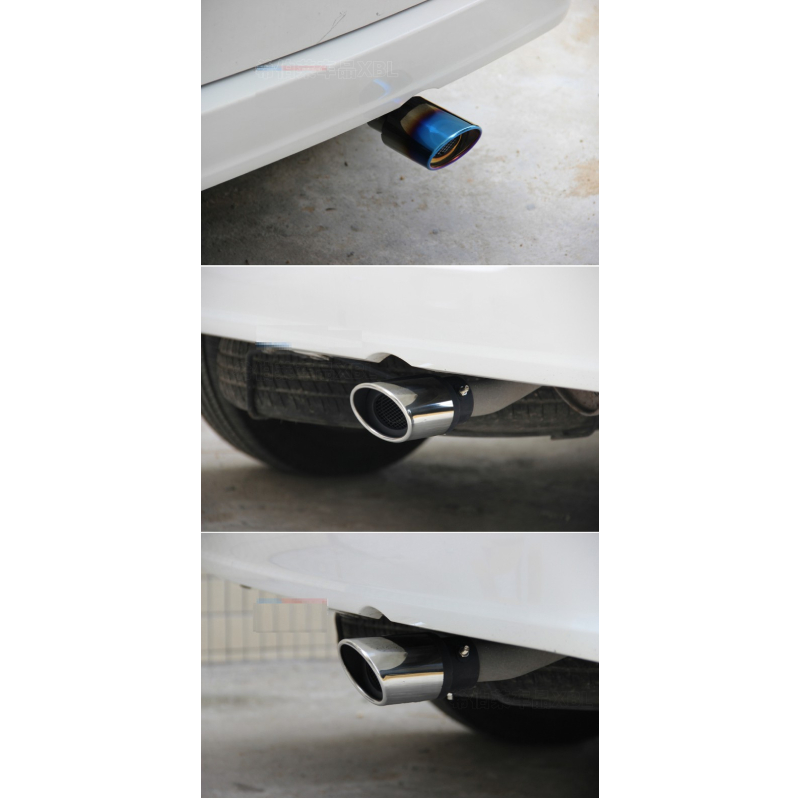
3. Automated Precision Many of the latest centerless grinders come equipped with automated features such as programmable settings and real-time monitoring systems. These innovations allow operators to maintain consistent quality levels and significantly reduce the likelihood of human error.
Applications of Centerless Grinders
The versatility of centerless grinders makes them suitable for a wide range of applications across various industries. They are commonly used in the production of shafts, rods, and tubes, which are essential components in automobiles, aerospace, and medical devices. The ability to grind parts to tight tolerances is critical in these fields, where precision is non-negotiable.
Moreover, centerless grinding is instrumental in the manufacturing of parts that require a high volume of output without sacrificing quality. The efficient feed rates and quick set-up times inherent in centerless grinding processes can lead to substantial productivity gains, which aligns perfectly with the manufacturing sector’s push towards lean production practices.
Sustainable Practices
In addition to enhancing efficiency, modern centerless grinders are also being designed with sustainability in mind. Energy-efficient motors and the use of environmentally friendly coolant systems are becoming standard features, addressing the growing concern over the environmental impact of manufacturing processes. By investing in 3% centerless grinder products, companies not only improve their operational efficiency but also contribute to more sustainable manufacturing practices.
Conclusion
The evolution of centerless grinders, particularly the introduction of models that showcase a 3% efficiency improvement, is a testament to the ongoing innovation within the manufacturing industry. These machines not only enhance productivity and precision but also pave the way for more sustainable practices. As manufacturers continue to seek competitive advantages, investment in advanced centerless grinding technology will be crucial to achieving operational excellence and meeting the rigorous demands of modern industry. For businesses poised to stay ahead in their fields, embracing the potential of centerless grinders is not just an option; it is a strategic necessity.