Revolutionizing Metal Finishing The Role of Tube Internal Polishing Machine Factories
In the ever-evolving landscape of manufacturing, the demand for precision and quality has propelled various technologies to the forefront. Among these innovations, tube internal polishing machines have emerged as crucial players, particularly in sectors requiring high standards of surface finish and hygiene. Factories specializing in the production of these machines are redefining the standards for metal finishing processes, driving efficiency and enhancing product quality across industries.
One of the primary functions of tube internal polishing machines is to ensure that the internal surfaces of tubes—often made of stainless steel or other alloys—achieve a smooth and reflective finish. This is particularly important in industries such as food and beverage, pharmaceuticals, and aerospace, where even the slightest surface imperfections can lead to contamination, performance issues, or structural failures. The polishing process not only enhances aesthetic appeal but also plays a critical role in preventing corrosion, thereby extending the lifespan of metal products.
The manufacturing process of these polishing machines involves advanced engineering and innovative technologies. Factories producing tube internal polishing machines invest heavily in research and development to integrate state-of-the-art features into their equipment. For instance, many modern machines employ automated polishing techniques that utilize abrasive media or chemical solutions tailored for specific materials. This level of automation reduces labor costs and minimizes human error, ensuring consistent quality across all produced tubes.
Moreover, the diversity of applications for tube internal polishing machines has led to a range of models and specifications that cater to different industries. From small-scale, portable machines designed for on-site polishing to large, industrial systems capable of handling extensive production runs, the variety in design ensures that clients can find a solution that perfectly fits their operational needs. Factories often collaborate closely with their clients to customize machinery based on specific requirements, further enhancing the value they provide.
tube internal polishing machine factory
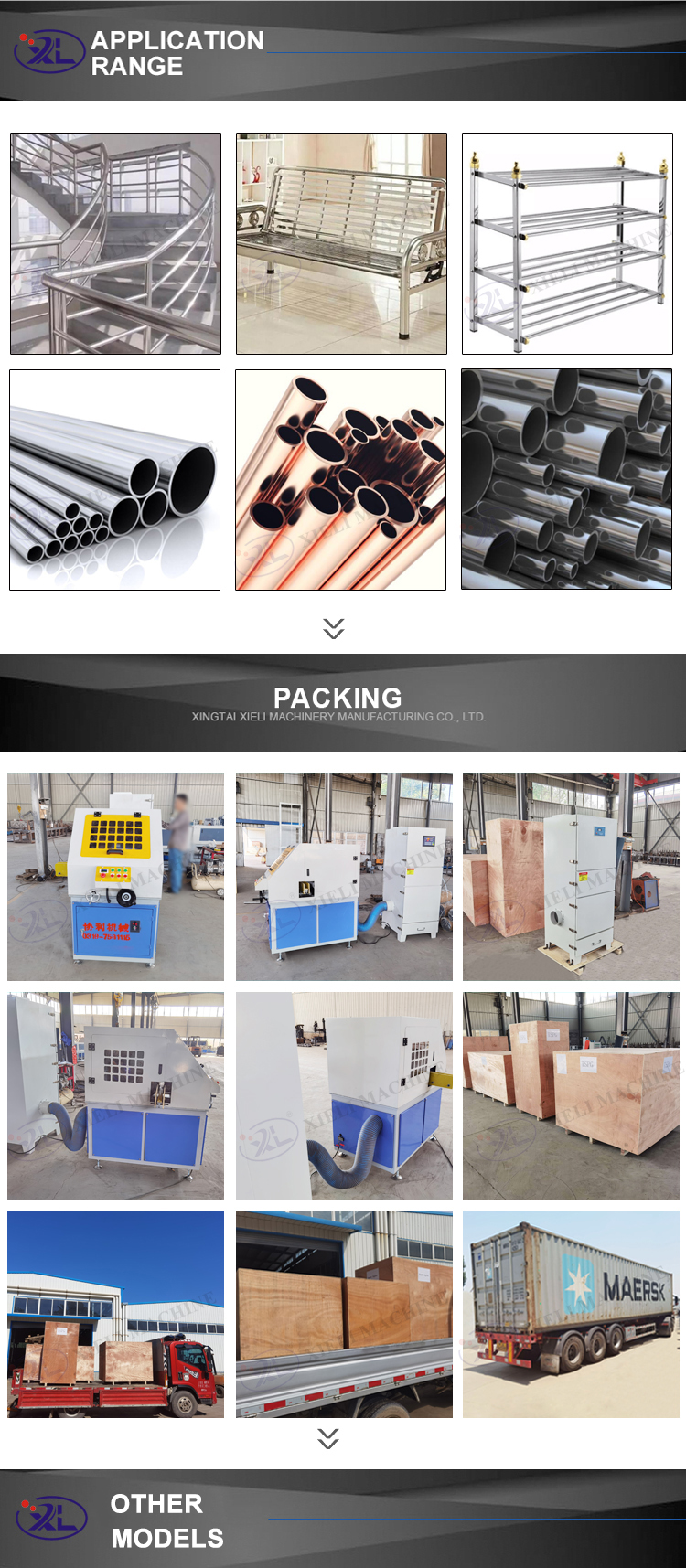
Sustainability is another growing concern in the manufacturing sector, and tube internal polishing machine factories are no exception. As industries move towards greener practices, manufacturers are focusing on producing machines that operate with minimal waste and energy consumption. Some machines are designed to recycle polishing media, while others employ environmentally friendly chemicals that reduce the ecological impact of traditional polishing processes. By adopting sustainable practices, these factories not only comply with regulations but also attract customers who prioritize environmentally responsible suppliers.
Quality assurance is paramount in industries that depend on tube internal polishing. To address this, many factories implement rigorous testing and inspection protocols to ensure that each machine meets international standards. Certifications such as ISO and CE lend credibility to these manufacturers, assuring clients of the reliability and effectiveness of their products. Additionally, after-sales support, including maintenance and training, further enhances customer satisfaction and loyalty.
As the global economy continues to grow, the importance of efficient and high-quality manufacturing processes cannot be overstated. Tube internal polishing machine factories are at the forefront of this transformation, equipped with advanced technology and a commitment to innovation. Their contributions help businesses improve product quality, reduce costs, and adhere to stringent safety and hygiene standards.
Looking ahead, the future appears bright for tube internal polishing machine factories. With the ongoing advancements in automation and materials science, we can expect to see even more sophisticated machines that enhance performance while reducing operational complexities. As industries grow increasingly competitive, the role of these specialized manufacturers will become even more critical, ensuring that high standards are met consistently and efficiently.
In conclusion, tube internal polishing machine factories play a vital role in enhancing the quality and reliability of metal products across various industries. Through innovation, customization, and a commitment to sustainability, these manufacturers are shaping the future of metal finishing. As technology continues to evolve, their impact will only become more significant, paving the way for a new era of precision engineering.