Understanding ODM Abbreviation in Centerless Grinding
In the world of manufacturing and precision machining, terms and abbreviations play a pivotal role in enhancing communication and understanding among professionals. One such abbreviation that often arises in discussions about centerless grinding is ODM. Understanding this term, particularly in its application to centerless grinders, can provide valuable insights into manufacturing processes and operational efficiency.
What is Centerless Grinding?
Centerless grinding is a machining process that removes material from a workpiece to achieve a high degree of precision in dimensions and surface finish. Unlike traditional grinding methods, where the workpiece is held between two centers, centerless grinding employs a different setup. Here, the workpiece is supported by a blade and rotated by a grinding wheel that surrounds it, allowing for continuous and efficient processing.
Defining ODM
ODM stands for Original Design Manufacturer. In the context of centerless grinding, an ODM is a company that designs products to be manufactured by another company. The ODM not only provides the design specifications but may also oversee the production process, ensuring that the end products meet the established quality standards and specifications. This model is particularly beneficial in industries where precision and customization are paramount, such as automotive, aerospace, and medical device manufacturing.
Importance of ODM in Centerless Grinding
The role of an ODM in centerless grinding is significant for several reasons
odm abbr for centerless grinder
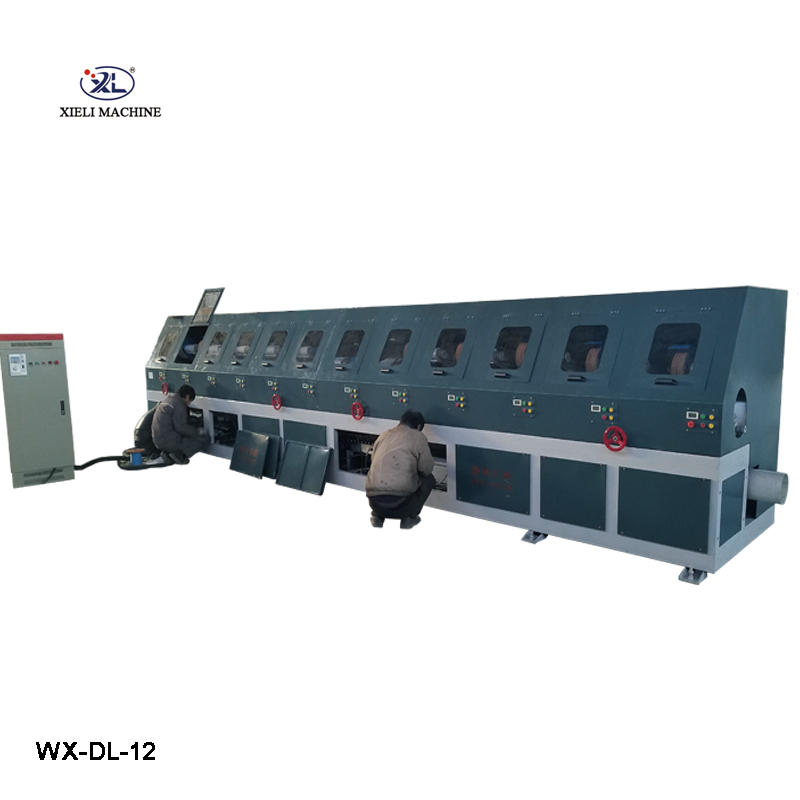
1. Customization ODMs can offer tailor-made solutions to meet specific requirements, adjusting designs based on unique customer needs. This flexibility is crucial in industries that require precise dimensions and finishes.
2. Expertise An ODM typically possesses extensive knowledge and experience in the design and manufacturing processes. This expertise ensures that the centerless grinding operations are optimized for efficiency and quality.
3. Cost Efficiency By outsourcing manufacturing to an ODM, companies can reduce costs associated with production. The ODM often has established relationships with suppliers, enabling them to procure materials at lower prices and thus pass on savings to their clients.
4. Focus on Core Competencies Collaborating with an ODM allows businesses to concentrate on their core competencies, such as sales, marketing, and customer service, while leaving the complexities of design and manufacturing to specialists.
5. Accelerated Time-to-Market With an ODM managing the design and manufacturing process, businesses can significantly reduce their time-to-market. This expedited process can provide a competitive edge in rapidly changing industries.
Conclusion
In conclusion, the abbreviation ODM plays a crucial role in the landscape of centerless grinding. As companies strive for precision and efficiency, collaborating with an ODM can offer significant advantages, including customization, expertise, cost savings, a focus on core activities, and faster product launch times. Understanding such terms and their implications is essential for professionals in the manufacturing sector, ensuring that they remain competitive and responsive to market demands. As the industry continues to evolve, the partnership between companies and ODMs will likely become increasingly vital in achieving operational excellence.