The Role of Filmatic Technology in Centerless Grinder Machine Factories
In the realm of precision engineering, centerless grinding stands out as an essential method for producing cylindrical components with tight tolerances. The evolution of manufacturing techniques has led to the incorporation of various technologies aimed at enhancing productivity, efficiency, and overall quality. One such notable advancement is the integration of filmatic technology in centerless grinder machine factories. This article delves into the significance of filmatic systems in these environments, examining their benefits and applications.
Understanding Centerless Grinding
Centerless grinding is a machining process that removes material from the exterior of a cylindrical workpiece. Unlike traditional grinding, where the workpiece is held between two centers, centerless grinding allows for the piece to be fed through the grinding wheels, which eliminates the need for centering support. This method is particularly advantageous for high-volume production and is widely used in various industries, including automotive, aerospace, and medical device manufacturing.
What Is Filmatic Technology?
Filmatic technology involves the use of film-like mediums to display critical operational information and operational statuses in real-time. In the context of manufacturing, this technology serves as an interface between the machine operators and the grinding machines, enabling seamless communication and enhanced control over the production process. The implementation of filmatic systems in centerless grinder machine factories allows for improved monitoring, error detection, and overall operational efficiency.
Benefits of Filmatic Technology in Centerless Grinding
1. Enhanced Visualization Filmatic technology provides operators with a visual representation of the grinding process, including critical parameters such as wheel speed, workpiece feed rate, and grinding depth. This real-time visualization aids operators in making quick adjustments, ensuring that the grinding process remains within desired specifications.
2. Reduced Downtime One of the most significant advantages of filmatic systems is their ability to detect and alert operators to potential issues before they escalate into costly downtime. By monitoring machine performance and providing alerts for maintenance, these systems help factories maintain a continuous workflow, thereby increasing overall productivity.
filmatic for centerless grinder machine factories
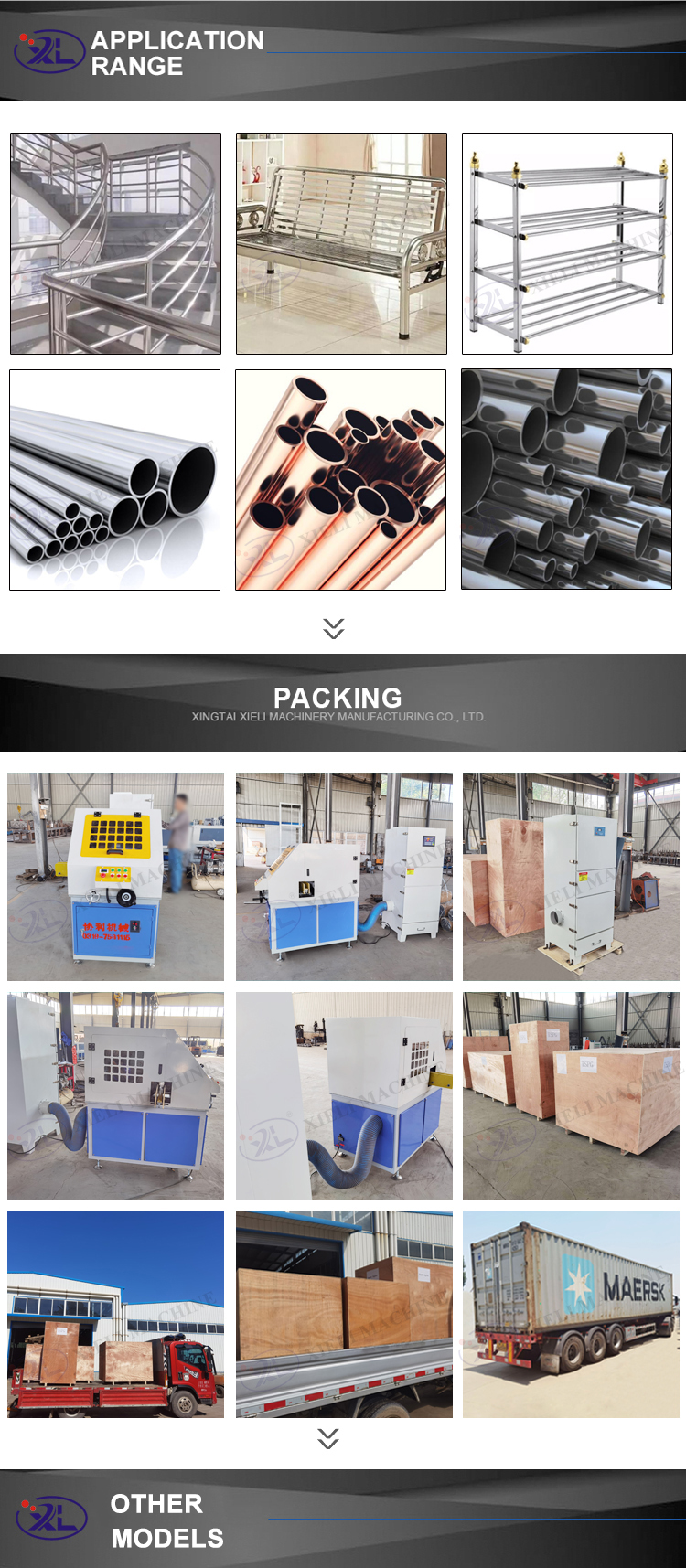
3. Improved Safety Safety is paramount in manufacturing environments. Filmatic technology enhances safety protocols by providing clear, immediate feedback about machine status and operator actions. For instance, an automated shutdown feature can be activated if an anomaly is detected, safeguarding both the equipment and personnel.
4. Efficient Training New operators can benefit significantly from filmatic interfaces, which often include instructional overlays and simulated scenarios. This feature facilitates a faster learning curve, reducing the time it takes for new employees to become proficient in operating centerless grinders.
5. Data Collection and Analytics Modern filmatic systems are equipped with data collection capabilities that log operational parameters over time. This data can be analyzed to identify trends, optimize processes, and implement preventive maintenance strategies, ultimately leading to enhanced machine performance and lifespan.
6. Customizability Every manufacturing process is unique, and filmatic technology can be tailored to meet specific operational needs. Customizable dashboards allow operators to prioritize the information most relevant to their tasks, making it easier to focus on what truly matters during the grinding process.
Future Trends
As demand for higher precision and lower costs continues to grow, the role of advanced technologies like filmatic systems in centerless grinder machine factories is likely to expand. Future developments may see further integration of artificial intelligence (AI) and machine learning algorithms with filmatic technologies. This integration could facilitate predictive maintenance, enabling factories to anticipate equipment failures even before they occur.
Conclusion
Filmatic technology is revolutionizing the way centerless grinder machine factories operate, driving improvements in efficiency, safety, and overall productivity. As manufacturers strive to meet ever-increasing demands for quality and precision, the role of innovative technologies such as filmatic systems will continue to be vital. By embracing these advancements, manufacturers can ensure they remain competitive in an increasingly complex global market, ultimately leading to enhanced outcomes for both operators and customers alike.