Internal Grinding Machines for Steel Pipes A Comprehensive Overview
In the world of industrial manufacturing, efficiency and precision are paramount. One area that has seen significant advancements is the internal grinding of steel pipes, which is crucial for ensuring the final products meet stringent quality standards. This article will explore the significance of internal grinding machines for steel pipes, their functionalities, challenges faced by manufacturers, and the future trends in this sector.
Importance of Internal Grinding for Steel Pipes
Internal grinding is a specialized form of grinding that focuses on the interior surfaces of tubular components, such as steel pipes. The process is essential for achieving the desired surface finish and dimensional accuracy. In industries ranging from automotive and aerospace to construction and oil & gas, steel pipes are integral components, and any imperfections can lead to systemic failures.
Proper internal grinding can enhance the mechanical properties of the pipes, such as tensile strength and fatigue resistance, thereby ensuring they can withstand extreme conditions. Moreover, it can eliminate any burrs and rough edges that may cause operational problems or safety hazards.
Functions of Internal Grinding Machines
Internal grinding machines designed for steel pipes typically incorporate advanced technology and engineering excellence. These machines are equipped with high-speed spindles and multi-point diamond dressing tools, enabling them to achieve high precision while maintaining an excellent surface finish.
1. Versatile Applications Internal grinding machines can cater to various pipe sizes and configurations, making them versatile for multiple applications. Manufacturers can customize their machines to handle different pipe materials and diameters, offering flexibility in their operations.
2. Consistent Quality These machines utilize computer numerical control (CNC) systems to automate the grinding process, ensuring consistent quality in production. With advanced software, manufacturers can set precise parameters for grinding, reducing the likelihood of human error, and ensuring uniformity across batches.
3. Enhanced Efficiency By incorporating automation and advanced tooling, internal grinding machines significantly reduce production time. High rotational speeds and rapid infeed rates allow for faster operations, directly impacting the bottom line for manufacturers.
Challenges in Internal Grinding
Despite the advancements in internal grinding technology, manufacturers face several challenges when processing steel pipes
steel pipe internal grinding machine factories
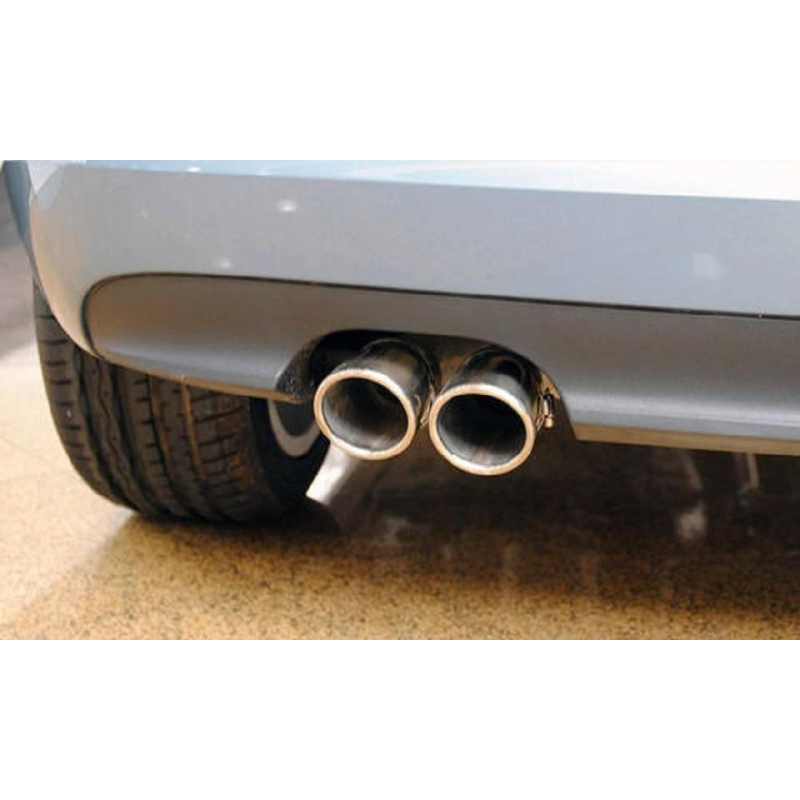
1. Material Variability The inconsistency in material quality can lead to variations in grinding performance. Manufacturers must ensure that raw materials meet specified standards before processing.
2. Tool Wear The high speeds and pressures involved in the grinding process can lead to rapid tool wear, necessitating regular maintenance and replacement. This can add to operational costs.
3. Environmental Regulations With growing environmental awareness, manufacturers must adhere to stringent regulations regarding noise, dust, and waste management. Implementing eco-friendly practices is now more critical than ever, placing additional pressure on manufacturers.
Future Trends in Internal Grinding Machines
The future of internal grinding machines for steel pipes is set to evolve with technological advancements
1. Smart Manufacturing The integration of Industry 4.0 technologies, such as IoT (Internet of Things), will enable real-time monitoring and data analysis. This capability will facilitate predictive maintenance and enhance operational efficiency.
2. Advanced Materials The advent of new materials such as high-strength alloys and composites will drive innovation in grinding techniques. Machines will need to adapt to handle these materials more efficiently.
3. Sustainability Initiatives As companies prioritize sustainability, the development of energy-efficient machines that minimize waste and reduce energy consumption will be a focal point for manufacturers.
4. User-Centric Design Future internal grinding machines will likely feature more intuitive user interfaces and automation capabilities to simplify operation and maintenance.
Conclusion
Internal grinding machines for steel pipes play a crucial role in ensuring the quality and performance of these vital industrial components. As technology continues to advance, manufacturers must adapt to meet the challenges and leverage opportunities in this dynamic field. By investing in state-of-the-art machinery and staying ahead of industry trends, companies can ensure they remain competitive in the global market, delivering high-quality steel pipes that meet the demands of various applications. The future of internal grinding technology looks promising, with endless possibilities for improvement and innovation.