The Importance of Coolant Management in Centerless Grinding
Centerless grinding is a machining process that has gained popularity due to its high efficiency and ability to produce precise, cylindrical parts without the need for a traditional work-holding device. A crucial aspect of this process is coolant management, which significantly impacts both the performance of the grinding operation and the quality of the finished product. This article delves into the role of coolant in centerless grinding and highlights the importance of selecting the right coolant product for optimal results.
The Role of Coolant in Centerless Grinding
Coolant serves multiple purposes in centerless grinding. Primarily, it helps to reduce the heat generated by the grinding wheel during operation. Excessive heat can lead to thermal damage, which may affect the material properties of the workpiece and cause premature wear on the grinding wheel. The coolant effectively dissipates heat, ensuring that the grinding process remains efficient and that the components maintain their integrity.
Additionally, coolant aids in lubricating the grinding process, minimizing friction between the workpiece and the grinding wheel. This lubrication not only helps enhance the material removal rate but also improves surface finish and dimensional accuracy. Furthermore, coolant assists in flushing away metal shavings and abrasive particles from the grinding zone, preventing them from interfering with the machining operation and maintaining a clean working environment.
Types of Coolant Products
When it comes to selecting a coolant for centerless grinding, manufacturers often have a variety of options, including soluble oils, semi-synthetic fluids, fully synthetic fluids, and straight oils
. Each type of coolant has its pros and cons, making it essential for operators to consider their specific needs1. Soluble Oils These are mixed with water to create an emulsion, offering great lubrication and cooling capabilities. They are suitable for various materials but can require more frequent maintenance, as they may harbor bacteria if not managed properly.
centerless grinder coolant product
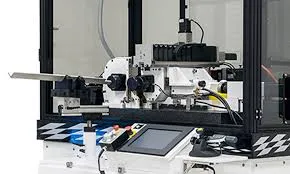
2. Semi-Synthetic Fluids These contain both oil and synthetic components, offering a balanced approach that combines the best of both worlds. They tend to have lower misting and better cooling properties, making them an excellent choice for high-speed grinding operations.
3. Fully Synthetic Fluids These coolants do not contain any oil and thus provide excellent cooling properties and lower viscosity. They are less likely to produce residue or bacterial growth, making them highly effective for clean operations. However, they may not provide as much lubrication as oil-based coolants.
4. Straight Oils These non-emulsifiable oils are primarily used for grinding operations where lubrication is more critical than cooling. While they provide optimal protection against wear, they can present challenges in terms of evaporative loss and clean-up.
Environment and Safety Considerations
Environmental and safety regulations have become increasingly strict, making it imperative for manufacturers to choose coolants that comply with local laws while maintaining worker safety. Many modern coolant products are designed to be biodegradable and free from harmful substances like chlorine, phenols, and other hazardous materials. This not only promotes a healthier workplace but also reduces the environmental impact of coolant disposal.
Conclusion
In conclusion, managing coolant in centerless grinding is vital for maximizing performance and ensuring product quality. Choosing the right coolant product can enhance the grinding process, improve surface finishes, and prolong the life of both the grinding wheel and the workpiece. By understanding the various coolant options available and their unique benefits, manufacturers can make informed decisions that will lead to more efficient operations and superior products. As the industry continues to evolve, embracing advancements in coolant technology will become increasingly paramount in achieving success in the competitive machining landscape.