Custom Tube Polishing Machine The Key to Enhanced Metal Finishing
In the world of metal processing, the finish of a product can significantly affect its marketability and functionality. For industries dealing with tubular products, be it in automotive, aerospace, or medical applications, the need for a quality finish is paramount. This is where custom tube polishing machines play a critical role, offering tailored solutions that meet the specific needs of different metallic surfaces.
A tube polishing machine is designed to buff and polish metal tubes to achieve a smooth and shiny finish. Unlike standard polishing equipment, a custom solution caters to the unique specifications and demands of a particular job. With features like adjustable speeds, variable polishing pressures, and specific polishing compounds, these machines can handle various materials and geometries, ensuring optimal results.
The Importance of Customization
The concept of customization in tube polishing is vital for several reasons. First, different industries use various metal types, including stainless steel, aluminum, copper, and more. Each of these materials has distinct properties that affect how it can be polished. For instance, stainless steel, commonly used in medical applications, requires a different polishing technique than aluminum, which is frequently utilized in the aerospace sector. Custom tube polishing machines are designed to handle these variances, providing the flexibility necessary for achieving high-quality results.
Moreover, the dimensions of the tubes also significantly impact the polishing process. Some tubes may have larger diameters or may be configured in complex shapes that standard machines cannot handle efficiently. Custom machines can be designed to accommodate these specifications, allowing manufacturers to maintain high productivity levels while achieving the desired finish.
Innovative Features
Today’s custom tube polishing machines come equipped with some of the latest technological advancements. Automation is one of the foremost enhancements, allowing for reduced labor costs and increased precision in the polishing process. By integrating robotic systems, manufacturers can achieve consistent finishes without the variability that can come from manual labor.
custom tube polishing machine
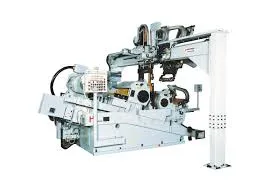
Additionally, modern tube polishing machines often incorporate programmable interfaces. This feature allows operators to set specific parameters for various materials, diameters, and finishes, ensuring that the machine functions optimally for each job. Operators can store multiple polishing profiles, making it easy to switch between products without extensive setup time.
Environmental considerations are also becoming increasingly important in manufacturing. Custom polishing machines can be designed to minimize waste and optimize the use of finishing compounds. Advanced filtration systems can reuse polishing liquids, which not only conserves resources but also reduces the environmental impact of the polishing process.
Benefits of Using Custom Tube Polishing Machines
Investing in custom tube polishing machines not only improves the finish quality but also enhances overall productivity. Manufacturers can streamline their processes, reducing the time taken for polishing and allowing for quicker turnaround on projects. This efficiency can lead to increased profitability and a stronger competitive edge in the market.
Furthermore, with a high-quality finish, products are more likely to meet industry standards and customer expectations. This can result in fewer reworks and returns, saving time and resources. In sectors such as aerospace and medical, where regulations are strict, having a reliable polishing solution can ensure compliance and minimize risks associated with product failures.
Conclusion
In an era where precision engineering and quality finishes are key competitive factors, custom tube polishing machines stand out as invaluable assets for many manufacturers. With their ability to cater to specific industry needs and their incorporation of advanced technology, these machines are essential for producing finished products that not only meet but exceed market expectations. Investing in a custom solution is not merely an option; it is a strategic move that enhances quality, efficiency, and ultimately, business success.