Troubleshooting OEM Centerless Grinders A Comprehensive Guide
Centerless grinders are essential machines in the manufacturing and machining industries, allowing for the efficient grinding of cylindrical parts without the need for a spindle. However, like any industrial equipment, they can encounter problems that may affect their performance. This article will delve into common issues faced with OEM centerless grinders and offer troubleshooting tips to ensure their smooth operation.
Identifying Common Issues
Before diving into troubleshooting, it’s crucial to identify the common problems that may arise in centerless grinders. These include
1. Inconsistent Part Size One of the primary issues in centerless grinding is achieving uniformity in part size. Variations can stem from incorrect setup, worn wheels, or machine misalignment.
2. Increased Cycle Time If the grinding process is taking longer than usual, it could signal wheel wear, incorrect speed settings, or a slowdown in material feed.
3. Poor Surface Finish A rough finish on the part can indicate a problem with the grinding wheel, improper setup, or contamination.
Troubleshooting Steps
1. Check Setup and Alignment
Ensure that the workpiece is correctly aligned in the machine. Misalignment can lead to inconsistent grinding and should be adjusted before further diagnosis. Additionally, verify that the regulating wheel is positioned correctly. Using dial indicators can help check alignment.
2. Inspect Grinding Wheels
oem centerless grinder troubleshooting
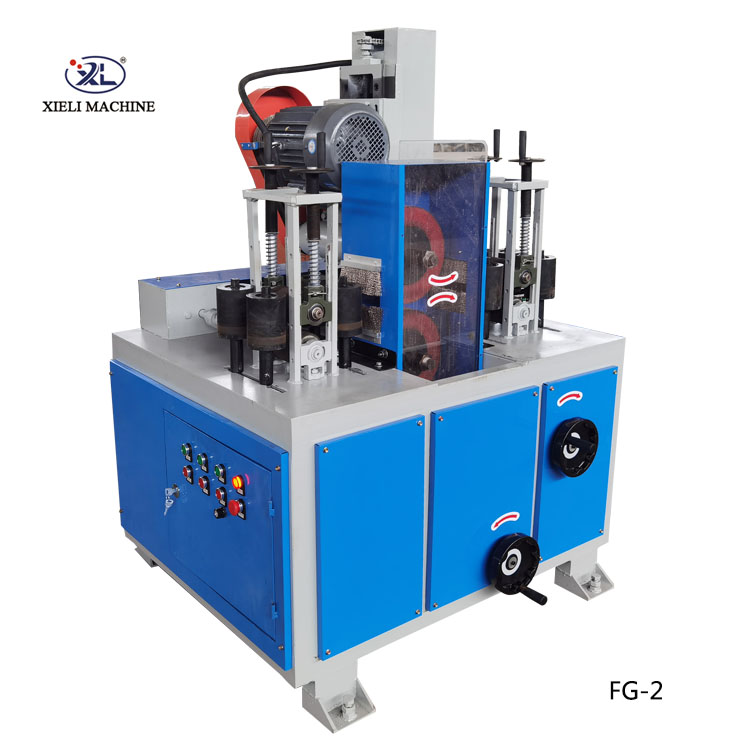
Grinding wheels wear out over time and can affect the quality and consistency of the grind. Inspect the wheels for signs of wear, cracks, or chips. If the wheels appear damaged, they should be replaced. Selecting the correct wheel for the material being ground is also crucial; differents materials and shapes require specific wheel compositions.
3. Assess Feed Rates and Speed Settings
Check the feed rate and wheel speed settings. If the feed rate is too high, it can lead to a reduction in surface finish quality and an increase in cycle time. Conversely, too slow of a feed rate might lead to overheating. Always refer to the manufacturer's specifications for optimal settings.
4. Examine Coolant Supply
The coolant plays a vital role in dissipating heat during the grinding process. Insufficient coolant flow can lead to overheating, which can damage the workpiece and the grinding equipment. Regularly check coolant levels and ensure the system is free of blockages.
5. Look for Signs of Vibration
If the grinder is exhibiting unusual vibrations or noises, stop the machine immediately and inspect it for any loose components, such as bolts or fixtures. Ensure that the machine is securely installed on a stable platform to minimize vibrations.
6. Routine Maintenance
Regular maintenance is key to preventing issues with centerless grinders. This includes routine cleaning, checking for wear on various components, lubricating moving parts, and recalibrating as necessary. Following a maintenance schedule recommended by the OEM can prolong the machine's lifespan and effectiveness.
Conclusion
Troubleshooting OEM centerless grinders can be daunting, but following these steps can help identify and resolve common issues. Regular maintenance, careful setup, and prompt inspections can greatly reduce downtime and enhance productivity. Should problems persist despite these troubleshooting efforts, consulting the OEM’s service manual or seeking professional assistance is advisable. This proactive approach not only ensures smoother operations but also helps maintain high-quality standards in machining processes.