Exploring the Benefits of Using a Centerless Grinder
In the world of manufacturing and machining, precision is paramount. One of the key tools that professionals rely on for achieving superior accuracy in the shaping and finishing of metal components is the centerless grinder. This piece of equipment has revolutionized the machining process for various industries by offering unmatched efficiency, versatility, and precision. In this article, we will delve into the workings of centerless grinders, their advantages, and their common applications.
What is a Centerless Grinder?
A centerless grinder is a type of grinding machine that operates without the need for a spindle or other mechanisms to hold the workpiece in place. Instead, the workpiece is supported by a combination of a grinding wheel and a regulating wheel. The grinding wheel performs the cutting action, while the regulating wheel controls the rotation and feed rate of the piece being ground. This unique design allows for continuous operation, resulting in a higher output compared to traditional grinding methods.
Advantages of Centerless Grinding
1. High Efficiency and Productivity One of the standout benefits of centerless grinders is their ability to handle multiple pieces simultaneously. This capability significantly reduces production times, making them particularly advantageous for high-volume production environments. Operators can feed a continuous length of material, which is processed without the need for frequent setup changes.
2. Increased Precision Centerless grinding provides excellent dimensional accuracy. The absence of a spindle allows for easier handling of elongated workpieces, ensuring that they maintain tight tolerances. This feature is especially essential in industries such as automotive and aerospace, where precision-engineered parts are critical.
craigslist.org dedtru centerless grinder
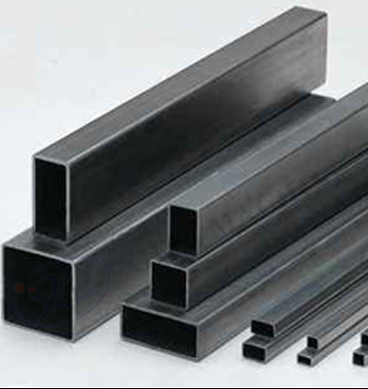
3. Flexibility in Part Size Another considerable advantage is the ability to grind workpieces with varied shapes and sizes. Whether dealing with small rods or larger, more intricate shapes, centerless grinders can accommodate a range of specifications. This flexibility makes them useful in diverse applications, from manufacturing simple components to more complex geometries.
4. Reduced Costs While the initial investment in a centerless grinder can be significant, the operational efficiencies gained typically result in reduced long-term costs. The increased output, combined with the lower labor costs associated with automated setups, means that businesses can recover their investment relatively quickly.
5. Consistent Surface Finish The continuous grinding process yields a smooth surface finish, which is crucial for parts that require minimal friction and higher performance. A consistent surface finish not only enhances the aesthetic appeal of products but also extends their operational lifespan by reducing wear.
Common Applications
Centerless grinders find applications across various sectors. In the automotive industry, they are used to grind parts such as shaft components, bushings, and bearings. Fabrication shops utilize them for processing tubing and other elongated materials. Additionally, centerless grinding is also employed in the manufacturing of medical devices, where precision and surface quality are critical.
Conclusion
As industries continue to evolve and the demand for precision-engineered components rises, centerless grinders are increasingly becoming indispensable tools in manufacturing. Their ability to enhance efficiency, precision, and consistency while reducing production costs makes them a valuable asset for any machining operation. Investing in a centerless grinder not only streamlines the production process but also positions a business for success in a competitive marketplace. As more companies recognize these advantages, the adoption of this technology is likely to grow, further solidifying its role in the future of manufacturing.