Understanding Thru-Feed Centerless Grinders A Key in Manufacturing
Thru-feed centerless grinders are essential machinery in the manufacturing sector used for precision grinding of cylindrical parts. Unlike traditional grinding methods, this innovative technology streamlines the process by allowing for continuous feeding of workpieces. This article explores the significance of thru-feed centerless grinders, their applications, advantages, and the vital role they play in various manufacturing factories.
The Mechanism of Thru-Feed Centerless Grinders
Thru-feed grinding operates on a simple yet effective principle. A workpiece is fed through two grinding wheels—a stationary wheel that serves as the grinding surface and a rotating wheel that regulates the speed and motion. The design eliminates the need for complex setups, enabling a seamless operation where parts can be ground on both ends in a single pass. This process is particularly beneficial for high-volume production runs, where efficiency and speed are critical.
Applications in Manufacturing
Thru-feed centerless grinders find applications across numerous industries. Commonly used in the production of small to medium-sized cylindrical components, these machines excel in grinding parts like shafts, rods, and tubes. Industries such as automotive, aerospace, and even medical device manufacturing benefit greatly from this grinding technology as it ensures high precision and repeatability in part dimensions.
In the automotive industry, for instance, components such as valve stems and fuel injectors require precise tolerances for optimal performance. Through the use of thru-feed centerless grinders, manufacturers can achieve the necessary precision while maintaining productivity. Similarly, in the aerospace sector, the demand for lightweight and highly engineered components makes this grinding method even more valuable.
thru feed centerless grinder factories
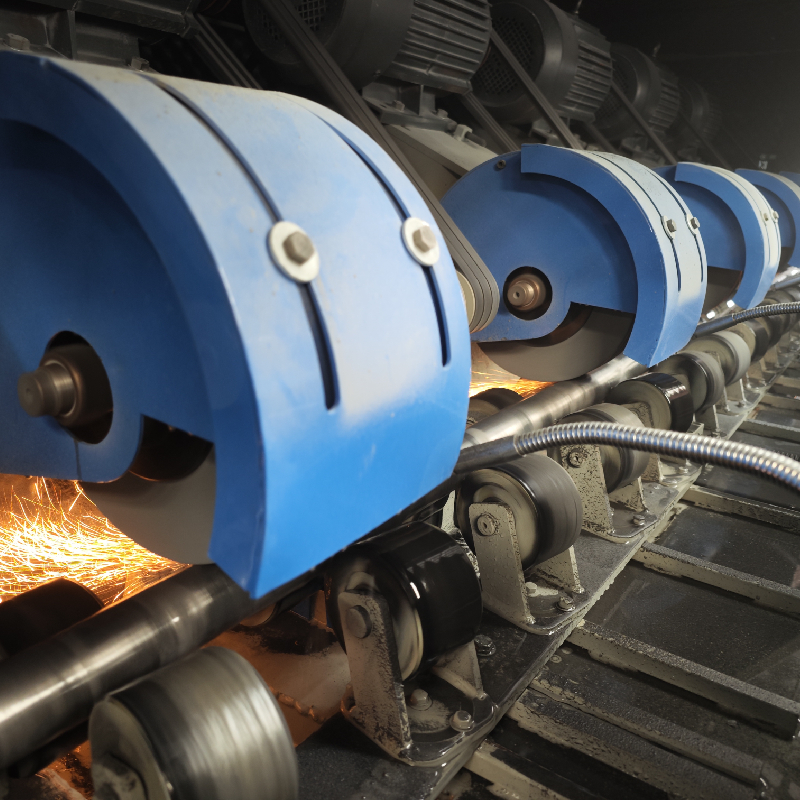
Advantages of Thru-Feed Centerless Grinding
One of the most significant advantages of thru-feed centerless grinding is its efficiency. Because the workpiece is continuously fed through the machine, there is minimal downtime associated with loading and unloading, which leads to increased throughput. Additionally, the process allows for multiple components to be ground simultaneously, thereby saving time and reducing labor costs.
Another benefit is the consistency and accuracy it offers. Thru-feed grinding minimizes variables that can lead to dimensional discrepancies. The geometry and setup of the machine ensure that each workpiece is treated uniformly, which is vital for industries where precision is non-negotiable.
Moreover, thru-feed grinders are designed for ease of use and maintenance. Operators can quickly set up the machines and make adjustments as needed, enhancing productivity in dynamic manufacturing environments. With advancements in technology, many modern grinders also come equipped with automation features, allowing for greater precision and reduced human error.
Conclusion
In summary, thru-feed centerless grinders represent a pivotal advancement in manufacturing technology. They provide manufacturers with the ability to produce high volumes of precision ground parts efficiently. Their application ranges across various industries, showcasing their versatility and reliability. As manufacturing continues to evolve with technological advancements, the importance of thru-feed centerless grinders is likely to grow, ensuring that they remain integral to the production processes of the future. Investing in this technology is a step towards enhancing operational efficiency, precision, and ultimately, competitive advantage in the global market.