Understanding Through-Feed Centerless Grinders A Key to Precision Manufacturing
In the realm of precision manufacturing, achieving high tolerances and consistent part quality is crucial. One of the most effective methods for processing cylindrical parts is through-feed grinding using centerless grinders. These machines, known for their efficiency and ability to produce high-volume outputs, are an important asset in various industries, from automotive to aerospace.
What is Through-Feed Centerless Grinding?
Through-feed centerless grinding is a method where the workpiece passes through the grinding wheels without needing to be manually loaded and unloaded between operations. In this process, the part is supported by a steady rest and is driven by a regulating wheel while being ground by a grinding wheel. The ability of the grinder to continuously feed parts into the machine allows for impressive throughput with minimal downtime, making it an ideal choice for high-volume applications.
How Does Through-Feed Centerless Grinding Work?
The setup consists of two main wheels the grinding wheel and the regulating wheel. The grinding wheel is positioned at an angle to the workpiece, and the regulating wheel is placed at a lower angle, creating a feeding orientation that holds the part in place. The regulating wheel's speed controls the speed of the part as it passes through the grinding zone. As the part moves through, the grinding wheel removes material, achieving the desired diameter and finish.
A critical aspect of through-feed grinding is its ability to grind straight cylindrical parts with precision. Because the part is continuously fed and the alignment is integral to the machine's operation, it is essential for the parts to have uniform dimensions. This technique is not suitable for irregularly shaped or very short parts, which often necessitate different grinding methods.
Advantages of Through-Feed Centerless Grinders
The primary advantage of through-feed centerless grinding lies in its efficiency. This method can produce thousands of parts in a day, depending on the size and specification of the parts. Furthermore, this process reduces handling time, as parts are automatically fed through the grinder, which minimizes human error and enhances productivity.
through feed centerless grinder product
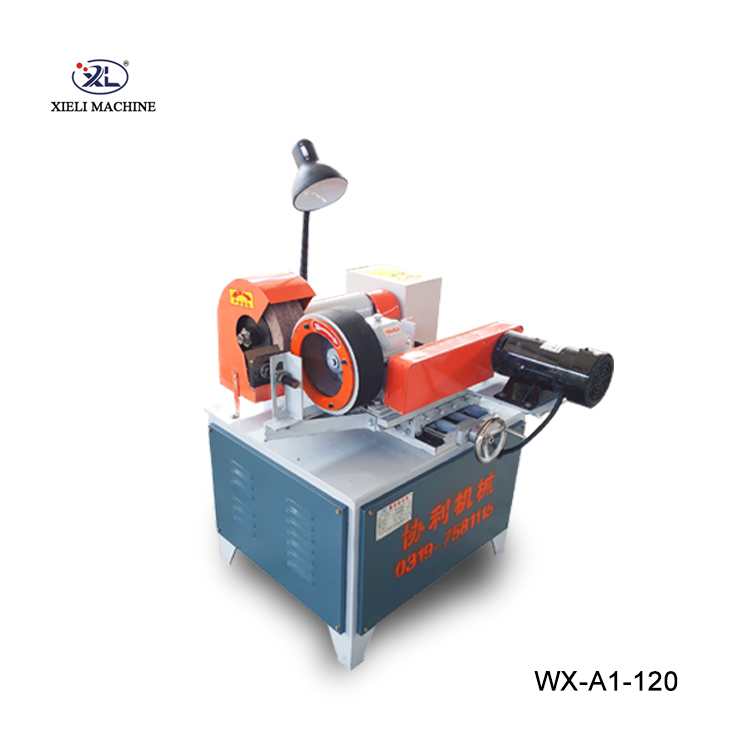
Another significant benefit is the high degree of precision it offers. Through consistent grinding processes and advanced controls, manufacturers can achieve tolerances as tight as ±0.0001 inches. Such precision is crucial in industries where even slight variances can lead to substantial operational issues.
Centerless grinding also generates a superior surface finish, which is essential for ensuring the durability and performance of components. Many industries require parts to meet stringent surface finish requirements, and through-feed centerless grinders excel in delivering high-quality finishes.
Applications of Through-Feed Centerless Grinders
Through-feed centerless grinders are commonly used in manufacturing industries where cylindrical parts are prevalent. Common examples include
1. Automotive Industry Components such as axles, shafts, and bearings are often manufactured using this process. 2. Aerospace Parts needed for engines and landing gear require precise tolerances that through-feed grinding can accommodate. 3. Medical Devices Components such as syringes and orthopedic implants benefit from the precision and surface finish attainable through this grinding method.
Choosing the Right Through-Feed Centerless Grinder
When selecting a through-feed centerless grinder, it is vital to consider several factors including the types of materials you work with, the required tolerances, and output volume. Additionally, assessing the machine's maintenance requirements and the availability of technical support is essential for ensuring long-term operational efficiency.
In a world where precision manufacturing is increasingly critical, through-feed centerless grinders offer significant advantages in terms of speed, accuracy, and versatility. By enabling the production of high-quality cylindrical parts at scale, these machines play an essential role in various industries, ultimately contributing to better performance and reliability in the products we use every day. Embracing this technology allows manufacturers to keep pace with market demands while continuously striving for excellence.