The Evolution and Significance of Table Top Centerless Grinders
In the realm of precision machining, the table top centerless grinder has emerged as a vital tool for achieving high levels of accuracy and efficiency. These compact machines are designed to grind cylindrical parts with minimal operator intervention, making them an essential asset for small and medium-sized manufacturing units. In this article, we will explore the features, benefits, and applications of table top centerless grinders, as well as their significance in various industries.
What is a Table Top Centerless Grinder?
A table top centerless grinder is a type of grinding machine that operates without the use of a machine center, allowing for rapid and efficient material removal. Unlike traditional cylindrical grinders, which require the workpiece to be centered and clamped, centerless grinders employ a simplistic yet effective mechanism. The workpiece is supported by a regulating wheel and a grinding wheel, which work in tandem to perform the grinding process. The lack of a center means that operators can quickly change out parts and work on larger batches without extensive setup time.
Features of Table Top Centerless Grinders
These machines come with a variety of features that enhance their usability and efficiency
1. Compact Design The table top configuration saves space, making it ideal for small workshops or areas with limited room. 2. Ease of Use Many modern centerless grinders are equipped with user-friendly controls and digital displays, enabling operators to set precise parameters quickly. 3. Versatility Table top centerless grinders can handle a diverse range of materials including metals, plastics, and composite materials, making them suitable for various industries. 4. High Precision By maintaining tight tolerances, these machines produce parts that meet strict specifications, vital for industries such as aerospace and automotive. 5. Low Maintenance Their simpler design translates to reduced wear and tear, which enhances longevity and decreases maintenance costs.
Benefits of Using Table Top Centerless Grinders
table top centerless grinder factory
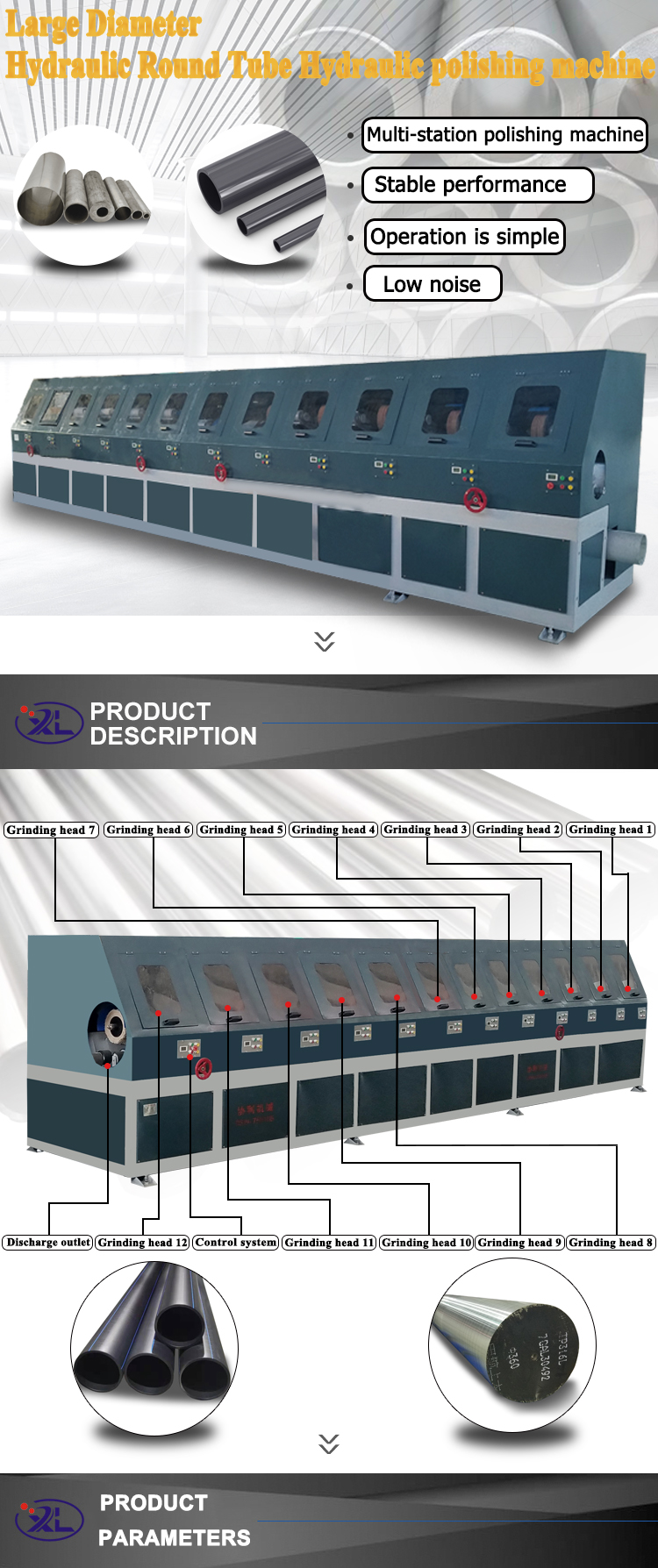
The adoption of table top centerless grinders offers numerous advantages to manufacturers. Firstly, their ability to maintain tight tolerances translates to higher quality products. This is particularly important in sectors where precision is critical, such as electronic components or medical devices.
Moreover, the speed of operation allows for increased productivity. Manufacturers can process more parts in a shorter time frame, facilitating higher output rates. This not only improves profitability but also helps in meeting customer demands swiftly. Additionally, their low energy consumption further enhances cost-effectiveness.
Applications Across Industries
The versatility of table top centerless grinders allows them to be utilized in a myriad of applications. The automotive industry frequently employs these machines for grinding components such as axle shafts, bearings, and valve stems. Similarly, manufacturers of aerospace parts rely on centerless grinding to produce intricate components with stringent requirements for performance and safety.
Other fields such as medical device manufacturing, where precision and sterility are paramount, also benefit from the efficient and clean operation of table top centerless grinders. Moreover, the furniture and construction industries use these machines for creating custom hardware, showcasing the breadth of applications available.
Conclusion
Table top centerless grinders play an indispensable role in the manufacturing landscape, thanks to their practicality, efficiency, and precision. As industries continue to evolve and demand higher quality products at faster turnaround times, the importance of these machines will only grow. Investing in a table top centerless grinder could very well be a game-changer for companies looking to enhance their production capabilities and maintain a competitive edge. Whether in the automotive, aerospace, or medical fields, the impact of table top centerless grinders is undeniably significant, paving the way for future advancements in manufacturing technology.