The Evolution and Importance of Surface Grinders and Centerless Grinding Products
In the realm of manufacturing and machining, the precision and efficiency of processes are paramount. Among the crucial tools that ensure high accuracy and smooth finishes are surface grinders and centerless grinding machines. These tools have evolved significantly over the years, adopting advanced technologies and methodologies to meet the demands of modern industries.
Understanding Surface Grinders
Surface grinders are essential machines used primarily in the manufacturing industry for producing flat surfaces. The grinding process involves a rotating wheel covered in abrasive particles, which removes material from the workpiece to achieve the desired surface finish and dimensions. Surface grinding is indispensable in applications where a high degree of flatness and dimensional tolerances are required.
The operation of surface grinders has transformed over the years. In the past, manual surface grinders required skilled operators to control the speed and feed of the wheel and the workpiece. However, with the advent of CNC (Computer Numerical Control) technology, surface grinding has become more automated. Modern CNC surface grinders can achieve remarkable levels of precision and repeatability, making them ideal for high-volume production environments. This automation reduces the risk of human error and enhances overall productivity.
The Role of Centerless Grinding
Centerless grinding is a unique and efficient machining process that differs significantly from traditional grinding methods. In this process, the workpiece is held in place by two rotary grinding wheels—one regulating wheel and one grinding wheel—without the need for a spindle or fixture. This innovative setup allows for the continuous feeding of workpieces, making centerless grinding particularly suitable for high-volume production runs.
One of the key advantages of centerless grinding is its ability to grind parts with consistent dimensions and surface finishes. This method is particularly effective for cylindrical parts, such as shafts, pins, and rods. The design of the centerless grinding system allows for faster processing times and the ability to work on longer workpieces, which can be a significant advantage in manufacturing operations.
Applications of Surface and Centerless Grinding Products
surface grinder centerless grinding products
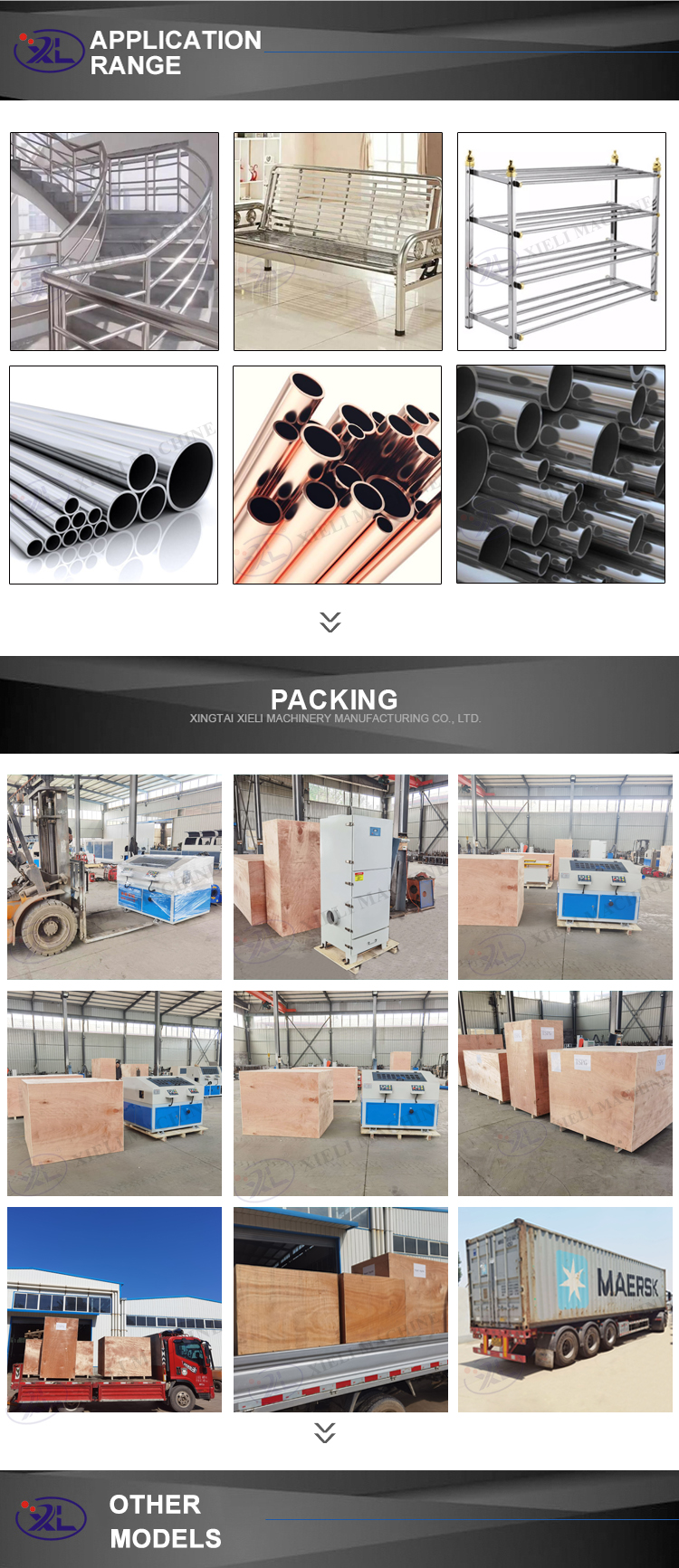
Both surface grinders and centerless grinding machines find applications across various industries, including automotive, aerospace, medical, and consumer goods. For instance, in the automotive industry, surface grinding is used to achieve flat surfaces on components like brake discs and engine blocks. Meanwhile, centerless grinding is critical for producing precision components such as fuel injectors and transmission shafts.
In the medical field, where precision is vital, both surface and centerless grinders are employed to manufacture surgical instruments and implants. The precision required in these components ensures that they function correctly and safely when used in medical procedures.
Innovations and Future Trends
As manufacturing processes continue to evolve, so do surface and centerless grinding technologies. Current trends include the integration of smart technologies, such as IoT (Internet of Things) capabilities, into grinding machines. These innovations allow for real-time monitoring of machine performance, predictive maintenance, and improved process optimization.
Additionally, advancements in abrasives and grinding wheel technologies are leading to better material removal rates and surface finishes. For example, diamond and CBN (Cubic Boron Nitride) wheels are increasingly popular for their longevity and effectiveness in grinding hard materials.
Sustainability is also becoming a critical consideration in the design and operation of grinding machines. Manufacturers are looking for ways to reduce waste and energy consumption, resulting in the development of more eco-friendly grinding solutions.
Conclusion
In summary, surface grinders and centerless grinding machines are integral to modern manufacturing processes, driving efficiency and precision across various industries. Their evolution reflects the overall advancement in machining technology, showcasing the importance of innovation in maintaining competitiveness in a global market. As industries continue to demand higher performance and sustainability, the future of grinding processes will undoubtedly see exciting developments that further enhance their capabilities.