The Importance of Surface Grinding and Centerless Grinding in Modern Manufacturing
In the ever-evolving world of manufacturing, precision and efficiency are non-negotiable. Among the myriad of machining processes employed in the industry, surface grinding and centerless grinding stand out as essential techniques that contribute significantly to the production of high-quality components. Companies specializing in these grinding processes have become cornerstones in various sectors, delivering exceptional results that meet stringent industry standards.
What is Surface Grinding?
Surface grinding is a manufacturing process that involves the use of a rotating abrasive wheel to remove material from the surface of a workpiece, achieving a flat and smooth finish. This technique is critical for producing parts that require tight tolerances and superior surface finishes. Surface grinding machines come in various configurations, designed to accommodate different sizes and shapes of workpieces. The versatility of these machines makes them applicable in industries such as aerospace, automotive, and tool making.
The process of surface grinding is not just about removing material; it's about precision. The ability to achieve flatness, parallelism, and a fine surface finish is vital for components that must fit together perfectly or have minimal friction. For instance, in the aerospace industry, components that undergo surface grinding must meet rigorous specifications to ensure safety and reliability.
Understanding Centerless Grinding
Centerless grinding, on the other hand, is a process where the workpiece is supported not by centers but by a regulating wheel and a grinding wheel. This method allows for the continuous production of cylindrical parts without the need for a fixture to hold the workpiece. Centerless grinding is particularly advantageous for high-volume production and is widely used in the manufacturing of shafts, pins, and other cylindrical components.
One of the significant benefits of centerless grinding is its ability to process long and slender workpieces with high accuracy. The regulating wheel controls the workpiece's rotation and feeds it into the grinding wheel, ensuring a consistent diameter is maintained throughout the length of the part. This makes it an ideal choice for industries that demand mass production of precise cylindrical components.
surface grinder centerless grinding company
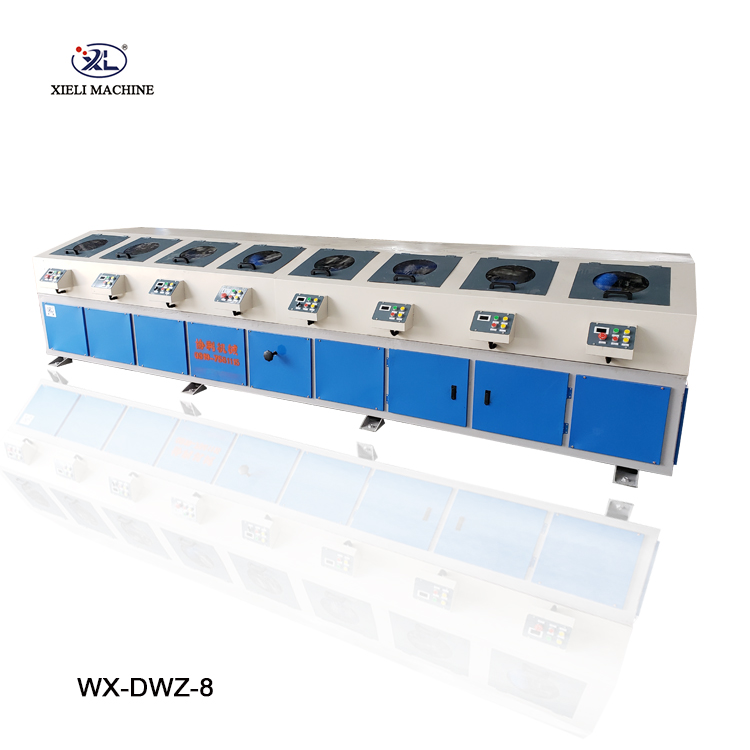
Benefits of Both Processes
Both surface grinding and centerless grinding offer valuable benefits to manufacturers. They allow for the production of parts with exceptional dimensional accuracy and surface finishes that are crucial for the performance of the final product. Moreover, these processes are capable of handling a wide range of materials, from metals to plastics, broadening their applicability across different sectors.
From a cost-effectiveness standpoint, both grinding methods can be highly efficient, especially in a production environment. They can reduce secondary processing steps by delivering parts that are ready for assembly or use. This capability not only saves time but also minimizes the risk of defects that can arise during additional handling or machining steps.
Choosing the Right Company
When selecting a surface grinding or centerless grinding company, it’s essential to assess their capabilities, experience, and equipment. A reputable company will have a robust quality control system to ensure that every part meets the required specifications. Look for firms that have invested in modern grinding technology, as advancements in machine capabilities can significantly enhance precision and efficiency.
Moreover, a knowledgeable customer service team can be invaluable, helping clients select the right grinding processes and materials for their specific needs. Collaboration between the manufacturer and the grinding service can lead to optimized production processes and improved overall product quality.
Conclusion
In conclusion, the significance of surface grinding and centerless grinding in modern manufacturing cannot be overstated. These processes not only enhance the precision and quality of manufactured components but also contribute to the efficiency and cost-effectiveness of production. As industries continue to strive for greater accuracy and performance, the role of grinding companies will become increasingly vital. Embracing these advanced grinding techniques is essential for any manufacturer aiming to stay competitive in today’s dynamic market.