Understanding Surface Grinding and Centerless Grinding A Comprehensive Overview
In the world of manufacturing and metalworking, precision is paramount. Two critical processes that play significant roles in achieving high levels of accuracy are surface grinding and centerless grinding. Although they serve distinct purposes, both methods are essential for producing finely finished products with tight tolerances. This article aims to unpack these two grinding processes, providing a clear understanding of their functions, applications, and the technology behind them.
Surface Grinding
Surface grinding is a popular machining process used to create a smooth finish on flat surfaces. It involves the use of a rotating grinding wheel that removes material from the workpiece, effectively creating a flat and even surface. The grinding wheel is composed of abrasive particles that grind away the material as it spins against the workpiece. This method is particularly effective for achieving a high degree of accuracy and surface finish.
The operation of a surface grinder can be performed in various ways, including horizontal, vertical, and rotary configurations. The choice of machine type often depends on the specific requirements of the project. For instance, horizontal grinders are typically used for larger workpieces, while vertical grinders are favored for smaller components or those requiring more precise control.
Surface grinding can be used on various materials, including metals, ceramics, and plastics. Its applications are widespread, ranging from automotive and aerospace industries to tool manufacturing, where precision and surface quality are critical. The main advantages of surface grinding include high precision, versatility, and the ability to produce flat surfaces.
Centerless Grinding
Centerless grinding, on the other hand, is a production grinding method that does not require the workpiece to be fixed. Instead, it is held in place by a combination of wheels a grinding wheel and a regulating wheel. This unique setup allows the workpiece to be fed through the grinding process, removing material without the need for any workpiece alignment or setup, greatly enhancing efficiency.
surface grinder centerless grinding
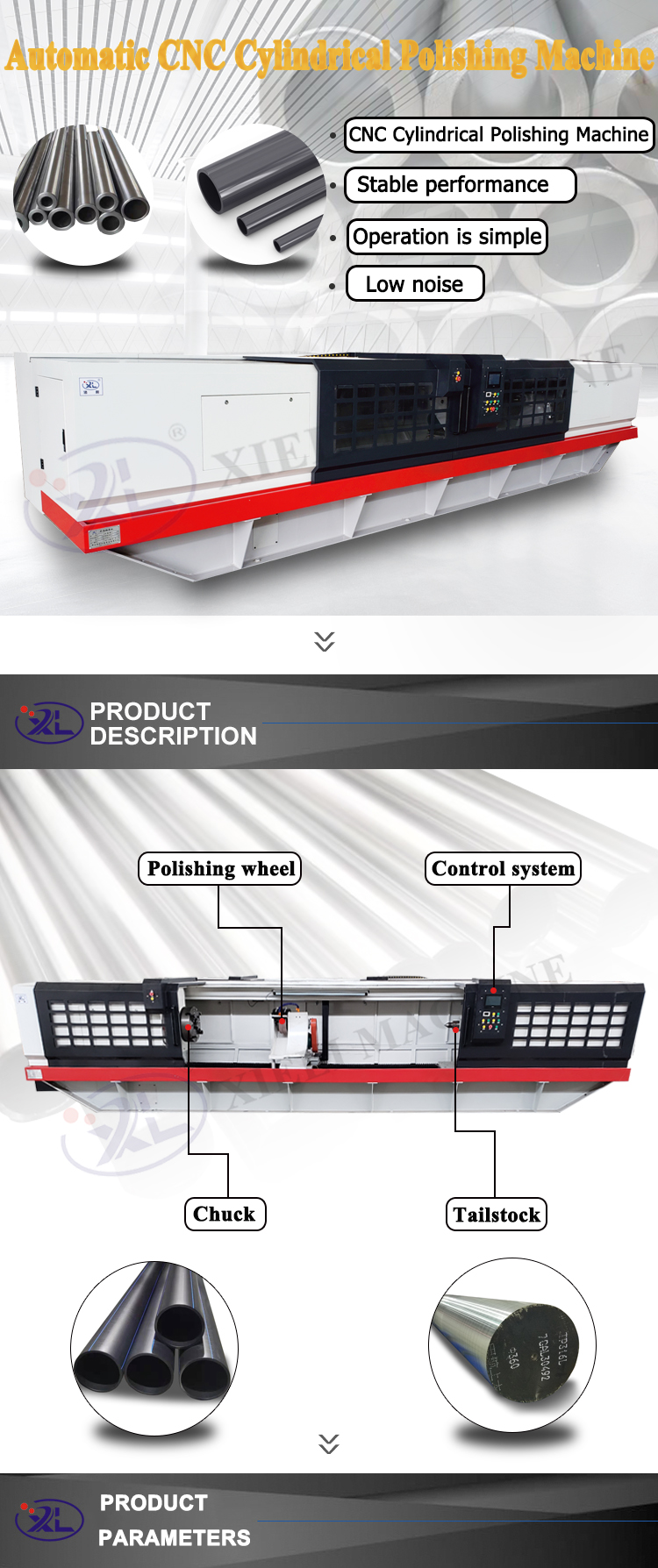
This process is often used for cylindrical parts, as it enables the grinding of round surfaces while maintaining tight tolerances and high production rates. Centerless grinding excels in the production of components like shafts, pins, and rods, where consistency and uniformity are essential.
There are two primary types of centerless grinding through-feed grinding and in-feed grinding. Through-feed grinding is used for workpieces that have a uniform round shape and can be fed continuously through the machine. In-feed grinding, on the other hand, is suitable for workpieces that are not of uniform shape or require a more complex grinding process, enabling larger parts to be ground accurately.
Key Differences and Synergies
While both surface grinding and centerless grinding focus on material removal for the creation of precise components, they differ in their methodologies and applications. Surface grinding is primarily focused on flat surfaces, making it essential for applications needing precision in one or two dimensions. Centerless grinding, however, is adept at processing cylindrical shapes efficiently and is often employed in high-volume production environments.
Despite their differences, these two grinding techniques can be used in tandem to achieve comprehensive manufacturing solutions. For example, a manufacturing facility may utilize surface grinding for initial finishing of a flat area on a cylindrical workpiece, whereas centerless grinding can be employed for final shaping, improving overall productivity and consistency in part quality.
Conclusion
In conclusion, surface grinding and centerless grinding are integral processes within the manufacturing domain, each offering unique advantages and applications. Understanding these methods allows manufacturers to select the appropriate techniques for their specific requirements, ensuring their products meet the necessary precision and quality standards. Whether it’s surface finishing or cylindrical shaping, mastering these grinding techniques is vital for any factory aiming to enhance its production capabilities and deliver top-notch products to its customers. As technology continues to evolve, the efficiency and applications of these grinding processes will only expand, further solidifying their importance in the manufacturing landscape.