The Role of Surface Grinders and Centerless Grinding in Modern Manufacturing
In the realm of manufacturing, precision is paramount. Among the various techniques employed to achieve the required dimensions and surface finishes, surface grinding and centerless grinding stand out as essential processes. Together, they enhance efficiency and precision in production, serving a wide array of industries.
Surface grinding is a finishing process that utilizes a rotating wheel covered in abrasive particles to remove materials from a workpiece, resulting in a flat, smooth surface. This technique is vital in scenarios where tight tolerances and high surface quality are crucial, such as in the aerospace and automotive sectors. The surface grinder itself is an advanced piece of machinery that combines sophisticated technology and operator skills to ensure that the final product meets exact specifications.
On the other hand, centerless grinding is predominantly used for cylindrical parts where the workpiece is held in place by two rotating wheels, one for grinding and the other for regulating the speed of the workpiece. This method is particularly advantageous for mass production as it allows for continuous operation without the need for intricate setups. Centerless grinding is commonly employed for manufacturing components such as shafts, rods, and pins. The primary benefit of this process is its ability to achieve high throughput rates while still delivering a consistent finish.
The factories that specialize in these grinding techniques leverage state-of-the-art technology and skilled labor. They often invest in CNC (Computer Numerical Control) machines that can automate grinding processes, enhancing precision and reducing human error. The combination of advanced machinery and meticulous craftsmanship in these factories positions them to meet the diverse demands of current manufacturing needs.
surface grinder centerless grinding factories
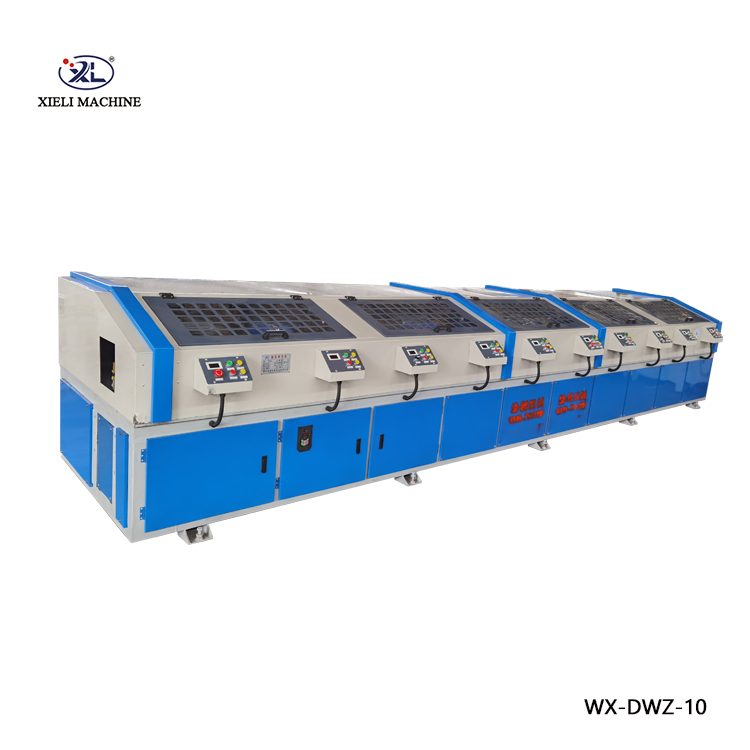
Furthermore, the versatility of surface and centerless grinding allows manufacturers to work with various materials, including metals like steel, aluminum, and exotic alloys. This adaptability is essential to industries such as medical device manufacturing, where specific material properties and stringent compliance standards are required.
Businesses are increasingly recognizing the importance of integrating quality control measures into their grinding processes, which has paved the way for the development of specialized factories that focus exclusively on grinding operations. These factories prioritize not only the quantity of production but also the quality, ensuring that each component produced meets exacting manufacturing standards.
As sustainable practices gain traction in the manufacturing industry, there is also a growing emphasis on minimizing waste and optimizing energy use. Factories are adopting environmentally friendly grinding wheels and employing coolant systems that reduce environmental impact while enhancing efficiency.
In conclusion, surface grinding and centerless grinding are critical components of modern manufacturing, contributing significantly to the production of high-precision components across various industries. The evolution of technology in these processes not only enhances productivity but also ensures that quality and sustainability remain at the forefront of manufacturing practices. The continued investment in and innovation of grinding techniques is essential for factories to remain competitive and meet the ever-evolving demands of the global market.