The Evolution and Importance of Square and Rectangle Tube Polishing Machines
In today's fast-paced manufacturing environment, the need for precision and quality is paramount. Industries ranging from construction to automotive and furniture increasingly depend on efficient and reliable processing of metal components. Among these vital processes, tube polishing has emerged as a key operation, particularly for square and rectangular tubes. The advancements in square and rectangle tube polishing machines have revolutionized the way manufacturers approach the finishing of their products.
Understanding Tube Polishing
Polishing is a surface treatment that enhances the aesthetic and functional qualities of tubes. The goal of tube polishing is not only to improve the appearance but also to eliminate surface defects, enhance corrosion resistance, and prepare tubes for subsequent processes like coating or welding. Square and rectangular tubes, given their geometric characteristics, present unique challenges in polishing due to their corners and edges. Therefore, specialized polishing machines have been developed to cater to these specific shapes.
The Role of Tube Polishing Machines
Tube polishing machines range from manual units to fully automated systems, each designed to accommodate varying production demands. In a factory setting, the choice of machine can significantly affect productivity and product quality. Modern square and rectangle tube polishing machines incorporate advanced technologies, including automation, programmable controls, and high-efficiency motors. These innovations enable manufacturers to achieve consistent results, reduce labor costs, and increase throughput.
Features of Modern Polishing Machines
1. Versatility Many contemporary polishing machines can handle a variety of tube sizes and materials, making them suitable for a wide array of applications. This flexibility is essential in factories that deal with multiple product lines.
2. Advanced Abrasives The choice of abrasives used in polishing has evolved significantly. Modern machines utilize specialized polishing belts and compounds that enhance the polishing process while reducing wear on the equipment and ensuring a longer lifespan.
3. Automated Systems Automation plays a critical role in the efficiency of tube polishing machines. Automated systems can be programmed to adjust polishing parameters such as speed and pressure, ensuring uniform results across batches and reducing the risk of human error.
square rectangle tube polishing machine factory
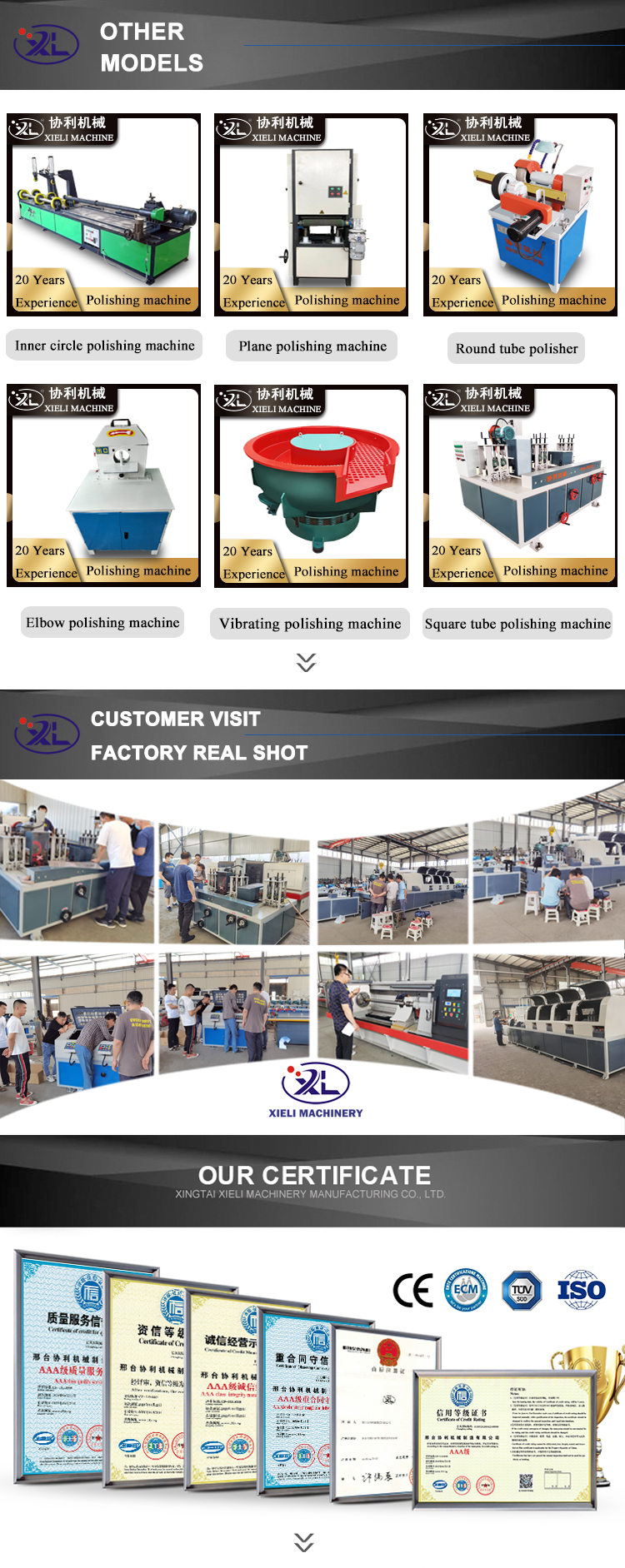
4. Quality Control The integration of quality control systems within polishing machines allows for real-time monitoring of the polishing process. These systems can detect anomalies and provide feedback, ensuring that only products meeting strict quality standards leave the factory.
The Impact on Manufacturing Industry
The significance of square and rectangle tube polishing machines extends beyond mere aesthetics. In construction, for instance, polished tubes not only appear more appealing but also have enhanced properties that increase their durability and resistance to environmental factors. In the automotive industry, polished tubes are critical for both functional and safety reasons, as they often form essential components of vehicles that must withstand harsh conditions.
Moreover, in sectors like furniture manufacturing, polished metal tubes contribute to the overall quality and appeal of the final product. As consumer preferences shift toward high-quality and aesthetically pleasing items, the demand for reliable polishing solutions continues to grow.
Challenges Faced by Manufacturers
Despite the advancements in technology, manufacturers face challenges in the polishing process. Achieving consistency in the finish, managing the wear and tear of machinery, and maintaining operational efficiency are ongoing concerns. Additionally, the initial investment in high-quality polishing machines can be substantial, which may deter smaller businesses from upgrading their equipment.
Future Trends
Looking ahead, the future of square and rectangle tube polishing is poised for further innovation. The rise of smart manufacturing and Industry 4.0 means that future polishing machines may incorporate even more sophisticated features such as IoT connectivity, enabling real-time data exchange and enhanced maintenance scheduling. Furthermore, sustainability will likely play a crucial role in the development of new polishing techniques and materials, promoting eco-friendly practices within the manufacturing industry.
Conclusion
In conclusion, square and rectangle tube polishing machines are essential tools in the modern manufacturing landscape. As industries strive for excellence in product quality and efficiency, these machines will continue to play a vital role. The evolution of tube polishing technology is a testament to the industry's commitment to innovation, ensuring that manufacturers can meet the ever-growing demands of their markets while maintaining a competitive edge. The future looks bright for tube polishing technology, with endless possibilities on the horizon, driving both quality and efficiency in manufacturing.