The Cost of Internal Grinding Machines for Steel Pipes
The manufacturing sector has seen significant advancements in technology, particularly in the realm of machining processes. One of the essential machines in this sector is the internal grinding machine, especially for steel pipes. These machines are critical for achieving precise internal diameters and surface finishes, especially in industries where high tolerances are mandatory, such as aerospace, automotive, and energy. This article explores the pricing trends, factors influencing costs, and the benefits of investing in an internal grinding machine specifically designed for steel pipes.
Understanding Internal Grinding Machines
Internal grinding machines are specialized equipment used to grind the internal surfaces of pipes and tubes. They employ a rotating grinding wheel that is fed into the pipe, allowing for the refinement of inner diameters and enhancing surface finish. These machines can handle various materials, but steel pipes are the most common due to their widespread use in construction, manufacturing, and infrastructure.
Price Range of Internal Grinding Machines
The price of internal grinding machines for steel pipes can vary significantly based on several factors, including the machine’s size, capabilities, and manufacturer. On average, one can expect to pay anywhere from $30,000 to over $150,000 for a high-quality internal grinding machine.
1. Basic Models For smaller machining operations or for those just starting, a basic internal grinding machine may cost between $30,000 and $60,000. These machines typically have limited capabilities and may focus on basic operations without advanced features.
2. Mid-Range Options Mid-range machines priced between $60,000 and $100,000 offer more versatility, allowing for various grinding tasks with a range of pipe sizes. These machines often come equipped with enhanced features such as CNC controls, which improve precision and repeatability.
3. High-End Models For large-scale manufacturing or specialized applications, high-end internal grinding machines can exceed $100,000. These machines are usually equipped with advanced technologies such as automation, robotics integration, and smart diagnostics, which significantly enhance efficiency and precision.
Factors Influencing Costs
Several factors influence the cost of internal grinding machines
steel pipe internal grinding machine pricelist
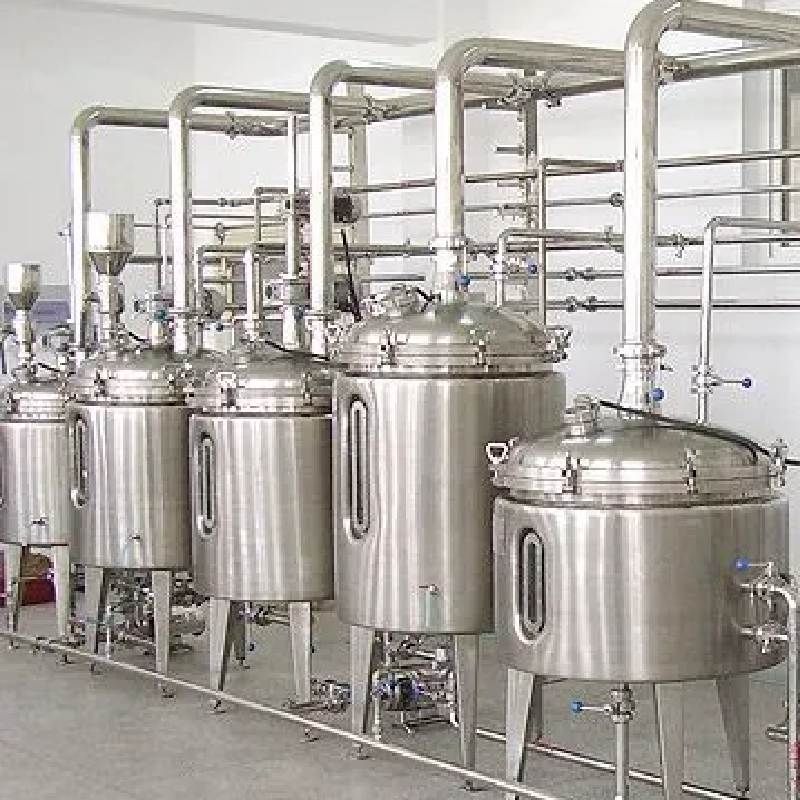
- Technology and Features Machines with advanced technological features such as computer numerical control (CNC) capabilities, automatic loading systems, or integrated inspection systems will generally be more expensive.
- Brand and Manufacturer Renowned manufacturers with a reputation for quality and reliability may charge a premium for their machines. Brands recognized in the industry often offer better support and warranties, making them a worthwhile investment.
- Customization Some operations may require custom-built machines tailored to specific needs, which can greatly increase the price due to the engineering and design work involved.
- After-Sale Support Comprehensive after-sale support, including training, maintenance, and parts availability, is crucial and can factor into the overall cost of ownership.
Benefits of Investment
Investing in an internal grinding machine for steel pipes provides several advantages
- Increased Precision and Efficiency These machines can produce parts with high precision, reducing waste and rework costs.
- Improved Surface Quality A smoother surface finish enhances the performance and longevity of the pipes.
- Versatility Modern internal grinding machines can work with various pipe sizes and materials, making them a valuable addition to any manufacturing setup.
In conclusion, while the initial investment in an internal grinding machine for steel pipes can be substantial, the long-term benefits in precision, efficiency, and quality make it a wise choice for manufacturers aiming to enhance their production capabilities. As the industry continues to evolve, staying updated on technology and pricing trends will ensure that businesses make informed decisions that align with their operational goals.