The Importance of Pipe and Tube Polishers in Industrial Applications
In the realm of manufacturing and metalworking, the finish of products is just as crucial as their functionality. Among the various processes that contribute to achieving a smooth and aesthetically pleasing finish, pipe and tube polishing stands out as an essential practice. A pipe/tube polisher is a specialized machine designed to refine the surface of pipes and tubes, enhancing their structural integrity and visual appeal. This article delves into the significance of pipe and tube polishers, the working principles behind them, and their applications across different industries.
Significance of Pipe and Tube Polishing
The primary objective of polishing pipes and tubes is to remove surface imperfections, such as scratches, oxidation, and other blemishes. A polished surface is not only attractive, but it also plays a substantial role in improving the performance and longevity of the material. For instance, a smoother surface reduces friction, which enhances the flow of fluids within pipes, making them more efficient for processes such as oil and gas transportation or fluid conveyance in various industrial applications.
Moreover, polishing increases the resistance of pipes and tubes to corrosion. Many industries utilize stainless steel and other alloys that naturally resist rust; however, even these materials can develop surface imperfections over time. A high-quality polish creates a barrier that reduces the likelihood of oxidation, prolonging the working life of the pipes. Consequently, industries benefit from lower maintenance costs and decreased downtime due to equipment failures.
Working Principles of Pipe and Tube Polishers
Pipe and tube polishing machines operate by utilizing various polishing techniques that can include mechanical polishing, abrasive blasting, or chemical treatments. Each method has its unique advantages depending on the material type, the desired finish, and the specific application.
pipe tube polisher
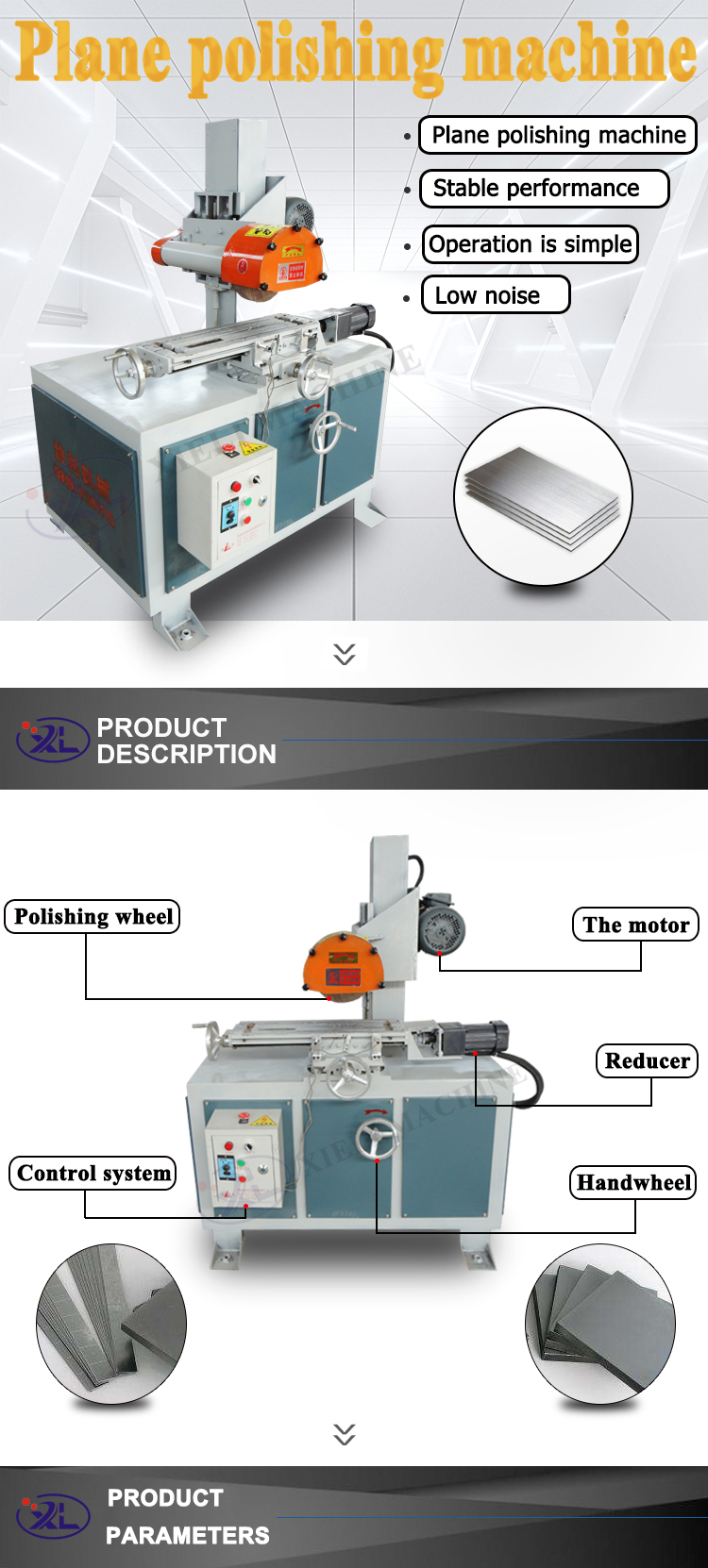
Mechanical polishing is a popular method which employs abrasive materials, such as sandpaper or specialized polishing pads, to grind away imperfections gradually. The surface finish can be precisely controlled during this process, leading to a high-quality sheen on the metal. Additionally, advancements in technology have led to the development of automated polishers that can operate at high speeds, ensuring consistent results and reducing labor costs.
Abrasive blasting, on the other hand, involves propelling a stream of abrasive material against the surface of the pipe or tube at high pressure. This method is efficient for both cleaning and polishing surfaces, particularly for larger diameter pipes that are difficult to handle manually. Finally, chemical treatments employ acid or other solutions to remove contaminants and achieve a bright finish. This approach is often used in industries where hygiene is paramount, such as pharmaceuticals and food processing.
Applications Across Industries
The applications of pipe and tube polishers are vast and varied. In the automotive industry, polished exhaust pipes not only enhance the vehicle's aesthetics but also provide improved performance. In aerospace, polished fuel lines contribute to weight reduction and enhanced fuel efficiency. Similarly, the oil and gas sector relies on polished pipes to ensure optimal flow rates while minimizing the risk of leaks.
Moreover, the food and beverage industry benefits greatly from polished stainless steel equipment. The smooth surfaces prevent bacterial growth and make cleaning easier, ensuring compliance with health and safety regulations. Pharmaceutical manufacturers utilize pipe polishers to guarantee that their equipment meets stringent cleanliness standards as well.
In conclusion, pipe and tube polishers play an indispensable role in enhancing the functionality and durability of metal components. Their ability to provide superior finishes fosters efficiency, prolongs equipment life, and meets the diverse needs of various industries. As manufacturing processes continue to evolve, the demand for high-quality pipe and tube polishing will only grow, underscoring the importance of these machines in modern industrial applications. Whether through mechanical, abrasive, or chemical methods, the end goal remains the same to deliver polished products that meet the highest standards of quality and performance.