Pipe Belt Polishing Machine Revolutionizing Metal Finishing
In the world of metalworking and fabrication, achieving a high-quality surface finish on pipes and tubing is essential for both aesthetic and functional reasons. Traditionally, metal finishing has involved labor-intensive processes using hand tools and chemical treatments. However, advancements in technology have led to the development of the pipe belt polishing machine, a powerful innovation that streamlines the polishing process and enhances productivity in manufacturing environments.
What is a Pipe Belt Polishing Machine?
A pipe belt polishing machine is a specialized piece of equipment designed to polish and finish the surfaces of pipes, tubes, and cylindrical objects. Unlike traditional polishing methods that may involve various hand tools, this machine typically features a belt-driven system that automates the process. The machine consists of a cylindrical belt that moves against the surface of the pipe, effectively removing imperfections, scratches, and oxidation while producing a smooth and shiny finish.
Key Features and Functionality
The primary components of a pipe belt polishing machine include the belt, drive mechanism, and adjustable fixtures for holding pipes securely. The machine operates by rotating the belt around a series of pulleys, creating friction against the surface of the pipe. The speed and pressure can be adjusted based on the material and finish required, allowing operators to achieve the desired results efficiently.
1. Versatility One of the standout features of pipe belt polishing machines is their versatility. They can be used on various materials such as stainless steel, aluminum, and brass, making them suitable for diverse industries including automotive, aerospace, and construction.
2. Consistency Automated polishing ensures uniformity across all surfaces, reducing the risk of human error that is common in manual polishing processes. This consistency is crucial for industries that require high precision and quality control.
pipe belt polishing machine
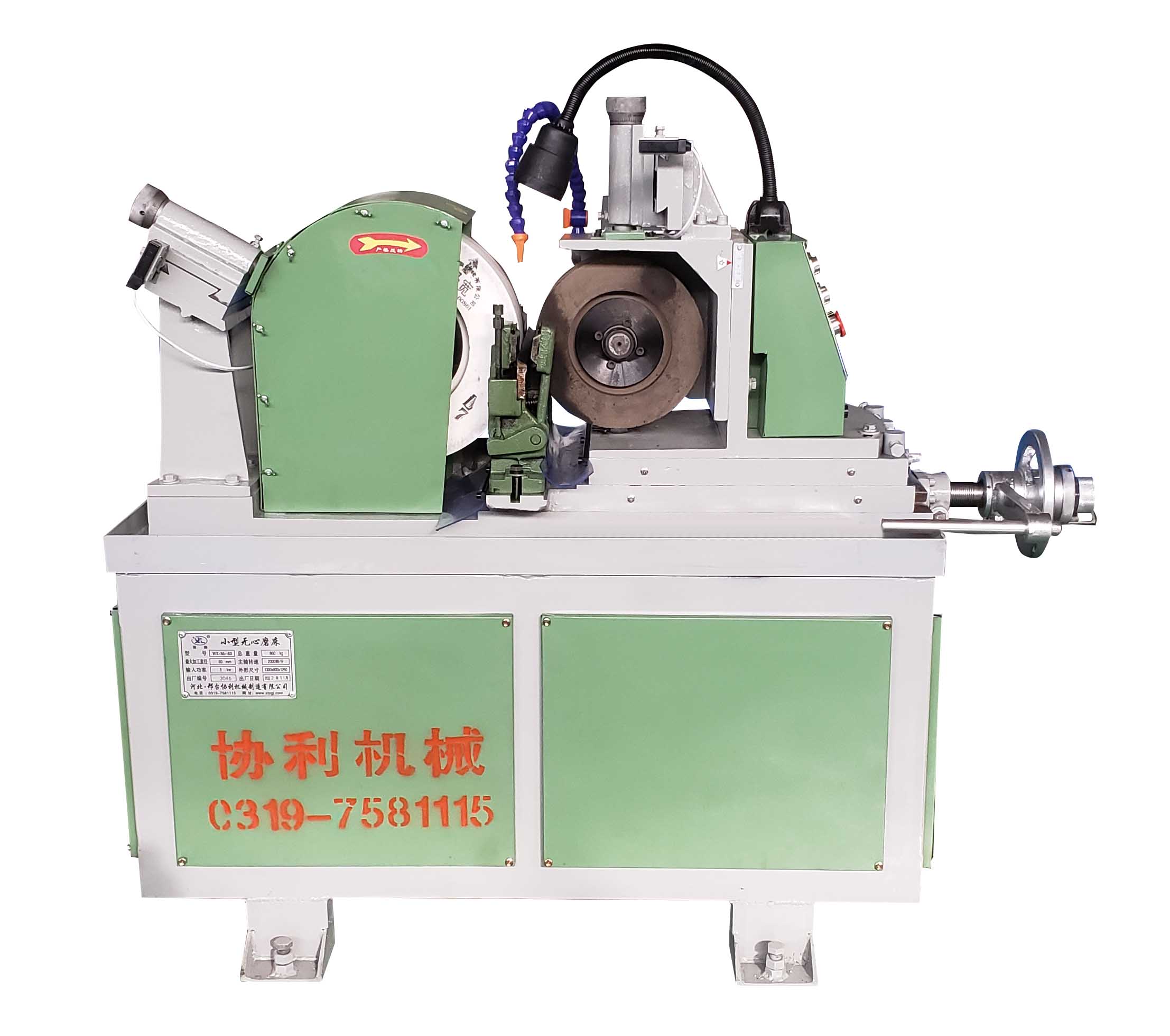
3. Efficiency The speed of the machine allows for rapid processing of multiple pipes, significantly reducing the time required to achieve a polished finish. This efficiency translates into increased productivity and cost savings for manufacturers.
4. User-Friendly Interface Modern pipe belt polishing machines are equipped with intuitive controls and digital displays, making them accessible to operators with varying levels of experience. Many machines also feature safety measures such as emergency stop buttons and protective guards to keep operators safe while working.
Applications in Industry
The applications of pipe belt polishing machines are vast. In the automotive industry, for instance, polished exhaust pipes are not only visually appealing but also enhance performance by reducing friction and enhancing flow. In the aerospace sector, the need for corrosion-resistant surfaces and lightweight materials makes polishing a critical step in manufacturing components.
Moreover, industries involved in the production of medical equipment and food processing equipment rely on polished pipes to meet stringent hygiene and safety standards. A polished surface minimizes the risk of bacteria buildup and ensures compliance with regulatory requirements.
Conclusion
The pipe belt polishing machine exemplifies how technology continues to advance the capabilities of manufacturing processes. By automating and refining the polishing procedure, manufacturers can achieve high-quality finishes more efficiently and effectively than ever before. As industries increasingly recognize the benefits of investing in such equipment, the future of metal finishing looks bright. With ongoing innovations in machine design and functionality, we can expect further improvements in speed, versatility, and ease of use, satisfying the demands of an ever-evolving marketplace.
In summary, the adoption of pipe belt polishing machines is a game-changer for manufacturers aiming to enhance their production processes. By delivering consistent, high-quality finishes in a fraction of the time, these machines not only boost efficiency but also contribute to overall product quality—a win-win for any manufacturing operation focused on staying competitive in today’s fast-paced industrial landscape.