Essential Parts for Cincinnati Centerless Grinders
Cincinnati centerless grinders have been a staple in the manufacturing industry for decades, known for their efficiency and precision in producing cylindrical parts. These machines operate on a distinct principle where the workpiece is held between two rotary wheels, with one wheel driving the workpiece and the other performing the grinding operation. The performance and longevity of a centerless grinder heavily depend on the quality and maintenance of its various components. Understanding these essential parts can help operators optimize their grinding processes and enhance productivity.
1. Grinding Wheel
The grinding wheel is one of the most critical components of a centerless grinder. It performs the actual grinding operation and comes in various sizes and materials depending on the application. The type of bonding agent, grain size, and overall configuration of the grinding wheel can significantly affect the finish of the workpiece. Regular inspection and replacement of worn-out grinding wheels are essential to maintaining the precision and efficiency of the grinding process.
2. Regulating Wheel
The regulating wheel is responsible for controlling the speed of the workpiece. By adjusting the angle and speed of this wheel, operators can influence the rate of material removal and surface finish. The interaction between the grinding wheel and the regulating wheel creates a unique grinding environment conducive to high precision. Maintaining this component involves checking for wear and ensuring proper alignment to facilitate optimal performance.
3. Work Rest Blade
The work rest blade supports the workpiece and helps maintain accurate positioning during the grinding process. It is usually made of high-strength steel and must be set at a precise angle to ensure consistent grinding results. Over time, work rest blades can become worn or damaged, leading to inaccuracies in part dimensions. Regular maintenance and timely replacement are crucial to achieving the desired surface finish and tolerances.
parts for cincinnati centerless grinder products
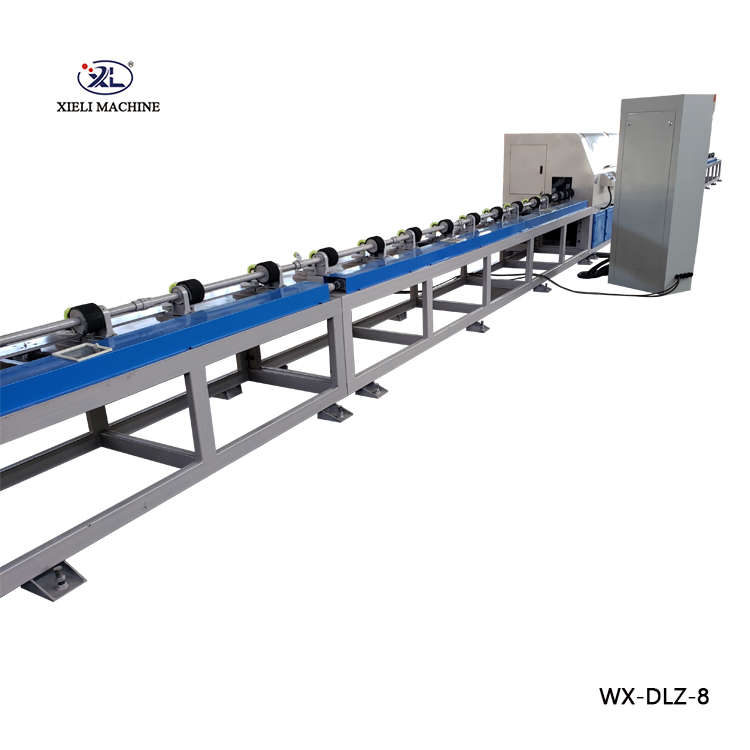
4. Hydraulic System
.
The hydraulic system plays a vital role in controlling various functions of the centerless grinder, including the positioning of the grinding and regulating wheels. A reliable hydraulic system ensures the smooth operation of the machine and enables precise adjustments. Regular checks for leaks, as well as the condition of hydraulic fluids, are necessary to prevent downtime.
5. Alignment Mechanisms
Proper alignment is critical for the effective operation of a centerless grinder. Misalignment can lead to uneven wear on the grinding wheel and poorer part quality. Components like the adjusting screws and alignment fixtures are essential for achieving the correct configuration before commencing the grinding process. Operators should routinely check these mechanisms to maintain grind precision.
6. Cooling System
Grinding generates significant heat, which can adversely affect both the grinding wheel and the workpiece. A robust cooling system helps mitigate this risk by circulating coolant to lower temperatures and improve surface finishes. Regular maintenance of the cooling system, including coolant replacement and ensuring optimal flow rates, is vital for preventing thermal damage and enhancing tool life.
Conclusion
The efficiency and output quality of Cincinnati centerless grinders depend on the upkeep of their essential parts. By understanding the critical components—grinding wheels, regulating wheels, work rest blades, hydraulic systems, alignment mechanisms, and cooling systems—operators can take proactive measures to maintain the machine’s performance. Regular inspections, timely replacements, and adherence to maintenance schedules not only enhance productivity but also help mitigate the risk of costly repairs and downtime. In the competitive landscape of manufacturing, ensuring that your centerless grinder is in top condition can ultimately lead to improved operational efficiency and superior product quality.