Parts for Cincinnati Centerless Grinder A Comprehensive Overview
Cincinnati centerless grinders have long been regarded as the gold standard in precision machining. Dominating the market for decades, these machines are popular among manufacturers seeking efficient and reliable solutions for grinding cylindrical parts. However, the continued performance and longevity of these grinders depend significantly on the availability and quality of replacement parts. This article explores the essential components of Cincinnati centerless grinders, the importance of sourcing quality parts, and the role of exporters in the global market.
Understanding Cincinnati Centerless Grinders
Centerless grinding is a method of removing material from a workpiece with an abrasive wheel. Unlike traditional grinding methods, the part is not held in place by any means but is instead grounded between two wheels—the grinding wheel and a regulating wheel. Cincinnati centerless grinders are particularly known for their ability to handle high-volume production while maintaining precision and efficiency. This makes them integral to industries ranging from automotive to aerospace.
Key Components of Cincinnati Centerless Grinders
To maintain optimal performance, it is crucial to understand the various parts that make up a Cincinnati centerless grinder
1. Grinding Wheel The primary tool that performs the grinding. It can vary in size, material, and grit, depending on the specific application.
2. Regulating Wheel This wheel controls the speed at which the workpiece rotates and helps in positioning the part against the grinding wheel. Its alignment is critical for achieving desired tolerances.
3. Work Support Blade Positioned between the grinding and regulating wheels, the support blade provides critical support to the workpiece, ensuring stability during the grinding process.
5. Hydraulic System Essential for controlling the movement and positioning of the grinder components, a reliable hydraulic system is crucial for achieving operation efficiency and precision.
parts for cincinnati centerless grinder exporter
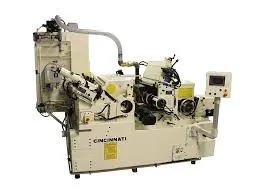
6. Electronics and Controls Modern Cincinnati centerless grinders are equipped with advanced electronic systems that allow operators to fine-tune grinding parameters. This includes speed control, feed rates, and diagnostics.
Importance of Quality Parts
The efficiency and reliability of a Cincinnati centerless grinder depend heavily on the quality of its parts. Using genuine or high-quality replacement components ensures that the machine operates at its peak performance, reduces downtime, and lowers operational costs. Low-quality or incompatible parts can lead to premature wear, decreased productivity, and may even pose safety risks.
Sourcing Parts The Role of Exporters
The global market for centerless grinding machines has led to an increased demand for parts, making exporters crucial players in this landscape. Exporters provide
- Accessibility They bridge the gap between manufacturers and suppliers, ensuring that quality parts are available across different regions, thereby reducing lead times and inventory costs.
- Expertise Many exporters specialize in specific machinery and possess in-depth knowledge of the components involved. Their expertise allows them to recommend suitable parts based on unique customer specifications and applications.
- Compatibility Assurance When sourcing parts, it is vital to ensure compatibility with existing equipment. Reputable exporters often provide guarantees that their parts meet or exceed OEM specifications, allowing manufacturers to maintain or enhance machine functionality.
- Cost-effectiveness By sourcing through exporters, manufacturers can often reduce their procurement costs without sacrificing quality. Bulk purchasing or negotiating long-term agreements can lead to more favorable pricing structures.
Conclusion
Cincinnati centerless grinders remain a cornerstone of precision manufacturing, and the essential role of their parts cannot be overstated. With quality components, operators can ensure their machines function efficiently and effectively, maximizing productivity and minimizing downtime. Exporters play a pivotal role in this ecosystem, providing the necessary parts and support that manufacturers need to maintain their competitive edge. As the machining industry continues to evolve, maintaining a reliable supply chain for quality parts will be vital to sustaining operational efficiency and innovation in manufacturing processes.