Palmary Centerless Grinding Machine Service Ensuring Precision and Efficiency
The precision of manufacturing processes is critical to the success of many industries, particularly those that require high levels of accuracy and surface finish in their components. One of the most vital machines in achieving such precision is the centerless grinding machine. Palmary, a renowned name in the manufacturing of high-quality grinding machines, prioritizes service and maintenance as a cornerstone of their operational philosophy. This article explores the significance of service aspects related to Palmary centerless grinding machines and how they contribute to enhanced performance and longevity.
Understanding Centerless Grinding
Centerless grinding is a manufacturing process that allows the grinding of cylindrical parts without the need for a spindle or fixture to hold the workpiece in place. Instead, parts are fed through the machine and rotated by the grinding wheel. This method offers a continuous flow of production while maintaining high precision. Palmary’s centerless grinding machines are celebrated for their innovative designs, which facilitate fast workpiece changes and minimal downtime.
Importance of Service and Maintenance
Regular service and maintenance are essential for the optimal operation of any industrial machine, especially centerless grinders
. For Palmary machines, proper service routines can significantly affect the machine's performance, accuracy, and lifespan.1. Minimizing Downtime Ensuring that a Palmary centerless grinding machine is well-maintained helps reduce unexpected breakdowns. Downtime can be costly in a manufacturing setting, leading to lost productivity and increased operational costs. Regular inspections and maintenance checks can help identify potential issues before they escalate into major problems.
palmary centerless grinding machine service
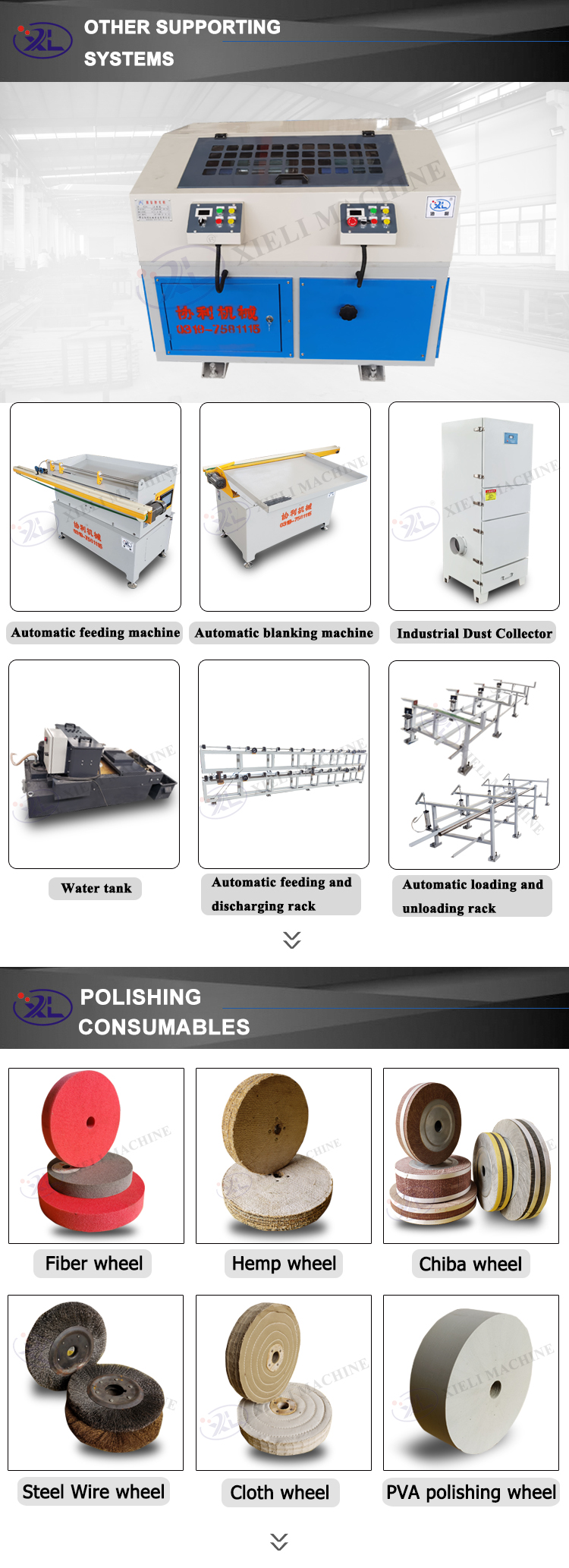
2. Enhancing Performance Like any high-precision machine, a centerless grinder relies on exact measurements and alignments. Periodic adjustment and calibration of the machine are crucial to maintain its accuracy. Palmary’s service includes thorough checks of alignment and leveling, which are critical for the consistent performance and dimensional precision of machined parts.
3. Extending Lifespan The longevity of a centerless grinding machine is largely determined by how well it is cared for. Regular service from certified technicians ensures that wear and tear is addressed promptly. The use of genuine Palmary replacement parts during servicing also plays a significant role in maintaining the integrity of the machine, ultimately extending its operational life.
4. Training and Support Palmary goes beyond traditional servicing by providing comprehensive training and technical support for operators. Understanding the intricacies of machine operation not only enhances productivity but also empowers operators to perform routine maintenance tasks. With well-trained personnel, companies can better manage their grinding processes and address minor issues before they become larger problems.
5. Optimizing Grinding Processes Each manufacturing process is unique, and Palmary understands that operators may require tailored solutions to meet specific demands. Their service team is equipped to provide customized recommendations on grinding parameters, tooling, and workflows to maximize efficiency and output.
Conclusion
For companies relying on precision machining, the significance of effective service and maintenance of their centerless grinding machines cannot be overstated. Palmary’s commitment to high standards in both machine manufacturing and service creates a symbiotic relationship between technology and operators. By investing in regular service protocols and leveraging the expertise of Palmary’s support team, manufacturers can ensure their centerless grinding machines operate at peak performance, achieve desired tolerances, and remain competitive in the ever-evolving market landscape. In an industry where precision is paramount, Palmary’s dedication to service excellence sets them apart as a partner invested in the longevity and effectiveness of their customers' operations.