Understanding Ovality in Centerless Grinding
Centerless grinding is a widely used manufacturing process for providing high precision and excellent surface finishes to cylindrical parts. This technique is particularly important in applications where tight tolerances and consistency are required. However, one of the challenges faced in centerless grinding is the phenomenon known as ovality. This article will delve into the concept of ovality, its causes, effects, and the methods to control it within the centerless grinding process.
What is Ovality?
Ovality refers to the deviation of a circular component from a true circular shape. In simple terms, it's when a part that should be round exhibits an elliptical shape instead. This can lead to significant issues in functionality, as parts may not fit correctly within assemblies or may wear unevenly, leading to increased operational inefficiencies.
In centerless grinding, ovality occurs when the workpiece is not perfectly centered between the grinding wheel and the regulating wheel. As a result, the grinding process does not remove material uniformly around the component. This defect can manifest as increased eccentricity, where the center of the workpiece does not align with the geometric center of the part.
Causes of Ovality in Centerless Grinding
Several factors contribute to ovality during the centerless grinding process
1. Misalignment If the grinding wheel or regulating wheel is misaligned, it can cause uneven grinding. Proper setup and alignment of the machine components are crucial for achieving uniformity.
2. Workpiece Feed Rate The speed at which the workpiece is fed through the grinding zone can also influence ovality. A too-fast or too-slow feed rate may not allow for even grinding, leading to unwanted statistical variations in part geometry.
3. Wheel Wear Over time, grinding wheels can wear unevenly. A worn wheel that no longer maintains its designed profile can lead to irregular grinding results.
4. Material Variability Different materials react differently under grinding conditions. Variability in material properties can affect how much material is removed in each pass, facilitating the potential for ovality.
5. Cooling and Lubrication Inadequate cooling can lead to thermal expansion, which may alter the size and shape of the workpiece. Proper lubrication reduces friction and aids in maintaining consistent dimensional accuracy.
Effects of Ovality
ovality in centerless grinder product
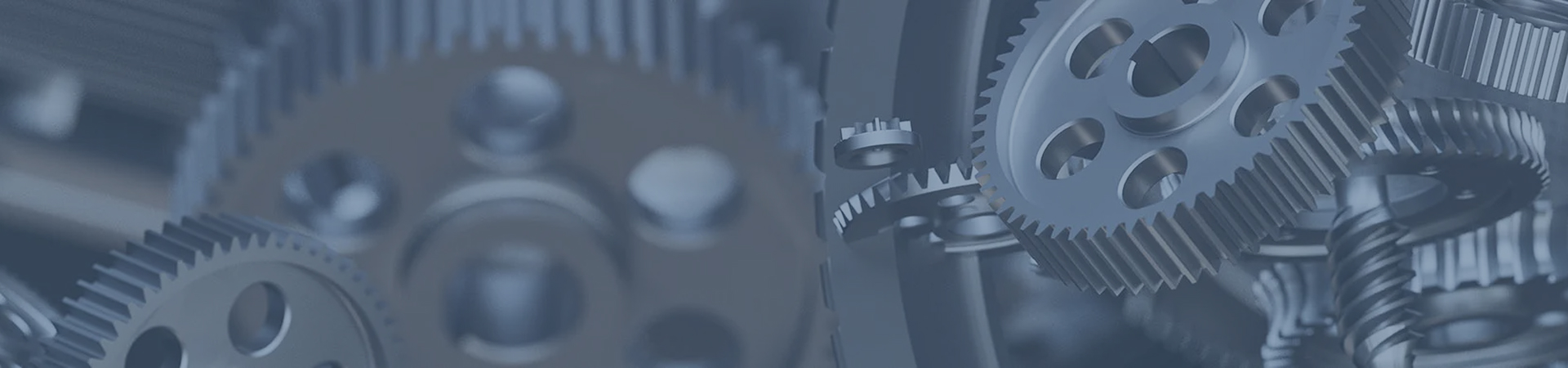
The impact of ovality in machined components can be severe. For instance, parts with oval geometries might exhibit premature wear, leading to higher maintenance costs. In automotive applications, for example, oval bearings may result in imprecise movements, negatively affecting vehicle performance. Furthermore, in precision instrument manufacturing, even a minor deviation can render a product unusable.
From a financial perspective, increased scrap rates and rework due to ovality can significantly elevate overall production costs. Consequently, reducing ovality is a critical objective in the modern manufacturing landscape.
Controlling Ovality
Addressing ovality in centerless grinding requires a comprehensive approach
1. Proper Setup Ensure that the grinding and regulating wheels are correctly aligned. Regular checks and calibrations should be part of maintenance routines.
2. Optimizing Feed Rates Analyze and adjust feed rates to maintain an even material removal rate throughout the grinding process.
3. Monitoring Wheel Condition Regularly inspect grinding wheels for signs of wear. Dressing wheels to maintain their profiles can help ensure consistent performance.
4. Material-Specific Strategies Develop tailored approaches to grinding different materials based on their unique characteristics, reducing the risk of ovality.
5. Cooling Solutions Implement effective cooling and lubrication systems to prevent thermal expansion and uneven wear.
6. Quality Control Employ advanced measurement tools and techniques to monitor dimensions continuously and detect ovality early in the process.
Conclusion
Ovality can pose significant challenges in the centerless grinding process, impacting both the quality of the finished product and the economic efficiency of manufacturing operations. By understanding the causes of ovality and implementing effective control measures, manufacturers can enhance product quality, reduce waste, and ensure that their processes remain competitive. As technology advances, integrating automated monitoring systems and adaptive grinding mechanisms will continue to play a pivotal role in mitigating ovality in centerless grinding.