Understanding Ovality in Centerless Grinding and Its Impact on Pricing
Centerless grinding is a precision machining process used to remove material from the outer diameter of cylindrical workpieces. It is known for its efficiency and ability to produce tight tolerances and smooth finishes. However, one significant challenge faced in this process is ovality, a condition where the finished workpiece exhibits a non-circular shape. This article explores the concept of ovality in centerless grinding, its implications for manufacturing quality, and how it can influence pricing in the industry.
What is Ovality?
Ovality refers to the deviation of a cylindrical part from a perfect circular shape. In the context of centerless grinding, it is the result of various factors such as improper alignment of grinding wheels, uneven force distribution, and discrepancies in the workpiece support. An oval shape can lead to poor performance in applications, as it may cause imbalance, increased wear on machinery, and reduced functionality of components in critical operations.
Causes of Ovality in Centerless Grinding
Several factors contribute to the occurrence of ovality in centerless grinding processes
1. Wheel Setup and Alignment If the grinding wheels are not correctly aligned, it can lead to uneven material removal, causing the workpiece to take on an oval shape. Precise alignment is crucial for maintaining consistent contact between the workpiece and the grinding wheel.
2. Workpiece Support The support mechanisms in place, such as guides and fixtures, must be accurately set up. Any deviation can cause the workpiece to tilt or shift during grinding, resulting in ovality.
3. Force Distribution A balanced distribution of force is essential. If one side of the workpiece is subjected to more force than the other, this imbalance can contribute to the formation of an oval shape.
4. Grind Wheel Condition Dull or worn-out grinding wheels can also lead to uneven material removal, impacting the workpiece's roundness.
ovality in centerless grinder pricelist
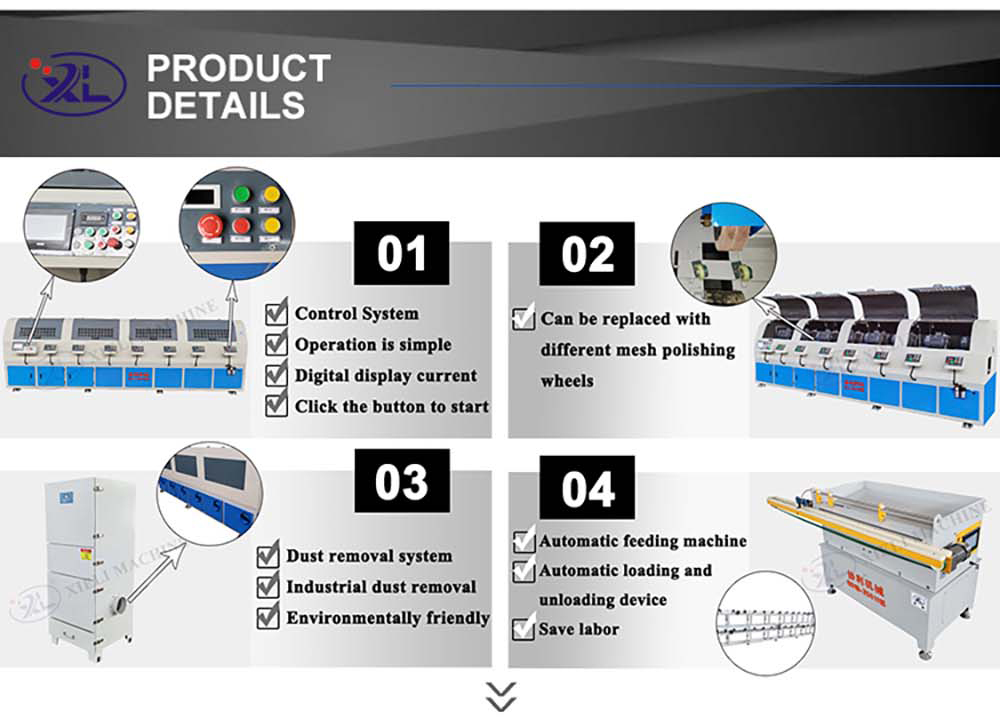
Implications for Quality and Performance
The presence of ovality can have profound implications on the quality and performance of the finished product. Components that are not perfectly round can lead to assembly issues, increased friction, and mechanical failures in applications such as automotive parts, aerospace components, and medical devices. As a result, maintaining stringent quality control measures is crucial for manufacturers to minimize ovality and ensure that products meet the necessary standards.
Pricing Considerations
The pricing dynamics in the centerless grinding industry can be significantly affected by the level of ovality present in the finished products. Here are a few ways how
- Quality Assurance Costs Manufacturers may incur additional costs to monitor and maintain ovality within acceptable limits. This includes implementing advanced measuring techniques and quality control processes, which can increase overall production costs.
- Rework and Scrap Rates If ovality is detected post-production, the need for reworking or scrapping parts can lead to increased expenditure. This not only affects the profitability of a manufacturing operation but can also result in higher pricing for end customers.
- Market Perception Products with a reputation for high precision and quality can command higher prices in the marketplace. If a manufacturer is known for delivering parts with minimal ovality, they can position themselves at a premium pricing tier.
Conclusion
Ovality in centerless grinding is a critical factor affecting both the quality of the finished product and the economic viability of manufacturing operations. By understanding the causes and implications of ovality, manufacturers can take necessary measures to ensure precision in their processes, ultimately influencing pricing strategies and fostering a reputation for quality in the industry. As technology advances, the ongoing quest for precision continues to shape the landscape of centerless grinding, underscoring the importance of addressing ovality to meet market demands.