Understanding Ovality in Centerless Grinder Manufacturers
In the realm of precision machining, centerless grinding stands out as a crucial process for producing cylindrical components. However, one common challenge in this manufacturing technique is the phenomenon of ovality—where the finished parts deviate from perfect roundness. For manufacturers of centerless grinders, addressing ovality is not just an operational concern, but a competitive differentiator.
What is Ovality?
Ovality refers to the condition where a cylindrical workpiece does not achieve a perfectly round cross-section. Instead, the part exhibits an elliptical shape. This can lead to various problems in machining operations, including poor fit, increased wear on machinery, and compromised performance in end applications. In industries where precision is paramount—such as aerospace, automotive, and medical device manufacturing—even minor deviations can result in substantial repercussions.
Causes of Ovality
Several factors contribute to ovality during the centerless grinding process
1. Machine Setup The correct alignment of the grinding wheel and regulating wheel is crucial. Misalignment can lead to uneven pressure on the workpiece as it passes through the grinder.
2. Workpiece Material Properties Variations in hardness or density within the material can yield uneven grinding rates, thus resulting in non-uniform shapes.
3. Inconsistent Feed Rates Inconsistent feeding of the workpiece can lead to varied contact times and pressure, ultimately causing ovality.
4. Worn Grinding Wheels Over time, grinding wheels may wear unevenly, producing subpar finishes and contributing to the issue of ovality.
Addressing Ovality in Centerless Grinding
ovality in centerless grinder manufacturers
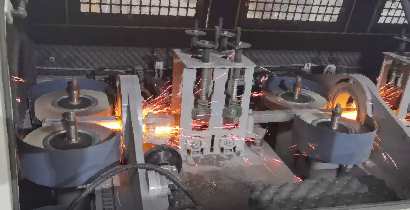
For manufacturers of centerless grinders, minimizing ovality is vital. Here are some strategies to tackle this challenge
1. Precision Calibration Manufacturers should frequently calibrate and maintain the centerless grinding machines to ensure optimal alignment. This includes checking the position of both the grinding and regulating wheels.
2. Quality Material Selection Opting for high-quality raw materials that exhibit uniform properties can significantly reduce the risk of ovality. This may involve sourcing materials from reputable suppliers who provide certifications for dimensional consistency.
3. Optimizing Feed Rates Adjusting the feed rates to achieve a balanced and consistent input can help maintain the desired shape of the workpiece. Implementing advanced programmable controls can enable manufacturers to refine these rates based on real-time feedback.
4. Regular Wheel Dressing Regularly dressing grinding wheels ensures that they maintain their shape and cutting ability. This can help in achieving a smoother finish and reducing the likelihood of ovality.
5. Effective Cooling Systems Implementing cooling fluids and systems during the grinding process can mitigate thermal effects, maintaining dimensional stability throughout the operation.
The Role of Technology and Innovation
In the modern manufacturing landscape, technology plays an essential role in addressing ovality issues. Advanced sensors and monitoring systems can track the dimensions of workpieces in real-time, providing immediate feedback to operators. With these insights, adjustments can be made on-the-fly, significantly reducing scrap rates due to ovality.
Moreover, the advent of automated and CNC-controlled centerless grinders has revolutionized the field. These machines offer unparalleled precision and repeatability, ensuring that ovality is minimized, thereby enhancing output quality.
Conclusion
Ovality remains a significant concern for manufacturers of centerless grinders, but it is also an opportunity for innovation and improvement. By focusing on precision calibration, quality materials, optimized processes, and leveraging technological advances, manufacturers can overcome this challenge. Ultimately, the goal is not just to produce parts that meet specifications, but to ensure a level of quality that sets them apart in a competitive marketplace. As precision demands continue to escalate across industries, addressing ovality effectively will remain a top priority for centerless grinder manufacturers worldwide.