Ovality in Centerless Grinder Factories Challenges and Solutions
In the precision manufacturing industry, maintaining the highest standards of quality is crucial for ensuring product performance and customer satisfaction. One of the critical factors that can affect the quality of cylindrical parts produced in centerless grinding operations is ovality. Ovality refers to the deviation of a circular component from its ideal circular shape, which can lead to poor fit, unwanted vibrations, and premature failure in applications where precision is paramount.
Centerless grinding is a widely used process for producing high-precision cylindrical parts. Unlike traditional grinding methods, where the workpiece is held in a chuck or fixture, centerless grinding supports the workpiece between a grinding wheel and a regulating wheel. This unique setup allows for continuous feeding of parts and is particularly efficient for mass production. However, this method also comes with its challenges, among which ovality is one of the most significant concerns.
Causes of Ovality in Centerless Grinding
The occurrence of ovality in centerless grinding can be attributed to several factors, each of which must be carefully monitored and controlled to minimize its impact. One prominent cause is improper alignment of the grinding wheels. If the grinding wheel and regulating wheel are not perfectly aligned, it can lead to uneven material removal, resulting in a non-circular workpiece.
Another factor contributing to ovality is variations in the material being processed. Different hardness levels or inconsistencies in the material can lead to uneven wear on the grinding wheel, making it difficult to achieve uniform dimensions. Additionally, the use of worn or damaged grinding wheels can exacerbate the issue, as they may not maintain the correct profile needed for precision grinding.
Environmental conditions within the factory can also play a role. Factors such as temperature fluctuations and humidity levels can affect the grinding process, leading to changes in the material properties of the workpiece or inconsistent performance of the machinery.
Addressing Ovality Issues
ovality in centerless grinder factory
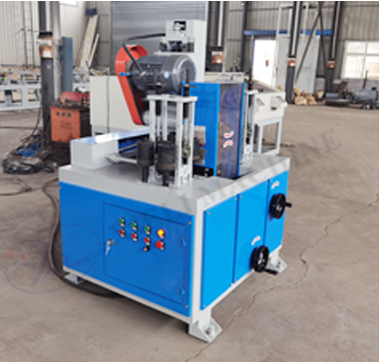
To combat ovality in centerless grinding operations, companies must adopt a proactive approach that includes regular equipment maintenance, stringent quality control measures, and continuous operator training.
1. Regular Maintenance Ensuring that grinding equipment is in optimal condition is vital. Regular checks and maintenance of grinding wheels, bearings, and alignment can prevent misalignment and wear that lead to ovality. Implementing a scheduled maintenance program can help identify potential issues before they become significant problems.
2. Quality Control Measures Establishing robust quality control measures is essential for detecting ovality early in the manufacturing process. Utilizing precision measurement tools, such as coordinate measuring machines (CMM), can help assess the roundness of each workpiece. By tracking this data over time, manufacturers can identify trends that may indicate underlying issues.
3. Operator Training Skilled operators who understand the nuances of centerless grinding are invaluable assets. Regular training programs can help operators learn best practices for setup, operation, and troubleshooting. A knowledgeable operator is better equipped to recognize signs of ovality and take corrective action promptly.
4. Investing in Technology Advanced technologies, such as automated monitoring systems and precision grinding machines equipped with adaptive control systems, can help reduce the incidence of ovality. These technologies can monitor the grinding process in real-time, making adjustments on-the-fly to maintain the desired tolerance levels.
Conclusion
Ovality in centerless grinding operations remains a critical challenge for precision manufacturers. However, by recognizing the causes and implementing effective solutions, manufacturers can significantly reduce the occurrence of this issue. Through regular maintenance, stringent quality control, continuous operator training, and investment in advanced technologies, companies can ensure the production of high-quality cylindrical parts. Ultimately, a focus on minimizing ovality will lead to improved product performance and enhanced customer satisfaction.