The Cincinnati Twin Grip Centerless Grinder Precision Engineering at Its Best
In the sphere of precision machining, few tools hold as much esteem as the Cincinnati Twin Grip Centerless Grinder. Renowned for its reliability and unmatched performance, this machine has become a staple in various industrial sectors, particularly in manufacturing operations that necessitate high levels of accuracy and consistency. With its unique design and advanced engineering, the Cincinnati Twin Grip Centerless Grinder stands out as an essential tool in the arsenal of machinists and manufacturers alike.
What is a Centerless Grinder?
A centerless grinder is a type of grinding machine used to grind cylindrical parts without the need for centers or chucks that typically assist in holding the workpiece in place. The fundamental principle of the centerless grinding process involves the use of two wheels the grinding wheel and the regulating wheel. The grinding wheel is responsible for removing material from the workpiece, while the regulating wheel controls the speed and position of the workpiece as it is fed through the grinder.
The Unique Features of the Cincinnati Twin Grip Centerless Grinder
The Cincinnati Twin Grip Centerless Grinder is distinguished by its innovative twin grip design. This unique feature allows the machine to provide superior support and stability to workpieces, ensuring that they are held firmly in position throughout the grinding process. This level of stability is critical for achieving the precision tolerances that are often required in the production of high-quality components.
One of the significant advantages of the Twin Grip design is its ability to accommodate a wide range of workpiece sizes and shapes. Whether dealing with small, intricately crafted components or larger, heavier pieces, the Cincinnati Twin Grip can handle the task with ease. This versatility makes it an attractive option for manufacturers seeking flexibility in their machining processes.
oem cincinnati twin grip centerless grinder
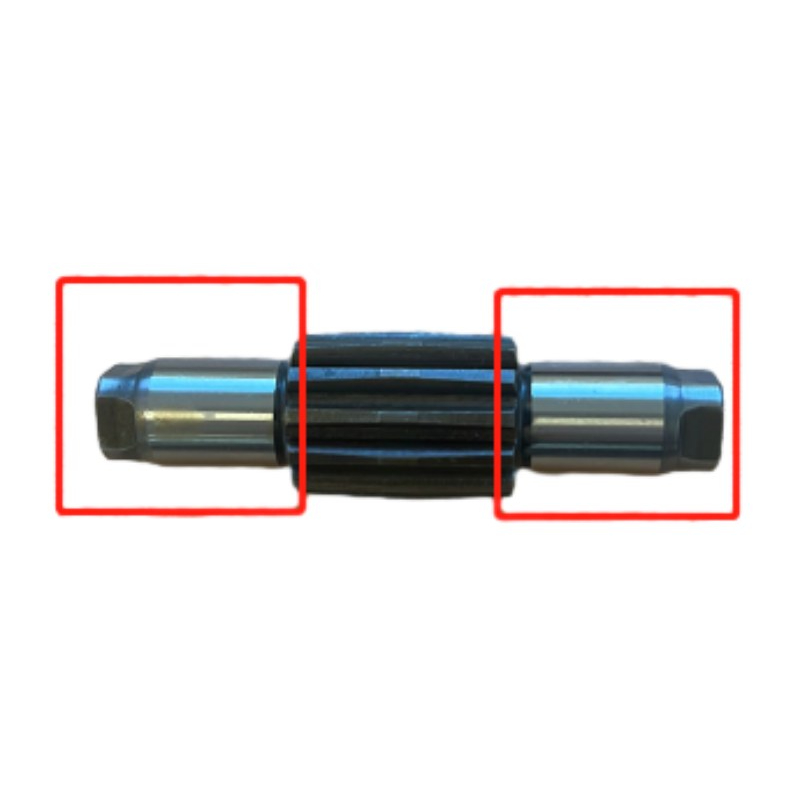
In addition to its gripping mechanism, the Cincinnati Twin Grip Centerless Grinder is equipped with advanced technology that enhances its performance. Features such as automatic grinding cycle control, digital readouts, and programmable logic controllers (PLCs) combine to create a user-friendly interface that simplifies operation and reduces the potential for human error. The result is a machine that not only maximizes productivity but also ensures consistent quality in the final product.
Applications of the Cincinnati Twin Grip Centerless Grinder
The applications of the Cincinnati Twin Grip Centerless Grinder are vast and varied. Industries such as automotive, aerospace, and medical device manufacturing often rely on this machine to produce components that require high levels of precision. Common applications include the grinding of shafts, pins, and bearings, where accuracy is paramount.
Furthermore, the centerless grinding process is ideal for high-production environments where large quantities of parts need to be processed in a short period. The ability to operate continuously and efficiently positions the Cincinnati Twin Grip as a vital player in the realm of mass production.
The Future of Centerless Grinding
As manufacturing technologies continue to evolve, centerless grinding machines like the Cincinnati Twin Grip are adapting to meet the changing demands of the industry. Innovations in automation, data analytics, and machine learning are setting the stage for smarter, more efficient grinding processes. Manufacturers are beginning to incorporate predictive maintenance strategies, reducing downtime and enhancing operational efficiency.
In conclusion, the Cincinnati Twin Grip Centerless Grinder represents a pinnacle of engineering and design in the world of precision machining. Its innovative features, versatility, and reliability make it an indispensable asset in various manufacturing sectors. As industries continue to embrace modernization and efficiency, the role of advanced machinery like the Cincinnati Twin Grip will only become more pronounced, reinforcing its status as a cornerstone of precision engineering. Whether you are a seasoned machinist or a newcomer to the industry, understanding the capabilities and advantages of this remarkable machine can provide valuable insights into the future of manufacturing.