Understanding ODM Ovality in Centerless Grinding
Centerless grinding is a widely utilized manufacturing process aimed at producing precise cylindrical components. One critical aspect of this process that often comes under scrutiny is the Out-of-Roundness Measurement (ODM) ovality, which refers to the deviation of a part from a perfect circular shape. Achieving optimal circularity is essential for ensuring the proper functioning of finished components, particularly in industries such as automotive, aerospace, and medical devices where precision is paramount.
The Importance of ODM in Centerless Grinding
Centerless grinding operates by holding the workpiece between two grinding wheels a regulating wheel and a grinding wheel. This design allows for high production rates and the ability to grind a variety of materials. However, maintaining roundness during the grinding process can be challenging. The term oval indicates that the workpiece, while still cylindrical, has variances in diameter that can affect its performance.
The oval shape can arise due to various factors such as improper setup, wear on grinding wheels, variations in workpiece material properties, and even the design of the centerless grinder itself. These irregularities can lead to increased wear on machinery, higher rejection rates, and ultimately, elevated production costs. For these reasons, monitoring and controlling ODM ovality is a vital part of the centerless grinding process.
Factors Influencing ODM Ovality
There are several factors that influence the ovality of parts produced through centerless grinding. One significant factor is the alignment of the regulating wheel and grinding wheel. If these two wheels are not properly aligned, it can lead to uneven grinding pressures on the workpiece, which may result in ovality.
Another critical aspect is the properties of the workpiece material. Different materials have varying hardness and structural integrity. Softer materials may deform under pressure, while harder materials may chip or crack, both of which can lead to out-of-round characteristics.
odm ovality in centerless grinder
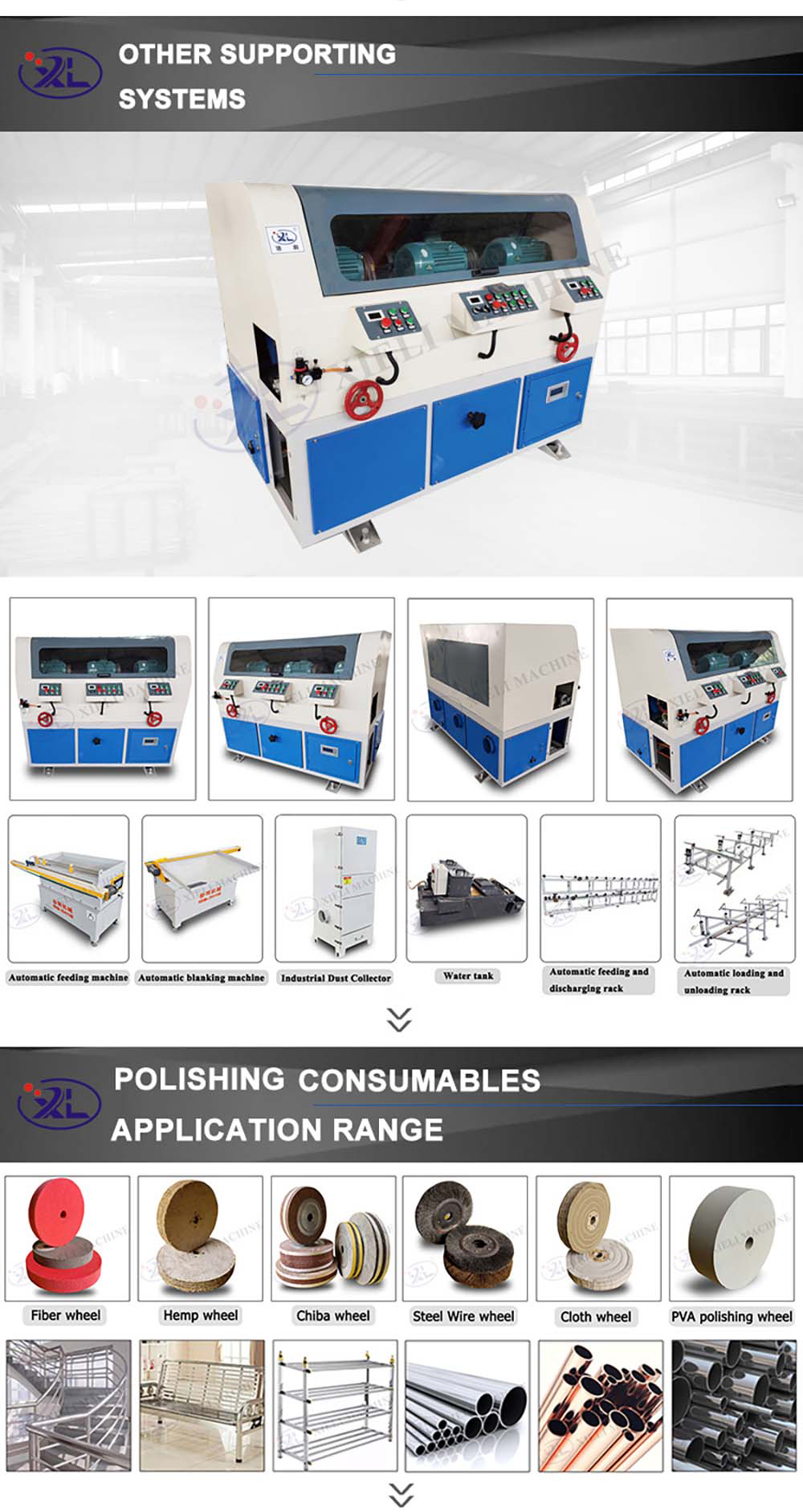
Additionally, the speed and feed rates of the grinding process can significantly affect the outcome. Faster speeds may seem advantageous for efficiency, but if they exceed the material’s capabilities, they can cause heat generation and distortion, leading to ovality. Hence, finding the right balance is crucial to minimize deviations.
Mitigating Ovality in Centerless Grinding
To combat issues related to ODM ovality, manufacturers can implement a series of best practices. Proper machine setup should be prioritized, ensuring that the machines are calibrated according to manufacturer specifications. Regular maintenance of the grinding equipment is essential to prevent wear that can lead to inaccuracies.
Using high-quality grinding wheels suited for the specific material being processed can also mitigate issues. Investing in robust materials and employing precise grinding techniques can greatly improve the consistency of the final product.
Moreover, continuous monitoring and measurement of the components throughout the grinding process enable timely adjustments. Utilizing laser measurement systems can provide real-time data regarding the workpiece’s roundness, allowing operators to make modifications on-the-fly and reduce the incidence of out-of-round components.
Conclusion
In conclusion, achieving consistent ODM ovality in centerless grinding is paramount for ensuring the quality and performance of machined components. Through a comprehensive understanding of the factors affecting roundness and the implementation of best practices, manufacturers can enhance their processes, reduce waste, and ultimately improve the delivery of high-quality products. As technology advances, continued innovation in measurement and grinding techniques will further bolster the capabilities of centerless grinding to produce perfectly round components with minimal ovality.