The Evolution of Old Centerless Grinding Machines
Centerless grinding is a precision machining process used to shape the outer diameters of cylindrical parts, which is vital in various industries such as automotive, aerospace, and manufacturing. Among the various types of grinding machines, the old centerless grinding machines hold a unique place in the history of manufacturing equipment. Despite the advancements in technology, understanding these machines provides valuable insights into both the evolution of manufacturing and the importance of precision engineering.
The Evolution of Old Centerless Grinding Machines
One of the most significant advantages of older models was their simplicity. Operators were able to quickly set up and operate these machines with minimal training. This accessibility made centerless grinding a popular choice for small-batch jobs as well as larger-scale production runs. The reliability of these machines meant that they could operate for long hours with minimal maintenance, which was crucial in a time when downtime equated to lost revenue.
odm old centerless grinding machine
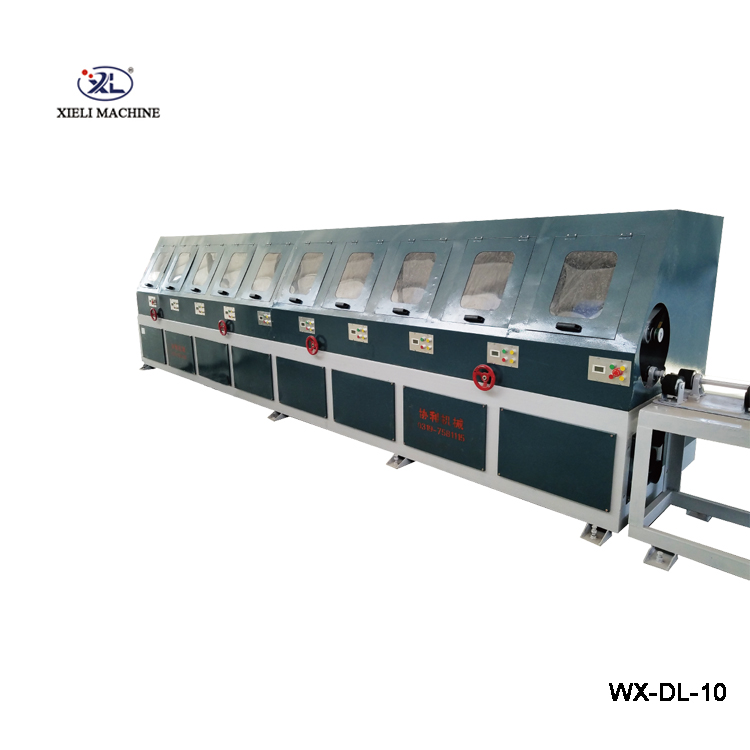
However, the limitations of the old centerless grinding machines also surfaced over time. Their designs lacked the sophisticated controls and automation features that modern machines boast today. For instance, while older machines required manual adjustments for parameters such as depth and speed, newer models utilize CNC technology to provide superior control and consistency. This shift has led to a significant increase in the versatility and capability of grinding operations, allowing manufacturers to tackle more complex geometries and tighter tolerances.
Despite these advancements, there remains a nostalgia and appreciation for older centerless grinding machines. Many manufacturers have adapted their operations to incorporate both old and new technologies, utilizing the robustness of legacy machines alongside the precision of modern ones. This hybrid approach allows for a greater range of production capabilities and can lead to cost savings by maximizing existing equipment.
Moreover, the revival of interest in old centerless grinding machines comes from the current trend of sustainability and longevity in manufacturing. By refurbishing and maintaining these older machines, manufacturers can reduce waste and avoid the environmental impact associated with producing new equipment. This aligns with the growing push towards greener manufacturing practices, ensuring that resources are used efficiently.
In conclusion, while old centerless grinding machines may not match the capabilities of their modern counterparts, they played a pivotal role in shaping the manufacturing landscape. Their simplicity and reliability made them crucial in the early years of industrial production, and their legacy continues to inform and inspire contemporary machining practices. By recognizing the value of these machines, we can appreciate the journey towards precision engineering and the future of manufacturing technology.