Micron Centerless Grinding Machine Service Precision Engineering at Its Best
In the fast-paced world of manufacturing, precision machining is critical to the success of any production process. One essential method that has gained prominence for achieving high precision is centerless grinding. At the forefront of this technology is the Micron Centerless Grinding Machine, known for its efficiency and accuracy. However, like any sophisticated machinery, it requires regular maintenance and specialized servicing to perform optimally. This article will explore the significance of Micron centerless grinding machine service and how it can benefit manufacturing operations.
The Importance of Centerless Grinding
Centerless grinding is a unique machining process that allows manufacturers to create cylindrical parts with precise dimensions. Unlike traditional grinding methods, centerless grinding does not require the workpiece to be mounted between centers. Instead, it utilizes a grinding wheel and a regulating wheel positioned in a specific alignment, enabling the workpiece to be fed through the machine in an automated manner. This setup not only enhances productivity but also significantly reduces the risk of errors typically associated with clamping and manual handling.
Why Choose Micron Centerless Grinding Machines?
Micron has established itself as a leader in the production of centerless grinding machines, appreciated for their durability, precision, and technological advancements. Designed for various industries, including automotive, aerospace, and medical, Micron machines are capable of grinding components to extremely tight tolerances, often within micrometers. Their technology ensures a consistent quality output, which is crucial for industries where component integrity is paramount.
The Role of Regular Service and Maintenance
Despite the robust design of Micron centerless grinding machines, regular servicing is essential to ensure longevity and maintain precision. Over time, wear and tear can affect machine performance, leading to diminished output quality and increased operational costs. Engaging in regular maintenance can help identify potential issues before they escalate, ensuring that the machinery operates at peak efficiency.
micron centerless grinding machine service
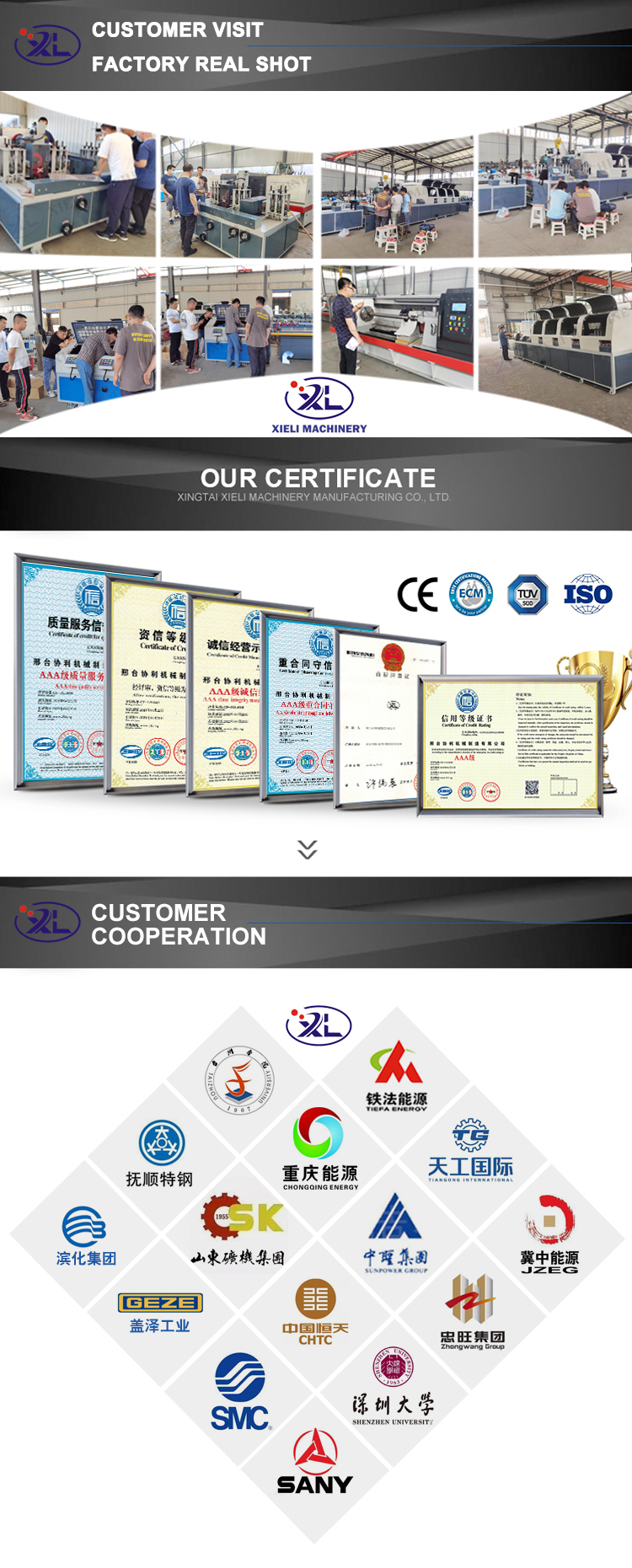
1. Preventative Maintenance Regular servicing helps to mitigate risks associated with unexpected machinery breakdown. This includes checking vital components such as bearings, belts, and gears to ensure they are in optimal condition. Preventative maintenance not only extends the life of the machine but also reduces downtime, which can be costly for manufacturing operations.
2. Precision Calibration The accuracy of the centerless grinding process heavily relies on the alignment and calibration of the grinding and regulating wheels. Professional servicing ensures that these components are calibrated correctly, which is vital for achieving the desired tolerances and surface finishes.
3. Replacement of Worn Parts Components such as grinding wheels and regulating wheels wear down over time. Regular service allows for the timely replacement of these parts, preventing more significant issues down the line and ensuring consistent machine performance.
Engaging Professional Services
Choosing a specialized Micron centerless grinding machine service provider can make all the difference in maintaining your equipment. An experienced service team possesses the knowledge necessary to perform comprehensive inspections and maintenance tasks. They can quickly diagnose issues and implement effective solutions, sparing manufacturers from the potential headaches of operational disruptions.
Conclusion
Micron centerless grinding machines stand as a pillar of precision in modern manufacturing. However, to fully leverage the benefits these machines provide, regular service and maintenance are not merely optional but essential. By investing in professional servicing, manufacturers can ensure that their machinery remains in peak condition, delivering outstanding performance and upholding stringent quality standards. In the competitive landscape of manufacturing, where every micron counts, prioritizing the care of centerless grinding machines can lead to significant improvements in efficiency and product quality.