The Micro Centerless Grinder Revolutionizing Precision Manufacturing
In the ever-evolving landscape of manufacturing, precision machining remains a critical pillar that supports the creation of high-quality components across various industries. Among the sophisticated tools that have emerged to meet the rigorous demands of precision, the micro centerless grinder stands out as a pivotal innovation. Designed for the meticulous grinding of small parts, this versatile machine has transformed the way manufacturers approach high-tolerance tasks.
Understanding Micro Centerless Grinding
Micro centerless grinding is a process that allows for the production of small, cylindrical components with incredibly tight tolerances. Unlike traditional center grinding methods, which require the part to be mounted between centers, centerless grinding supports the workpiece using a roller system, enabling faster processing times and reducing the chance of distortion. This process is particularly beneficial for industries that need high precision, such as aerospace, automotive, and medical device manufacturing.
The micro centerless grinder operates by employing a grinding wheel that shapes the workpiece while it is fed between a regulating wheel and a drive wheel. The regulating wheel controls the rotational speed and feed rate of the part, while the grinding wheel removes material to achieve the desired dimensions and surface finish. This combination allows for continuous, rapid production of even the smallest parts, thereby increasing efficiency and throughput.
Applications of Micro Centerless Grinding
Micro centerless grinders are utilized for a variety of applications, particularly where precise dimensions and surface finishes are critical. Some common uses include
1. Manufacturing of Small Components Industries such as electronics often require tiny shafts, pins, and other components that must adhere to strict tolerances. Micro centerless grinding is ideal for producing these parts consistently.
2. Medical Devices The medical industry relies heavily on the precision of micro-manufactured components. Devices such as stents, surgical instruments, and implantable devices often require parts with extremely tight tolerances that can be efficiently produced through centerless grinding.
3. Aerospace Components The aerospace sector demands a high level of precision due to stringent safety and performance standards. Micro centerless grinders can produce critical components like fuel injectors and valves that need to perform flawlessly under high-pressure conditions.
micro centerless grinder factory
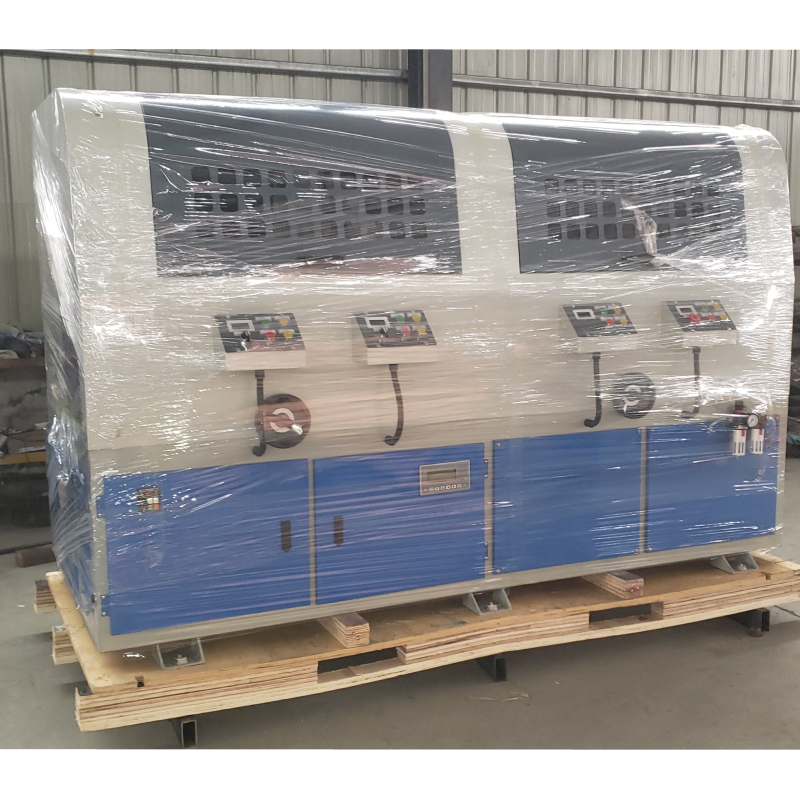
4. Automotive Parts Many automotive applications, particularly in engine manufacturing, benefit from micro centerless grinding. Components like fuel rails, camshafts, and bearing housings require precise dimensions to ensure optimal performance.
The Advantages of Micro Centerless Grinders
The micro centerless grinder offers several benefits that make it an invaluable tool in precision manufacturing
- High Efficiency Because the parts are not constrained by traditional mounting methods, micro centerless grinders can work continuously and are capable of handling multiple parts simultaneously, leading to increased productivity.
- Minimal Setup Time These grinders can be quickly set up and adjusted, allowing manufacturers to switch between different tasks with minimal downtime.
- Superior Surface Finish The grinding process often results in a better surface finish compared to other machining methods, which is crucial for parts that require minimal friction or enhanced aesthetic appeal.
- Increased Material Removal Rates Micro centerless grinding can achieve higher material removal rates, making it an effective choice for both roughing and finishing operations.
Conclusion
As the demand for precision continues to grow in various industries, the micro centerless grinder has become an essential tool for manufacturers looking to stay competitive. Its ability to produce high-quality, precise components in an efficient manner makes it a cornerstone of modern machining processes. Future advancements in grinding technology may further enhance the capabilities of micro centerless grinders, potentially opening new avenues for innovation in precision manufacturing. As we move forward, the continued evolution of these machines will likely redefine the boundaries of what is possible in the world of micro-manufacturing.